PLM-ERP Integration for Dynamics 365: How Data Moves from PLM to ERP
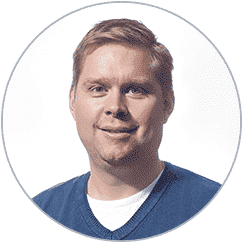
Table of contents
Integrating your PLM and ERP systems is a move many businesses make to ensure cohesive interdepartmental coordination and enhance process accuracy. While searching for a PLM-ERP integration solution, it is important to know a couple of things like what data you want to transfer and how the data transfer would take place, and how ERP integrates with PLM, so you are well-prepared before the implementation of the solution.
With a global experience spanning over 19 years in the manufacturing industry, we at STAEDEAN have often been asked by several customers: How does the data move from PLM to ERP with the integration solution?
In this article, we will share how the data transfer occurs from PLM to ERP, so you can know upfront about where your data lies and how it travels.
We will be discussing the following:
- What is our PLM-ERP integration?
- How does data move from PLM to ERP with our PLM-ERP integration solution?
- What kind of data do we integrate?
What do we offer in our PLM-ERP integration?
We integrate PLM systems with the ERP Dynamics 365 F&SCM, in combination with engineering change management (ECM) or Dynamics AX 2012 (which requires Product Engineering). The PLM integration solution is deeply embedded within Dynamics 365 and can import data to D365 by applying business logic and setting up certain templates.
We offer out-of-the-box PLM integrations for Siemens Teamcenter and PTC Windchill. Additionally, we provide PLM integrations for 3DX Dassault and a configurable PLM integration framework that can be easily adapted for any PLM, PDM, CAD, or MDM system.
How does data move from PLM to ERP with our PLM-ERP integration solution?
Our PLM-ERP integration supports data movement for enterprises having one, two, or multiple legal entities. To explain the data movement process from PLM/CAD to the manufacturing plant, let’s consider the scenario of a business having two legal entities:
1. Data movement from PLM or CAD to the engineering company with PLM integration
2. Data movement from the engineering company to the manufacturing plant with ECM
Here’s what happens in each of the two phases:
1. Data movement from PLM or CAD to the engineering company
The PLM or CAD system is the external environment in which the information related to product lifecycle and design is stored. The product-related data must be in a certain, acceptable format with which it can be released, for example, XML, Excel, web services, etc.
This data from the PLM or CAD system is first released to the engineering company which is in the Dynamics 365 environment.
The product data or product structure will then be picked up from the integration or connector, which will identify and state the type of the file format and is read in the PLM framework.
The PLM framework then carries out the following:
i) Maintains data ownership
ii) Automates data population (in combination with ECM)
iii) Ensures data quality by validation (in combination with ECM)
i) Maintaining data ownership
Data ownership refers to how data is created, accessed, and modified within the systems. For instance, different bill of materials (BOM) lines of a product will be transferred 'as is' from PLM to ERP, as the BOM line of products is owned by the PLM system. You can add 'local information' in the D365 ERP environment, which will be available locally and not globally.
The PLM framework recognizes any changes within product versions or BOM lines that occur in the PLM system. These changes will be automatically updated in the ERP system, without changing any other fields of the product, thereby maintaining data ownership.
Below you can see a graphical representation of data ownership with our PLM-ERP integration
In the image above, the product version has changed in the PLM/CAD system. Product A V 1.0 has changed to Product A V2.0, and only one BOM of the product has changed – C V2.0. The PLM integration only changes the delta information and version changes of the product will be reflected 'as is' in the D365 ERP, without changing other elements of the product data. You can see a change only in Product A V2.0 and BOM C V2.0, whereas BOM B V1.0 remains unchanged, thereby maintaining data ownership.
ii) Automating data population
The entire structure of the product data is enriched using ECM capabilities: readiness policy, release policy, and version controls.
