PLM, PDM, PIM, CAD, MDM: Why Connect Them to the ERP and How Are They Different?
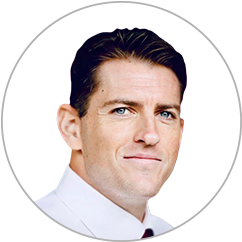
Table of contents
As a modern manufacturing business, you could be utilizing more than one system to manage and control different processes. For the engineering and design functions, you could have the CAD, PDM, and PLM systems; for data management, you could have MDM and PIM systems; for transactions, the ERP.
But what are all these systems? With different systems to manage distinct but vital processes of your business, it could be overwhelming to know the function and role of each system to utilize its maximum potential. Additionally, you must ensure they are connected in some way to guarantee smooth communication between departments.
With deep expertise in the manufacturing industry, we at STAEDEAN have global experience of over 17 years in offering PLM-ERP integration embedded in Dynamics 365 ERP.
This article will share the distinction between some of the commonly used systems by discrete manufacturers and process manufacturers and the need to connect them to your ERP.
What are some of the common systems used by manufacturers?
1. PLM – Product Lifecycle Management
PLM software is a solution that manages all the information and processes of product development across all stages from ideation, designing, manufacturing, maintenance, and disposal across globalized supply chains. This includes the data from items, parts, products, documents, requirements, engineering change orders, and quality workflows.
It has all your engineering information related to product design and is more flexible as it integrates data, workflows, business systems, and people in a value chain to manage the entire lifecycle of a product efficiently and cost-effectively.
Commonly beneficial for all the stakeholders, PLM systems are operated and used by engineers and product designers.
A few PLM providers in the market today are Autodesk Vault, PTC Windchill, Propel, Siemens Teamcenter, Dassault systems, and Ansys.
2. PDM – Product Data Management
Product data management is a system used for managing the design data and engineering processes in a central location. It is a business function that refers to the management and publication of product data. In software engineering, it is also known as version control.
Engineering teams use PDM software to organize product-related information, track revisions, collaborate, manage change orders, generate bills of materials (BOMs), and more. As it is a single source for project data, it saves time and effort for the engineers and avoids chances of errors.
Examples of PDM solutions are Siemens Teamcenter, Autodesk Fusion 360, SolidWorks PDM, and PTC Windchill.
PLM versus PDM
PDM systems could be considered a component of the PLM solution. PDM is an engineering tool primarily used for tracking technical data, whereas PLM is used to track all product data beyond the engineering and development phases of a product.
3. PIM – Product Information Management
PIM is a technical solution that connects internal sources of product data with external sales channels. It is used to manage all the information required to market and sell products through distribution channels. The hallmark of PIM systems is to support a multichannel marketing and distribution strategy and is relevant for businesses that sell products through various sales channels.
It supports data from multiple sources, such as different suppliers, supply chains, points of sales, etc., and ensures that the data is consistent and up to date in all places.
A few PIM solution providers include Informatica, Akeneo, Pimcore, and PIMworks.
PLM versus PIM
Compared to PLM, PIM is different as it focuses on the current information about a product while offering marketing information that could help sales and manage omnichannel data – something which isn’t available in a PLM system.
4. MDM – Master Data Management
A master data management solution is used to ensure the uniformity, accuracy, and consistency of all the master data of a particular business that is accessible to everyone within the organization. Master data is the uniform set of identifiers that describes different entities of an enterprise, such as customers, prospects, suppliers, products, and so on.
With an MDM system, a single master record is created for each person, place, or item in a company using both internal and external data sources. The data is enriched and is a trustworthy and reliable source of maintaining and distributing information throughout the organization, improving accuracy.
We at STAEDEAN offer Master Data Management solutions to implement data governance and streamline master data management within Dynamics 365 ERP.
PLM versus MDM
While PLM, PDM, and PIM are specific to managing product data and product lifecycles, an MDM system can be used by any business, regardless of the industry type.
5. CAD – Computer-Aided Design
Computer-aided design is a technique to make use of computer-based software to digitally create 2D drawings and 3D models of products before they’re manufactured. In simple words, it is the digital way of drawing something on a computer.
