- Home
- Equipment Rental
- Service & Maintenance
Equipment Maintenance Software
Offer uninterrupted rental services with a consistently maintained fleet
Maximize the uptime of your equipment by executing on-site or off-site maintenance and service in a timely and efficient manner using Equipment Maintenance Software embedded in Microsoft Dynamics 365 Finance and Supply Chain Management.
Experience our Equipment Maintenance Software firsthand
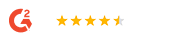
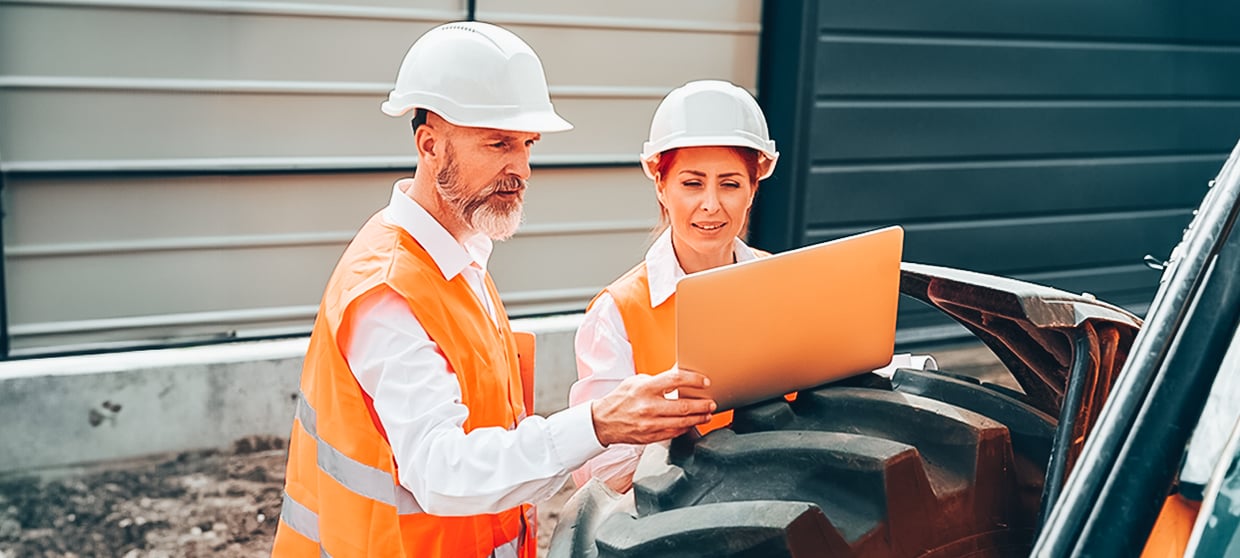
Equipment rental maintenance
Transform this narrative with proper Equipment Maintenance Software to ensure smooth operations in your rental business. Regular maintenance and servicing ensure efficiency, reliability, and customer satisfaction. By minimizing downtime through regular upkeep, you can enhance safety, sustainability, and reputation.
Key Challenges
Increased downtime
Safety risks
High maintenance costs
Key Features
Scroll to
Conduct timely maintenance
Equipment Service Management Software securely preserves records of your equipment's maintenance history on the cloud. Register and monitor your equipment maintenance and set up counter-based maintenance plans for each piece of equipment per the number of operating hours.
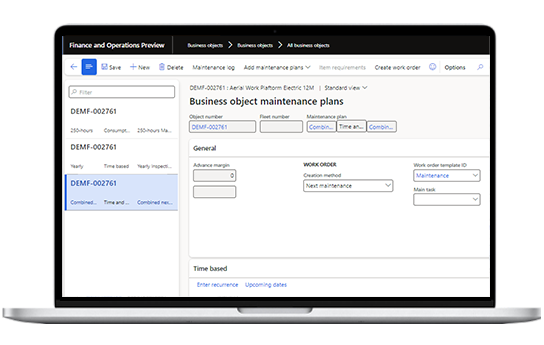
Execute work orders efficiently
Generate work orders automatically based on rental orders and maintenance plans. The progress status of each open, assigned, and pending work order is visible to the planning department and the field service engineers, along with the due dates, timelines, and reference material.
.png?width=770&height=488&name=image-(39).png)
Mobile field service app
Empower field service engineers and technicians to efficiently perform maintenance work on customer sites with an AI-enabled mobile field service app. Remotely capture electronic signatures, record damages, track delivery locations, and access remotely, speeding up on-site maintenance.
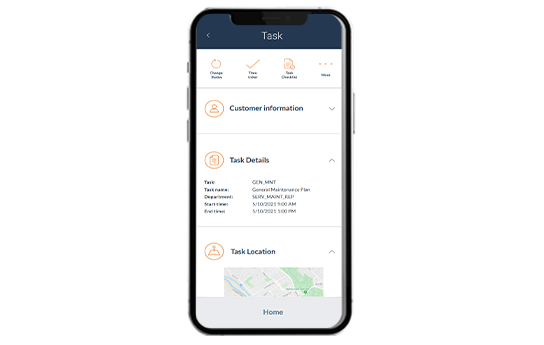
Benefits
The Equipment Maintenance Software helps conduct regular servicing to ensure your assets remain operational when needed, minimizing downtime, and optimizing productivity.
Preserve working capital by addressing issues early through preventive maintenance in the Equipment Service Management Software and avoid costly repairs in the long run.
Conduct time-based or consumption-based maintenance and manage scheduled (preventive and routine) and unscheduled (corrective, delayed, and emergency) maintenance plans.
Well-maintained equipment logged in the Equipment Service Management Software operates more safely, reducing the risk of accidents and injuries for operators and field workers.
Timely maintenance and reliable equipment ensure consistent performance, fostering client trust and satisfaction, thereby increasing customer loyalty and repeat business.
Proper maintenance safeguards the integrity of machinery, extending its lifespan and maximizing the ROI, attracting clients who value reliability, safety, and efficiency in their equipment.
Features
Service Execution

