10 Challenges of Disconnected PLM and ERP Systems for Dynamics 365 Users
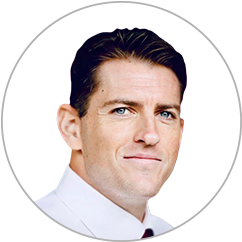
Table of contents
Product lifecycle management (PLM) and enterprise resource planning (ERP) are well-known solutions for manufacturing companies. Both possess critical product-related data and are used daily by engineers and manufacturers. Typically, the engineering process begins in the CAD and PLM, and Dynamics 365 relies on the product provided by your PLM to optimize the company's manufacturing and logistics.
Having no connection between your PLM and Dynamics 365 ERP will eventually slow you down and give birth to complex challenges that exacerbate with time.
With 20+ years of manufacturing industry expertise, we help global businesses integrate their PLM systems with Dynamics 365 ERP. In our experience in providing PLM-ERP integrations, we have witnessed the common issues manufacturers face with disconnected PLM and ERP systems.
This article will discuss the top challenges you, as a manufacturing business, will experience by not integrating your PLM with Dynamics 365.
Top 10 challenges manufacturers face by not integrating PLM with Dynamics 365 ERP
1. Manual import processes with increased workload
With a manual data import process, items must be created in Dynamics 365 ERP separately, increasing the workload. Any changes or updates to these items must be made in the ERP, doubling the effort.
The product items are not engineering-controlled, and teams must manually check every piece of data for errors or outdated information, which is tedious and inaccurate.
2. Data duplication due to no ownership
Disconnected PLM and ERP means there is a lack of data ownership between the PLM system and Dynamics 365 ERP. Data duplication could occur without control over product data, leading to double entries and confusion.
Additionally, with scattered data in your PLM and ERP, certain data could be overlooked or forgotten, resulting in data loss.
3. Inability to transfer and manage bill of materials
Bills of materials (BOMs) are everywhere - PLM, CAD, drawings, and ERP systems like Dynamics 365. Manufacturing companies must maintain BOMs across multiple systems and have one 'ultimate single BOM,' the 'to be built' version.
From prototypes to the final versions of products, there could be several updates in the BOM, which, if not communicated, negatively impact your manufacturing business. Having no connection between your PLM system and Dynamics 365 ERP makes it difficult to manage BOMs. These inconsistencies with inaccurate BOMS results in longer project duration and higher holding costs due to poor planning.
4. Lack of visibility due to inconsistent supply chain
If your PLM system is not well-connected to Dynamics 365, you won’t have a global view of your product data. You do not have the end-to-end visibility of your product journey, which is critical for error-free manufacturing.
Without complete visibility into the data residing in PLM and Dynamics 365, you won’t be able to identify the root causes of product defects/issues and resolve them. This impacts your entire supply chain, leading to lags in procurement, product reworks, and delivery delays.
5. Operational delays due to slow processes
Before reaching the end customer, a product goes through several stages – from design to distribution. However, with disconnected systems, you may not have a quick view of the product stage or a channel to communicate product revisions, increasing the response time.
You cannot access real-time data changes or transfers, making it challenging to stay updated on the product's status. Product release processes are siloed with multiple legal entities, causing downstream problems and revenue loss.
6. Failure to maintain data quality and integrity
Without integrating your PLM with Dynamics 365, different data resides as islands in separate systems, making it a cumbersome process to maintain the quality and integrity of the data.
Without an integration that could validate the data transfer from the PLM to the ERP, you risk data changes that could remain undocumented. Any compromise in product data quality directly impacts the product, causing faulty products.
7. Engineering and logistics confusion due to communication gaps
There is no unified access to the product data as the engineers work in the PLM system, and the logistics team operates in the Dynamics 365 environment. With no structured process to handle engineering changes, bills of materials, etc., you, as a manufacturer, will find it challenging to move equipment from the shop floor to production operations.
When data changes are not communicated on time, it leads to incomplete, outdated, or incorrect product specifications, halting your production.
8. Tracking product revisions, versions, and changes
In manufacturing, products are continuously updated and undergo several iterations or changes before reaching the finalized version. This new product version impacts all the associated components of the product, such as the BOMs, routings, and documents.
If you cannot track the changes made to the product, the manufacturing teams will be unaware of product changes and may use outdated BOMs. Without streamlined communication from your PLM to Dynamics 365, you create incorrect products, wasting costs, time, and resources.
9. Additional costs and expenses due to process lags
By not integrating your PLM with Dynamics 365, you spend much more capital and resources on procurement and raw materials. Without data accuracy, your procurement team cannot securely place their purchase orders, causing raw material shortages. This increases the lag time and destabilizes your daily manufacturing operations.
You lose money in either fixing, inspecting, or recalling the product. And this comes with complex coordination with all your distributors, customers, and legal teams.
10. High time to market and decreased productivity
The gap between your PLM and ERP relates to your product's time to market (TTM). A disconnected PLM system and Dynamics 365 ERP increases the time required to bring a product from conception to market availability due to missing information, process inefficiencies, and cumbersome operations.
Your engineering and manufacturing teams are overloaded with manual tasks related to updating, transferring, and accessing data in the PLM and Dynamics 365. This prolonged time to market sets you behind your competition, and you may lose a significant amount of potential market share.
Integrate your PLM system with Dynamics 365 now
If you are looking for a PLM integration for Dynamics 365 ERP (D365 Finance and Supply Chain Management or D365 AX), check out our PLM-ERP integration solution embedded in Dynamics 365. As a preconfigured solution with accelerated implementation templates for major PLM providers, the solution significantly reduces your time to market.
Our PLM-ERP integration solution is a one-time setup that runs smoothly in the background once implemented. Offering a seamless connection between your PLM and Dynamics 365 ERP, the integration automates multiple processes in one go.
We offer out-of-the-box PLM-ERP integrations for PLM systems: Siemens Teamcenter and PTC Windchill. If you use any other PLM, PDM, or CAD system, you can adopt our PLM integration framework that is easily configured based on your business requirements.
You can explore more about our PLM integration solution embedded in Dynamics 365 in the solution factsheet below.