- Use the readiness policy to set up readiness checks to populate/check the price, check the size specifications of the product, and so on
- Use the release policy to specify the template where the default values come from
- Use engineering change orders (ECO) to handle changes in the production and sales orders
With this, creating products within Dynamics 365 becomes much easier. For instance, creating one product in Dynamics 365 takes a minute on average, as a single product could have multiple fields or components to populate.
However, the PLM framework in combination with ECM will automatically populate the fields and enrich the data by setting up defaults in the template during the import. This means if u want to import new products with 100 component lines, defaults for all the 100 component lines will be automated, saving lots of time and effort.
iii) Ensuring data quality and validation
After the data is enriched, it reaches the staging journal, in which the product data is validated to ensure data quality. The necessary configurations and mapping are executed after which you can run the Integration. The integration supports multi-level structures with multiple journal lines, each having its own details, attributes, BOM lines, documents, and logs.
You then proceed by choosing the approvals and activate the BOM on release. After the information is validated, the system will state that all the information in the journal is ‘OK,’ and you can post the journal.
The D365 system will review all the items and auto default information from the ‘engineering product category details’ during the release. For instance, warehouse information, posting to finance, etc. will be done automatically.
After the PLM Journal is posted, the data is now a released product.
This product data from PLM/CAD can be released to one or multiple engineering companies, and therefore the data movement can work for a single or multi-company scenario.
2. Data movement from an engineering company to a manufacturing plant with ECM
The data has moved from the PLM/CAD to the engineering company and now this data is pushed to the manufacturing plant (single or multiple plants). It happens with the following steps:
i) Releasing products to the manufacturing company
From the newly released product, you can select the active product version and release the product structure you want by specifying the release details.
You can carry out:
- Single or multiple releases
- Part releases (without all BOMs) or full releases (the entire data structure)
During product data release, different data fields are auto populated using the same defaults from the ECM.
You then select the company to which the products must be released and click ‘process’ and the product will be released in the manufacturing company. All of this can be released to one manufacturer or multiple manufacturing plants, so it supports multi-releases.
ii) Creating new production orders
You can see what you received from the engineering end and explore the new products, after which you can 'accept the release'.
Set up readiness checks to populate any other data field by assigning it to the respective personnel. For example, cost-related information about the product.
After every quality check is passed, the product engineering version is activated, and you can begin working with the product.
You can create production orders by navigating: all production orders > new production order > create a new production order. Select the product (and version), and a production order will be created with the relevant BOM lines.
iii) Sending information from ERP to PLM/CAD
You can carry out certain configurations to the integration with which you can get ERP data back into the PLM/CAD system, for instance: price information or stock levels.
To support the above, we've added innovative functionality to our PLM-ERP integration solution: Product Logistic Insights, to manage product changes better.
You can also opt to send communication back to the PLM or CAD system letting the engineering team know that the products are received properly in Dynamics 365 (on the roadmap).
iv) Setting up engineering change requests
You can also set up an engineering change order which can be sent out to the engineering company, after adding the priority and severity (functionality on the roadmap). This change request will automatically be reflected in the engineering company under ‘engineering change requests,’ which can be approved by the concerned engineer. After the change order is executed and the new product information is sent back to the PLM system, the updated data can be picked up again.
Related reading: Key Features of STAEDEAN PLM-ERP Integration Solution for Dynamics 365 ERP |
What kind of data do we integrate?
Below you can see the list of data we integrate with the PLM and ERP systems
The integration can be done using XML and excel formats (web services on the roadmap). The type and volume of data that you can integrate could also depend on your specific business needs. More integration capabilities will be made available soon.
Is our PLM-ERP integration for Dynamics 365 the right solution for you?
Buying an integration solution like ours can streamline your manufacturing processes in a quick and effortless manner without any hassles of designing, coding, and maintenance.
If you want a solution with a quick implementation time that ensures data quality and ownership, our PLM-ERP integration might be just what you’re looking for.
You can see our PLM-ERP integration solution in action by book a demo with us.