Service Execution
Maximize the uptime of your rental equipment by executing timely maintenance and servicing on-site or off-site using the Equipment Service Management Software.
Service Order Management

Service Order Management
Use the service plan board in the Equipment Maintenance Software to get a graphical summary of each work order, based on which planners can assign tasks to technicians.
IoT-driven Maintenance

IoT-driven Maintenance
Utilize telemetry feeds from rental equipment to establish maintenance counter plans (operating time, counters), ensuring efficient and timely repairs and services.
Field Service Management

Field Service Management
Reduce delays, errors, and rework for field service engineers by using insights from the Equipment Maintenance Software to ensure they are in the right place, at the right time.
Centralized Database

Centralized Database
Utilize the Equipment Maintenance Software to eliminate paper trails and errors with auto-triggers, workflows, forms linked with customer records, and centralized data.
Frequently asked questions
What service execution or maintenance plans do you support?
The Equipment Service Management Software supports a wide range of service executions or maintenance plans. You can conduct preventive and corrective maintenance that can be time-based, consumption-based (meter-based), or related to recalls. Some of the maintenance tasks you can conduct include inspection of the rental object, damage repairs, equipment enhancements or updates, and spare parts changes. You can set up the maintenance plans to best support your business requirements.
Can the software integrate with the Internet of Things (IoT)?
Yes, the Equipment Maintenance Software can integrate with IoT. The IoT devices can automatically update the meter parameters based on which a work order can be generated to perform a service job. You can also utilize the telemetry feeds from the equipment to monitor equipment health and detect variances. You can schedule preventive maintenance by regularly updating equipment usage meters connected to maintenance plans, which can be set based on time, consumption, or both if required.
Are spare parts information always available when performing the service?
Yes. The spare parts necessary to perform a service job are part of the Master Planning capabilities in Microsoft Dynamics 365 Finance and Supply Chain Management. This capability can be combined with the Inventory Management functionality to transfer the spare parts from the central warehouse to the service van of a field technician. The data offered by the Equipment Service Management Software improves the first-time-right percentage and allows technicians to know the spare parts required before maintenance, preventing time loss and rework.
How do you integrate skills and capabilities to perform service jobs?
If special requirements (such as skills and certificates) are necessary to perform a job, selecting only those who meet these requirements with advanced search options within the Equipment Maintenance Software is easy. Additionally, with efficient work order management, your planners can view the availability and capability of technicians and assign tasks accordingly. Planners and technicians can also document and view the progress of equipment maintenance using the service plan board and update the task status.
Resources
Scroll to
Project-Driven Solution in Dynamics 365 F&SCM Factsheet
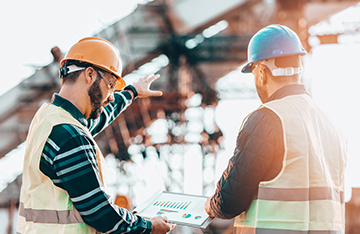
Service-Driven Solution in Dynamics 365 F&SCM Factsheet
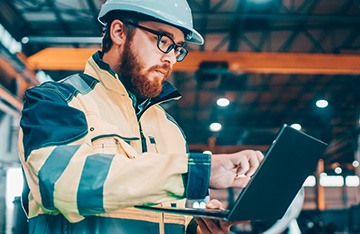
Equipment Rental Software Buyer’s Guide
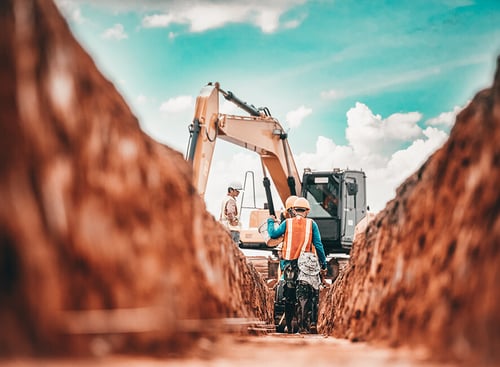