PLM-ERP Integration: Boundaries, Ownership, and Maintenance of Product Data
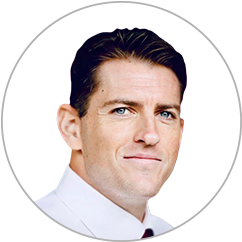
Table of contents
Integrating PLM and ERP enables businesses to connect their engineering and manufacturing worlds. A PLM-ERP integration solution has numerous benefits, such as streamlined communication and visibility into your product’s lifecycle. However, the integration depends on product data in the PLM and ERP. Without knowing the nature of the data in the two systems, you might end up with an integration solution that will not address your integration needs completely.
As experts in the manufacturing industry, we at STAEDEAN have over 19 years of global experience in offering PLM-ERP integration embedded in Dynamics 365 ERP.
In our experience integrating PLM and ERP systems, we’ve noticed one thing cropping up several times — companies are not sure where to draw the lines, how much data to integrate, and how data ownership works after the integration.
This article will share information on where you, as a manufacturing company, must draw the boundaries between your PLM and ERP systems when modifying, maintaining, and owning product data.
Let’s begin by taking a quick look at the basics.
What is PLM and what data does it own?
A PLM (Product Lifecycle Management) system manages complex product development across all stages: ideation, design, maintenance, and disposal.
It is a software solution with all your engineering information related to the product design and is more flexible. It integrates data, workflows, business systems, and the responsibilities of people in a value chain to manage the entire lifecycle of a product efficiently and cost-effectively.
What is ERP and what data does it contain?
The ERP (Enterprise Resource Planning) business system combines a company's core processes, such as HR, finance, procurement, manufacturing, services, supply chain, logistics, and shipping, into one system.
Companies use it to manage and integrate the essential parts of their businesses in real-time. ERP contains transactional data on the entire financial and supply chain management regarding product manufacturing.
The need for PLM, ERP, and integrating the two systems
Businesses involved in manufacturing products often depend on the PLM and ERP systems to carry out different processes.
The earlier stages of a product (designing and engineering) are handled in the PLM, and the later steps of a product (sourcing, warehousing, and manufacturing) are taken care of in the ERP. You require both systems to handle your business operations as a manufacturing business.
However, you can double the benefit from both ERP and PLM by connecting them through a PLM-ERP integration solution that allows data flow between the two systems.
PLM and ERP integration: where do you draw the boundaries?
While integrating your PLM and ERP systems may seem like a straightforward affair, most companies tend to overlook the individual systems and understand how they handle data. To get the maximum ROI out of your PLM-ERP integration, you must first understand how the two systems handle data, which actions you can do where, and then begin exploring integration options.
What data can you maintain in the PLM and ERP?
Broadly speaking, in an average manufacturing business, two types of items exist:
i) Engineering items: These refer to the finished goods to be manufactured where design is part of the engineering team. These items reside in the PLM and are data related to the product's design specifications, drawings, descriptions, properties, and engineering iterations.
ii) Standard items: These refer to the list of parts required to make the finished product. They are sub-parts purchased from suppliers. Examples include consumables, fixtures, tools, packing items, and key assembly items. Standard items are created in the ERP item master to be utilized for operations.
Depending on your specific business situation and the legal entities you operate with, you could have more item types. It's important to know that engineering items exist in the PLM system, so any related changes must be made in the PLM. The ERP must manage any modifications to the standard items.
How to handle changes in product data after PLM-ERP integration?
With the discussion around data being maintained in PLM and ERP comes the question — how do you manage product data changes after the PLM-ERP integration?
All product data initially created in the PLM will continue to be maintained in the PLM. For instance, data related to product color, versions, etc., will first be updated in the PLM and released to the operational companies. Similarly, all transactional data will continue to be maintained in the ERP, and changes related to costing, warehousing, etc., can be directly done in the ERP.
If departments operating outside the PLM system (sales, sourcing, etc.) want any changes in the engineering items, they must initiate it through an engineering change request (ECR). The ECR might be a change, fix, or recommendation for new or existing products.
The ECR is sent to the engineering team to assess the impact of the change and do the necessary approvals via defined workflows, which turns into an engineering change order (ECO). After implementing the proposed changes, the ECO is sent through a workflow to the relevant stakeholders, and the updated information is shared with the ERP(s).
What data can you export from the PLM to the ERP with an integration?
Speaking from a purely technical perspective, you can export all kinds of data from the PLM to the ERP. The real question is — what data should you send using an integration? As a rule of thumb, we advise you to only focus on exporting PLM data that is relevant and useful for the operations and manufacturing processes.
Pushing out information such as detailed product specifications, engineering bills of materials (eBOMs), and multiple iterations of product designs from the PLM to ERP is not required.
- Bill of materials
- Part data
- Product data
- Revision data
- Structure data
- List of attributes
- Status information
- Engineering documents and links
- Bill of processing (BOP)
- Engineering change information
You may choose to add more data, depending on your business requirements.
Tips on maintaining the boundary during PLM-ERP integration
- You do not have to send all your PLM data to the ERP. Focus on exporting the portion of PLM data required for the operations to the ERP via the PLM-ERP integration.
- Determine which system (PLM or ERP) will provide the master for each product, and it should always be the master system, whether it be data modification or data maintenance.
- Know which changes in product data you can make in the PLM and the ERP.
- Avoid conflicts and data duplications when integrating the PLM and ERP.
- Plan the foundation for how product data moves from the PLM to the ERP without friction.
- Consider the flow of data during the PLM-ERP integration, such as the frequency of changing information, the volume of data, and combining multiple ECRs into one ECO.
How does our PLM-ERP integration maintain data ownership?
We understand the significance of ensuring data quality and integrity during the integration process. Our solution maintains data ownership, so while you have a strong connection between the two systems, the lines are never entirely blurred.
Different BOM lines of a product will be transferred 'as is' from PLM to ERP, as the PLM system owns the BOM line of products. You can add 'local information' in the D365 ERP, which will only be available locally.
Our PLM integration framework recognizes any changes within product versions or BOM lines in the PLM system. It automatically updates it in the ERP without changing other product fields, thereby maintaining data ownership.
How can we help you with PLM-ERP integration?
If you’re interested in integrating your PLM system with Dynamics 365 ERP, you might want to explore the PLM-ERP integration solutions we offer embedded in Dynamics 365.
We offer out-of-the-box PLM integrations for Siemens Teamcenter and PTC Windchill. Additionally, we provide PLM integrations with 3DX Dassault and a PLM integration framework that you can easily configure for other PLM, PDM, or CAD systems.
You can explore more about our PLM-ERP integration solution by checking out our factsheet, which gives you a peek into:
- What the integration solution can do for your business
- Benefits of PLM-ERP integration
- Features of the integration solution