How to Manage BOMs with PLM-ERP Integration for Dynamics 365
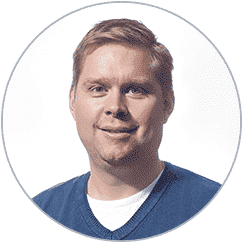
Table of contents
The significance of the bill of materials (BOMs) doesn’t have to be emphasized for anyone in the manufacturing industry. It is the basis of the entire supply chain and the reference document for everyone to ensure they are building the right product.
Inefficient BOM management results in incorrect manufacturing, delays in production, and impacts your entire business.
Having worked with numerous manufacturing companies from various industries, we at STAEDEAN have empowered businesses to streamline their manufacturing processes through a PLM-ERP integration solution for Dynamics 365.
In this article, we share the significance of BOMs and how you can handle them efficiently with a PLM-ERP integration solution.
What is the bill of materials?
Bill of materials often abbreviated as BOMs is a centralized information source containing an extensive list of items required to create and manufacture a product along with instructions to assemble and repair it.
The format of a BOM is usually hierarchal, with the finished product at the top and the individual components and raw materials displayed at the bottom levels.
What role does the BOM play in a manufacturing company?
Before any manufacturer begins to create a product, they would first need to know all the parts and components that would be used in creating the product and how to go about assembling it.
This process of creating a comprehensive list of parts, sub-parts, and sub-assemblies that will be used to build the finished product is how a BOM is created.
Often covering all the components required to make the final product, a BOM is referenced at various stages of a product’s lifecycle by different teams to ensure smooth production.
BOMs play a critical role in the manufacturing of any product. It helps you allocate resources and identify wasteful usage to develop more cost-effective products. It is responsible for ensuring all the departments work together and in sync.
Why must manufacturing companies manage BOMs efficiently?
Every single product today can be a combination of mechanical, electronics, and software. Customers nowadays demand high-quality and low-cost products and services. Also, with companies now moving into services in addition to selling products, the maintenance and management of BOMs has become more critical than ever.
As a manufacturing business, you’ll need to manage different aspects of the bill of materials during the design, engineering, manufacturing, and support stages.
From prototype to the final versions of products, there could be several updates in the BOM. If these updates are not communicated to everyone involved, it could lead to incorrect production, ultimately hitting your business’s reputation.
An inaccurate or incomplete BOM could pose the following challenges:
-
Makes procurement challenging as you are neither aware of the raw materials nor the quantities
-
Causes delays or halts in the production process as you could run out of stock
-
Increases risk of liability or product recalls due to inferior material planning and shortages
-
Results in longer project duration and higher holding costs due to poor planning
-
Creates inconsistencies among different departments – procurement, production, and sales
How can manufacturing companies manage BOMs efficiently with PLM-ERP integration?
PLM at the engineering end and ERP at the manufacturing end are commonly used to carry out business processes in the manufacturing unit. Both systems make use of BOMs and in order to track inventory and keep your workforce aware of any changes or updates in the BOM, you would need a solution that allows communication between your PLM and ERP systems.
A PLM-ERP integration solution can help you solve this. This integration establishes effective communication between several parties involved in the engineering, manufacturing, and production processes so that the information flows smoothly.
Such a solution allows the transfer of the BOM (along with several other vital information) from the PLM to the ERP system, making the job of the manufacturers easier. It provides the manufacturing team with access to a reliable and up-to-date BOM.
What is our PLM-ERP integration solution for Dynamics 365?
With our integration solution, you can integrate any PLM system with Dynamics 365 Finance & Supply Chain Management. It brings the engineering and manufacturing worlds closer.
Our PLM-ERP integration solution works with the Engineering change management (ECM) component of Dynamics 365. ECM is responsible for version and release management of BOMs and other product data in the Dynamics environment.
How can our PLM-ERP integration for Dynamics 365 manage BOMs?
With our integration solution, you can do the following with your BOM:
1. Ensure data quality of the BOM
Any data that comes from the PLM is first placed in a framework called the staging journal. In the staging journal an established data validation process occurs to validate the BOM data and maintain its quality.
The BOM is released only after these validations are done. The product cannot be used before the relevant routings and BOMs are created.
2. Manage multi-level and single-level BOMs
A multi-level BOM contains several subassemblies, each of which can also be a single-level BOM. On the other hand, a single-level BOM represents one level of an assembly and does not include any lower-level subassemblies.
With our solution, during integration, each product can have several BOM lines and therefore multi-level BOMs can be imported. The solution also easily supports single-level BOMs.