This software is commonly used by engineers and designers to share, review, modify and make multiple iterations and revisions of different products. Designers or facility planners can easily edit drawings and generate BOMs, and it is particularly useful in the automotive and construction industries.
With an electronic file output format in CAD, the designer's workflow is streamlined, and productivity is increased as the quality of the product design is precise and improved.
Some examples of CAD systems are SolidWorks, Siemens NX, Inventor, and AutoCAD.
PLM versus CAD
The processes in a CAD system usually occur prior to the PLM phase, as it is purely used in the designing of the product. CAD only focuses on the technical drawings of the product and can be considered a component of PDM, whereas the PLM system is more comprehensive.
6. ERP – Enterprise Resource Planning
An enterprise resource planning system combines all the core processes of a company, such as HR, finance, sales, inventory, planning, marketing, procurement, manufacturing, services, supply chain, logistics, and shipping, in a single system.
With a goal to source and sell products, the ERP system manages the product manufacturing process by handling the daily planning and transactions across the organization.
It is a process used by companies to manage and integrate the important parts of their businesses in real-time and contains transactional data that focuses on the entire financial and supply chain management regarding product manufacturing.
ERP systems can be on-premises or cloud-based, with cloud-based applications experiencing significant growth and demand in recent years due to easy information access and scale-up.
Some ERP providers are Microsoft Dynamics 365, Oracle, SAP, and Infor.
PLM versus ERP
In an ideal manufacturing setup, product data usually moves from PLM to the ERP to manufacture a product. PLM is where the product virtually exists, and when it enters the ERP, the actual manufacturing process begins. While PLM deals with the lifecycle of the product, the ERP has data related to costs, production orders, and procurement related to the particular product version.
Below is an image that depicts how the different manufacturing software systems exist
Why should manufacturing businesses connect their PLM, PDM, and CAD systems to ERP?
As an enterprise involved in manufacturing products, you could have one or more of the systems discussed above. However, while you could have the latest technology and software to support your processes, you risk operating in silos as the multiple systems you use are not connected to one another.
An easy way to fix this challenge and streamline your processes would be to connect your different systems to your ERP — the technology that manages the execution and manufacturing side of your business. You could invest in an integration solution that connects your PLM, PDM, or CAD to the ERP.
For instance, some of the benefits of integrated PLM and ERP are:
- Increased operational efficiency with real-time access to data
- Smoother supply chain with reduced errors
- Strengthened interdepartmental collaboration with streamlined communication
You can analyze the need for a PLM-ERP integration yourself with the 8 signs a manufacturing business must integrate PLM and ERP.
How do you select the right PLM integration solution?
Whether you’re looking to integrate your PLM, PDM, CAD, or MDM system with your ERP, you must get a few things right.
i) Analyze your current PLM and ERP systems, and look for vendors that offer integrations supporting those systems
ii) Identify the data you want to transfer from the PLM to the ERP
iii) Define the nature of the integration solution you require
iv) Set timelines for the implementation
How can we at STAEDEAN help with a PLM-ERP integration solution?
With nearly two decades of global experience, we offer PLM-ERP integration for all PLM systems with the ERP Dynamics 365 F&SCM or Dynamics AX 2012.
We offer out-of-the-box PLM integrations for Siemens Teamcenter and PTC Windchill and also have experience in PLM integrations with 3DX Dassault. Additionally, we provide a PLM integration framework that is easily configurable and can be adapted for any PLM system.
While we specialize in PLM-ERP integrations, we also offer configurable integrations for PDM, CAD, and MDM systems.
Ready to enhance your manufacturing business’s efficiency today?
If you are on Dynamics 365 ERP, you might be interested in exploring more about the PLM-ERP integration we offer for Dynamics 365. As a robust, configurable, and easy-to-use solution, it has no coding hassles with a quick implementation time.
You could explore more about our PLM-ERP integration solution in the factsheet, which would offer you more insight on:
-
What the PLM integration solution can do for your business
-
Benefits of PLM-ERP integration
-
Features of a standard PLM-ERP integration