8 Common PLM-ERP Integration Challenges and How to Solve Them
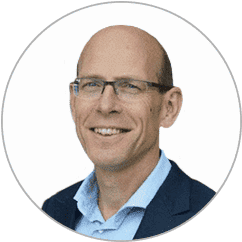
Table of contents
Implementing integration software to connect your PLM and ERP systems must be done right the first time to avoid additional costs to your manufacturing company. If the integration solution you opt for does not ensure data quality and cannot accommodate any future needs of your business, it would result in untimely higher maintenance costs.
If you’re considering integrating your PLM system with Dynamics 365 ERP, it would be helpful to know the challenges you could face during the implementation, so you are better prepared to proactively address them.
Having implemented standard out-of-the-box PLM-ERP integrations for global customers on the Microsoft Dynamics 365 ERP for over 20 years, STAEDEAN is familiar with challenges customers face while implementing the integration software and has helped them successfully overcome these challenges.
This article will discuss the 8 common challenges to expect while implementing PLM-ERP integration software and how you can avoid them.
What are the top implementation challenges while integrating PLM and ERP, and how can you avoid them?
1. Misaligned business expectations
We’ve put this challenge first as it impacts the entire implementation process. It’s important that every department within your manufacturing company is aligned with the PLM-ERP integration software deliverables, otherwise, it would lead to an organization-wide miscommunication.
Different teams would be unaware of what is expected of them or the impact of the integration software on their daily operations. Everyone would have a different take on what the integration could do for your business, leading to confusion about the overall process change.
The solution: Team members can offer inputs from their experience to the leadership on the exact needs regarding training, deliverables, and data transfer, so everyone is on the same page and the implementation can be done right.
2. Internal training is overlooked
Any new software calls for training for the end-users, and PLM-ERP integration software is no different.
The integration not only impacts two key departments — engineering and manufacturing but also the entire organization.
The engineering team must understand that data will now be automatically pushed from PLM to ERP, and they must ensure data quality, which otherwise leads to gross manufacturing errors, costing time, effort, and capital.
On the other hand, the logistics team must be aware of how data would appear in a fully integrated ERP environment.
Focusing on implementation without timely and correct training for the team members leads to knowledge gaps and lags for the end-users operating the PLM and ERP systems.
The solution: Have a thorough discussion with all the teams who would be impacted by the integration software. Document the areas of training required and make sure you communicate this to your implementation partner to ensure all training needs are covered.
3. Ineffective change management
After implementing the integration, there will be a change in roles and responsibilities among the engineering and manufacturing teams. The data owned in two different systems will now be transferred from PLM to ERP and ultimately utilized at the ERP end.
For instance, in a non-integrated environment, the bill of materials (BOMs) responsibility lies with the manufacturing team. But after the integration, the engineering team must ensure that the correct BOMs are being imported to the ERP, and therefore its responsibility lies with the engineering department.
If not communicated and understood properly, this shift in product data ownership would result in a lack of overall ownership by the internal teams. Although the integration would be successful, the end-users (your internal teams) would still be wondering what data is owned by which system.
The solution: Before deciding to carry out the implementation, communicate the purpose and benefits of this software change to the entire organization. You could also consider hiring a change manager to ensure that the transition is smooth for employees.
4. Lack of awareness on the impact of data change
The integration would change the data format of each manufacturing product. For instance, before integration, you would record an updated wire within an inverter battery as two different objects. After the integration, product versioning is streamlined, and you will record it as version 1 and version 2 of the same inverter battery.
This impacts all the departments using the data, such as the warehouse, purchase, and delivery teams.
If these teams are unaware of the changes in data formats and definitions, they won’t know how to read, translate, or even use the data to carry out manufacturing activities. This leads to gaps in the manufacturing process — handling, operating, or managing the product, ultimately impacting your entire supply chain and risks product recalls.