Within this BOM you can see details like the product, product specifications, BOM lines, main items with the sub-items, drawings, reference documents, and searchable attributes.
3. Quick overview of BOMs across teams
Using multiple software systems such as PLM and ERP makes it essential for the integration to enable a smooth flow of necessary information.
Different teams across the company can access the same BOM in a holistic way. This reduces communication errors, decreases rework, and streamlines workflow. The PLM-ERP integration allows for a structured view of the product BOM, and each team could view the information based on their roles.
4. Make key decisions around BOM data
When creating or updating BOM data from the staging journal, the integration solution helps you make decisions, such as:
- Which data is already there, and how to interpret the data
- How to create new product revisions and BOMs
- How to update or overwrite existing item revisions and BOMs
- How to automatically approve and update BOMs on PLM status change
- How to handle local data (for example, local BOMs) within a multi-company environment
How can ECM in Dynamics 365 help with BOM management?
1. Release BOMs based on requirements
You can choose to decide how much of the BOM data you want to release to different departments or companies you’re dealing with. With the ECM solution, you can:
- Do part releases, where you release only a certain part of the BOM
- Release the entire BOM
- Release multiple active BOMs for one product
- Decide which BOMs you want to push to the operational side, for instance, pushing a detailed BOM to the manufacturing plant
- Choose to release a basic BOM to the sales company as it would be more relevant
This can all be done by setting up the relevant routings for the BOM.
2. Manage changes and updates in the BOMs
The manufacturing plant can carry out local change orders like adding packaging materials to the existing BOMs. This can then be approved by the relevant owner, after which the BOM is updated.
This update (local change) to the BOMs can be done directly in Dynamics 365.
Additionally, if you make a change in the PLM, and get a second version of the product based on the change order, this change will be updated in Dynamics 365 as well.
What are the benefits of BOM management with our PLM-ERP integration?
Some benefits of our PLM-ERP integration for Dynamics 365:
-
Decreases errors due to reduced manual entry and process automation
-
Prevents data re-entry into the BOM multiple times
-
Provides quick access to BOM data with an automatic data transfer from the PLM to ERP
-
Saves time, effort, and resources
-
Streamlines processes and positively impacts your business
-
Guarantees that the BOM data is in sync in both the PLM and ERP
-
Offers a consistent overview of the BOMs across different teams
How does the BOM transfer from PLM to ERP occur with our integration for Dynamics 365?
The movement of the BOM from engineering to manufacturing occurs in the following way: The PLM (engineering) first imports the BOM to the engineering company which is set up as a legal entity in Dynamics. BOMs can be integrated with the following formats: file-based integrations such as XML and excel, or web services.
The BOM data is picked up by the integration solution. The BOM data from the PLM is picked using the PLM’s ERP connector, for example, T4EA used by Siemens Teamcenter PLM.
The BOMs are then brought over to the engineering company and automatically curated. For instance, if there’s a product with 100 components to it, all those 100 components will be automatically brought over to the engineering company.
You can make use of ECM capabilities which is the release mechanism to enrich the data. This means when you enter data or a BOM in Dynamics 365, the ECM component sets up lots of defaults in the template. This makes the data transfer process a lot easier, as opposed to spending 2 to 3 minutes per product with a manual process.
The integration solution makes use of the ECM capabilities to do the BOM transfer quicker. It automatically populates several components of each product, saving lots of time and effort.
The BOM is then put in the staging journal. The approval processes for the BOMs are done with the necessary validations or readiness checks. If everything is validated, the BOM is created in Dynamics 365 and the journal is posted with all the defaults.
The BOM is then pushed out to the manufacturing plant, and you can begin creating the products.
If there is any change required from the manufacturers at the manufacturing plant, a change request can be sent back to the engineering company.
Ready to effectively manage BOMs with PLM-ERP integration for Dynamics 365?
If you’re looking for standard PLM-ERP integration software embedded in Dynamics 365, you could explore the integration software we offer.
We provide out-of-the-box standard integrations that easily support output formats from two PLM systems: PTC Windchill and Siemens Teamcenter. We’ve also successfully executed integrations with 3DX Dassault.
Additionally, we offer integrations for any other PLM, PDM, or CAD systems, using a PLM framework that can be easily configured according to the data output format.
You could explore how our PLM-ERP integration in combination with Dynamics 365 ECM helps with BOM management and much more, by checking out our factsheet.
This factsheet shares information on:
-
What the integration solution can do for your business
-
Benefits of PLM-ERP integration
- Features of a standard integration solution