Benefits of Out-of-the-Box PLM Integration with Dynamics 365 ERP
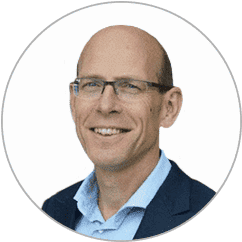
Table of contents
Last Updated: Dec 18, 2024
In manufacturing, silos aren’t just structures—they’re a significant organizational problem too. According to a Deloitte study, one in three manufacturers sees organizational silos as a top challenge. And it’s easy to see why. When systems like Product Lifecycle Management (PLM) and Enterprise Resource Planning (ERP) aren’t connected, teams work from different versions of the truth, making it harder to find the information they need to keep things running smoothly. If your organization relies on Microsoft Dynamics 365 ERP, integrating it with your PLM system can help bridge these gaps. This is where PLM integration with Dynamics 365 comes into play, breaking down silos by ensuring seamless data flow between the systems.
PLM provides the manufacturing team with critical details like engineering data, product drawings, and bills of materials (BOM) to build products correctly. On the other hand, your ERP, Microsoft Dynamics 365 Finance and Supply Chain Management (F&SCM) supports engineers with operational insights and logistics to design products efficiently. Disconnected PLM and ERP cause your teams to face unnecessary delays and frustration creating communication gaps.
The solution is simple: enable a single source of truth by connecting your PLM system with Dynamics 365 using an integration. And the quickest way to connect the two systems is an out-of-the-box integration.
What is an out-of-the-box PLM integration with Dynamics 365?
An out-of-the-box PLM integration with Dynamics 365 refers to a solution you can use immediately after purchase or implementation. It is ready to use without extensive customization, configuration, or additional development. Such integrations offer quick time to value and minimize user training time with pre-configured templates.
What are the benefits of out-of-the-box PLM integration with Dynamics 365?
1. Improves time to market
An out-of-the-box PLM integration with Dynamics 365 significantly improves the time-to-market for new products. With automated data transfer between systems, the handoff from design to production is faster and more reliable, eliminating manual processes that can delay production.
Teams can make decisions swiftly with real-time access to synchronized data from both systems, and the streamlined collaboration between engineering and operations accelerates the prototyping and production phases.
2. Saves costs
A ready-to-use PLM integration with Dynamics 365 can significantly reduce your business's costs. Since the integration is embedded in the ERP, it lowers the maintenance burden tied to managing multiple solutions.
Opting for a preconfigured PLM integration over custom development saves your budget, minimizes risks, and eliminates costly failures. Additionally, it removes the need for manual data entry, saving time, reducing errors, and preventing expensive rework.
3. Reduces IT dependency
Out-of-the-box PLM-ERP integrations are typically quick to deploy and require no programming to map against various input and output formats. As a manufacturing company, this allows you to begin importing data from PLM to ERP without any coding effort or IT dependency.
In most cases, the Independent Software Vendor (ISV) providing the integration solution handles all software maintenance. For example, we ensure the PLM integration is always updated, aligning with Microsoft’s release schedules to keep it running on the latest version.
4. Shortens implementation time
You can reduce the implementation time and have the solution running within a few weeks using an out-of-the-box PLM integration with Dynamics 365. Such integrations have preconfigured workflows and can adapt to your business needs with low configuration requirements.
With accelerated implementation templates designed for major PLM providers, you can deploy the solution rapidly and shorten the time to go live. This saves time by quickly addressing the standard requirements of any manufacturing business with minimal downtime.
5. Simplifies end-user training
You can simplify end-user training with an out-of-the-box integration, as it provides a unified and intuitive system that minimizes complexity while ensuring data quality. Users don’t need to learn a new system because the integration seamlessly operates within Microsoft Dynamics 365 F&SCM, maintaining the familiar interface.
This uninterrupted and sophisticated UI allows users to quickly adapt and perform their roles efficiently without the hassle of navigating multiple platforms or dealing with redundant workflows.
![]() |
Still deciding between building or buying a PLM integration for Microsoft D365? Check out our guide! |
How can you get an out-of-the-box PLM integration with Dynamics 365?
At STAEDEAN, we have been helping global manufacturing companies streamline their engineering and manufacturing communications for over two decades now, and we understand the significance of seamless integration between PLM and ERP systems.
Our PLM integration is fully embedded in Microsoft Dynamics 365 F&SCM and follows the same business logic, allowing a seamless user experience. With all your engineering and manufacturing data connected, you will have the correct data at the right time to complete production efficiently.
The PLM integration with Dynamics 365 utilizes specific capabilities of Engineering Change Management (ECM) in Microsoft D365 F&SCM to better handle product revisions, changes, and updates.
Which out-of-the-box PLM-ERP integrations are available at STAEDEAN?
We offer out-of-the-box PLM integrations for two of the most popular PLM systems: Siemens Teamcenter and PTC Windchill. This setup can easily be adjusted according to your needs. You can also tailor our no-code integrations embedded in Microsoft Dynamics 365 F&SCM, to suit any PLM, PDM, or CAD systems.
We follow the integration standards as set by Siemens Teamcenter and PTC Windchill. This means that we use the Teamcenter Gateway for Enterprise Applications (T4EA) for Siemens Teamcenter and the ERP connector for PTC Windchill.
With our out-of-the-box PLM-ERP integration, you can get instant answers to the following questions:
- How do you create or update product data from your staging tables
- What data do you already have, and how do you interpret it?
- How do you create new product revisions and BOMs?
- How do you update or overwrite existing item revisions and BOMs
- How do you automatically approve and update BOMs on the PLM change?
- How do you manage local data, such as local BOMs, in a multi-company environment?
- How do you communicate issues back to the PLM system effectively?
Ready to bridge the gap between engineering and manufacturing?
Discover more about our preconfigured PLM integration with Dynamics 365 by downloading the solution factsheet. Gain insights into:
- Connecting your engineering and manufacturing processes
- The benefits your business can gain with our solution
- Key features of our PLM-ERP integration solution