The solution: Don’t only consider the engineering and the manufacturing team while training. All the other departments dealing with the product data must be given the right training on where and how the data exists. This could be conducted in team-wise sessions or using a train-the-trainers model for larger businesses.
5. Overlooking external training for third-party partners
The manufacturing supply chain doesn’t always consist of a manufacturer and an end customer. Often, there are several third parties involved in the form of servicing partners, selling partners, distribution partners, vendors, and so on.
When not equipped with the right knowledge of how your product data has been updated, the servicing partner will be confused about which part to repair, or the selling partner won’t know which is the latest product version to sell.
The solution: After integrating your PLM and ERP systems, all external stakeholders involved in servicing, handling, and selling your manufactured products must be briefed on the data change. If needed, you could also train the third parties you’re involved with.
6. Limited knowledge of PLM data
The first step when beginning to integrate your PLM and ERP systems is to analyze the data in the PLM system to be transferred to your ERP.
This ‘data’ must be carefully identified, analyzed, and then selected for import. If there is a lack of understanding on the format and type of data that you want to transfer, it could be the starting point of a disorderly implementation process.
Additionally, if your PLM system does not have a standard output format (XML, Excel, etc.), then this must be created, which increases the overall implementation effort.
The solution: Take your time analyzing the PLM data which you want to transfer into the ERP. Get in touch with your manufacturing team to truly understand what kind of data they use from the PLM system to avoid the transfer of unnecessary PLM data.
Also, look for an implementation partner and software vendor with a track record of implementing PLM-ERP integrations to get the right guidance on the data type and data format.
7. Inefficiency in supporting new product data structures
When looking to integrate PLM and ERP, if you want your data to be structured in line with versions and releases, you must invest in software that supports version and release management.
However, if your ERP doesn’t support version and release control of the product data, you would have to clean up your database in line with the new product data structure to maintain versions and releases.
What is more, if you’re moving from one ERP system to another, extensive data cleanup is needed. You have to set up a different data structure for your products, depending on the extent to which the previous ERP could support versions and releases. This process requires time and effort.
The solution: Begin cleaning and organizing your database according to the data output format provided by your integration vendor before you begin implementing the integration software. This will allow you to be a step ahead of the implementation process, and data errors, if any, could be corrected before the integration begins.
For instance, a classic Microsoft Dynamics 365 ERP environment doesn’t support product data with versions and releases. You must activate the ‘Engineering Change Management' (ECM) module within the ERP to control product versions and releases.
8. Insufficient clarity on data sets
Before you begin the implementation process, you must have a thorough understanding of which data sets you want to transfer from the PLM to your ERP. When you are not clear on the data sets you want to be transferred, you could end up adding more PLM data to the data list during the implementation.
This results in an additional effort for the implementation partner, as they must accommodate changes and more time to carry out the integration, as the entire testing process must be repeated for the new data sets.
The solution: Minimize repeated changes or alterations to the integration and get clarity on the data sets by educating yourself on the PLM data and carrying out a thorough analysis of the data in the PLM system. This will reduce, if not, avoid any ad-hoc changes you make to your integration software and quickens the implementation time.
Be clear on whether you want to build or buy the integration, to accommodate any future innovation of your business.
How can you ensure your PLM-ERP integration is done right the first time?
As a manufacturing company, you must be mindful of all the challenges discussed above and stay ahead of them with a well-planned implementation process by incorporating the recommended solutions.
The next steps you can take are:
1. Look for a PLM-ERP integration that you can implement out-of-the-box.
2. Identify an implementation partner with proven expertise in integrating PLM, PDM, or CAD systems to ERP.
3. Carry out data analysis to identify what your data needs are and select a software vendor that matches those needs.
If you’re using Microsoft Dynamics 365 F&SCM, you could explore the standard out-of-the-box integration solutions we offer for PTC Windchill and Siemens Teamcenter. We also offer integrations that can be configured for any PLM, PDM, or CAD systems.