7 Supply Chain Disruptions Solved by PLM-ERP Integration for Manufacturers
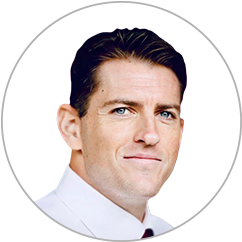
Table of contents
As a manufacturing business, you could be utilizing PLM and ERP systems to manage and control different processes related to the engineering, designing, and transactions, of your products. With both systems handling critical product data, not having them talk to each other puts you at risk of a supply chain disruption.
At STAEDEAN, we help global manufacturing enterprises integrate their PLM systems with Dynamics 365 ERP, and we have seen the supply chain disruptions faced by manufacturing companies.
In this article, we will share the biggest supply chain challenges faced by manufacturers and how a PLM-ERP integration can help overcome these challenges.
How will the supply chain disruption impact manufacturers in 2023 and beyond?
Despite being a trend we’d all like to leave behind, it appears that supply chain disruption is here to stay. The National Association of Manufacturers reported that more than 78% of manufacturers consider supply chain disruptions a primary business challenge.
According to the Manufacturing Leadership Council, 52% of manufacturers have experienced supply chain disruption, and 73% of manufacturing companies do not fully protect their current supply chains. The leading obstacle to a resilient supply chain was a lack of common data platforms and digital maturity.
A McKinsey report stated that companies with end-to-end visibility of their supply chain are twice as likely to avoid supply chain disruption.
However, the condition seems less than encouraging with rising inflation, labor shortages, and the pending recession. But if there’s one area you can begin eliminating issues related to your supply chain — it would be to streamline operations with well-connected data systems. A PLM-ERP integration is the first step manufacturers must take to achieve supply chain resilience.
What are the top supply chain challenges faced by manufacturers and how does PLM-ERP integration help?
Challenge 1: Prolonged time to market
The distance between your PLM and ERP is directly proportional to your product's time to market (TTM). A large gap between the systems increases the time it will take to bring a product from conception to market availability. A long time to market could get you behind your competition, especially regarding new product launches, and you may lose an exciting amount of potential market share.
How PLM-ERP integration helps: A PLM-ERP integration unifies all the significant processes related to your product, such as ideation, engineering, sourcing, production, inventory, and distribution. The ability to manage all your processes easily, and quicker communication from PLM to ERP, will increase your agility and enhance efficiency, reducing your time to market.
Challenge 2: Inconsistent visibility into the supply chain
Not having an end-to-end view of your supply chain due to siloed data and a scattered view makes it difficult for the engineering and manufacturing managers to realize any errors or make necessary improvements. Asynchronous PLM and ERP systems and information gaps often lead to supply chain vulnerabilities. You won’t identify potential hazards and incur costly damages.
How PLM-ERP integration helps: An integrated environment provides insights into the supply chain with increased visibility and clarity, thereby helping manufacturers and engineers work smarter and keep track of their on-site and off-site activities with ease.
Challenge 3: Underdeveloped planning of the future
One way for a manufacturing business to improve its operations and increase revenue is to have better plans and strategies for the future. Without a complete picture of the product lifecycle, you cannot identify potential hazards, vulnerabilities, errors, or weak areas in the supply chain.
How PLM-ERP integration helps: Fully transparent product lifecycles with integrated PLM and ERP systems provide teams with a clear view of product development from start to finish. With timely insight into the lifecycle status of your products and the entire supply chain, you can work smarter and prevent supply chain errors. You gain a big-picture perspective, and inefficient processes can be corrected, boosting your supply chain agility.
Challenge 4: Scattered and missing data
When your product data is running in silos across multiple systems, you have islands of data. Not having data synchronized and updated makes you unable to share recommendations or timely updates, resulting in missed opportunities. This also leads to missing information or loss of data, as certain data could be overlooked or forgotten in a haphazard process. Different teams deal with varying sets of data, and formats, leading to inconsistencies, and it becomes challenging to track changes in product design or manufacturing, ultimately hurting your supply chain.
How PLM-ERP integration helps: An integrated PLM and ERP offers one source of truth, with which departments can share data in near real-time. With a seamless and direct connection between your PLM and ERP, there are no more disruptions to transferring data, and no data is lost in the daily operations. All the data related to your products, such as versions, revisions, changes, or updates, are well documented and accounted for.
To learn about the 8 most important factors when choosing the right PLM integration solution
|
Challenge 5: Miscommunication and misalignment
Disconnected systems cause a natural information gap between the departments working in the PLM and ERP. Since the design and engineering teams are only operating in the PLM system and the manufacturing and logistics teams are only operating in the ERP system, there is no access to the product data overview, proper communication, or alignment on products. This gap increases with time, leading to supply chain disruptions.
How PLM-ERP integration helps: PLM-ERP integration combines both software systems to allow for the collaboration of users working with them. Teams communicate regularly and efficiently, leading to improved performance and higher growth. With all relevant data stored in a unified repository, teams can view, edit, and update product data cohesively and put lesser effort into non-cognitive tasks.
Challenge 6: Errors due to manual operations
Following a manual procedure to import product data and bills of materials (BOMs) could lead to errors at multiple levels. Manual processes are slow and increase the chances of human error, especially when dealing with product releases to multiple legal entities. You are at a higher risk of defective manufacturing, supply chain delays, and production halts.
How PLM-ERP integration helps: With a proper integration between the design and operational aspects of your product, you save on the effort, time, and money you would otherwise spend on inspections, corrections, and damage repair.
Challenge 7: Inability to maintain data security and integrity
Multiple stages of your product data existing in different systems and handled by various teams increase the chances of data duplication, repeated entries, and unnecessary clutter. This makes your company prone to a data breach or leak, as there's no mechanism to keep your data secure.
How PLM-ERP integration helps: After implementing a PLM-ERP integration, your data and files are streamlined, allowing teams to work in an organized manner. It maintains tamper-proof data records and makes data available to various business users as and when required. A single repository also means more secure data and a safeguard for sensitive information.
Are you ready to streamline your supply chain with PLM-ERP integration?
There are several benefits a PLM-ERP integration solution can offer your business. If you’re interested in integrating your PLM system with Dynamics 365 ERP, you might want to check out our PLM-ERP integration solution. As an intuitive, easy-to-use solution, it seamlessly brings together your engineering and manufacturing worlds.
We offer out-of-the-box PLM integrations for Siemens Teamcenter and PTC Windchill. Additionally, we provide PLM integrations with 3DX Dassault and a PLM integration framework that you can easily configure for other PLM, PDM, or CAD systems. You could explore our intuitive and easy-to-use PLM-ERP integration solution by diving into our factsheet.
This factsheet shares information on:
-
What the integration can do for your business
-
Benefits of PLM-ERP integration
-
Features of a standard integration