Should I Build or Buy PLM-ERP Integration for My Manufacturing Business?
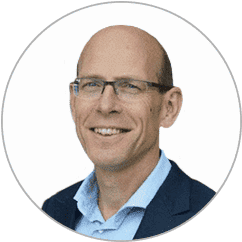
Table of contents
It’s a known fact that organizations must have their PLM and ERP systems connected to ensure there is no siloed data and that each version of the product is rightly communicated from the engineering team to the manufacturing team.
There are countless benefits of integrating your PLM and ERP systems, such as cost savings, structured information, and high data quality.
While you’ve realized the criticality of integrating the two systems, the pertinent question is, should you buy a standard solution from an independent software vendor (ISV) or build the integration solution on your own?
With decades of experience across different industries, we at STAEDEAN have been integrating PLM systems for companies using Dynamics 365 or AX as their ERP system.
In this article, we'll help you evaluate the effort involved in building versus buying PLM-ERP integration, by comparing them against various implementation factors.
Although we offer a standard PLM-ERP integration for Dynamics 365 Finance & Supply Chain Management, we aim to offer you an unbiased overview of what the journey would look like, so you can decide for yourself whether to buy or build the solution interface.
Factors to consider when deciding between building and buying a PLM-ERP integration solution
Various factors come into play when gauging the advantages and disadvantages of building or buying a PLM integration.
Building a fully functional PLM-ERP integration from scratch can be challenging with the development, planning, and time that goes into it. Next to the upfront development costs, there are long-term costs to maintain, upgrade, enhance the solution and dedicate manpower.
You must be wondering — “Why can’t I just write a simple import-export code to transport the data?” Well, you can, but it isn’t sufficient for successful integration. As there are high volumes of critical data transferred from the PLM system to ERP, and product data will be changed on both sides, you must consider several dimensions associated with data quality, which makes developing the solution a bit more complex.
On the other end, buying a standard integration may seem like an easy option to consider, as it reduces the hassle of designing, coding, maintenance, and associated costs. But it’s crucial you select a vendor with the right ERP experience (in this case, Microsoft), and a strong solution roadmap, as it locks you in a future of innovation.
We’ll be comparing the two options — developing your own solution or buying an ISV solution, against the following factors:
1. Identify requirements and resources
The first step in either building or buying an integration would be to identify the technical requirements of your solution and the skills or expertise needed to execute it. However, the effort of the identification process looks different for both.
Building: Engineers could be experts in the PLM system and manufacturers could be the sages of their ERP systems. But to build an integration solution, you’ll need qualified experts who have a fair knowledge of both the ERP and PLM systems. They are required to know the ERP solution in and out to identify exactly how the data will go in and be received in the ERP system in a logical format.
Buying: ISVs providing PLM-ERP integration solutions come with plenty of experience as this is their job. For instance, at STAEDEAN, we have decades of experience providing PLM-ERP integration solutions and we continuously update the solution by collaborating with our customers.
2. Solution plan and design
Based on your identified functional requirements, a functional design is created on what is expected from the specific code. This functional design is then turned into a technical design that specifies how the solution should be built, after which the solution development begins.
Building: Before identifying how to build, you need to identify the exact issues the integration solution will resolve. Prepare a comprehensive list that includes:
-
List of data elements – product data, version data, BOM data, engineering change information, etc.
-
Information to be integrated per data element
-
Data mapping
-
The receiving and processing process
-
The direction of data flow
-
Data format – based on web services or file transfer
-
Middleware to be put in between
-
Error handling
Buying: You primarily have to identify the exact technical requirements that will form the basis of your solution. The above-listed points are already planned in the standard solution. You’ll have to look into the different ISVs offering a standard solution and gauge them according to your functional requirements.
3. Integration solution development
Product data has two elements, engineering data in the PLM system and operational & logistical data hosted in the ERP, which exist on the same record. During integration, you need to ensure that changes in the product data on both sides — engineering and operations are in sync, without disturbing each other. The two systems, both of which own a certain part of the data, need to work together seamlessly.
Building: While developing a simple import-export code using data entities will do the data transfer, there is no means to govern the quality of the data being transferred and the extent to which it is received in the ERP system. Such a code could risk changing and resetting the data at both ends.
Since there is a high volume of critical data that travels from the PLM to the ERP system, there are multiple dimensions to take care of while doing the data transfer. This component of maintaining the data quality while ensuring no loss of data requires a lot more planning, effort, and development time while building the solution.
On average, building an integration solution close to the same functionalities and capabilities as our standard solution would require a development effort of at least one year.
Buying: A standard integration solution like ours prevents certain data changes by PLM or the ERP, retaining the highest form of data quality. At STAEDEAN, we offer two standard PLM integrations for Dynamics 365 ERP – PTC Windchill and Siemens Teamcenter, that take about one day to install, explain, and configure, which could vary depending on the training needs of the customer.
Our PLM-ERP integration solution is also easily adaptable to connect to other PLM, PDM, or CAD systems without any development. Integrations have been implemented with other PLM systems such as Dassault, Autodesk, Ansys, etc., by simply configuring the solution.
This can be realized within 3 to 5 days based on the output from the PLM system in a predefined format. However, this period may vary depending on the level of customization or change requests. The data output can be provided by the customer company or the PLM partner, to be able to carry out the integration successfully.
4. Solution testing and deployment
Building: A PLM integration solution simply cannot be deployed after development. You need to rollout a ‘pilot program’ to test the software and check for any bugs before scaling up the solution. This testing could be a rigorous and time-consuming process done by in-house testers or outsourcing testing, which again has additional costs.
Once all the parameters are tested successfully, the solution can be scaled and deployed.
Buying: The standard PLM integration solution can be deployed immediately after identifying the technical needs. Initially, workshops are held to understand and agree on the data configuration. Testing is done with the ISV to ensure the integration is successful, which is relatively quick and simple.
5. Implementation time
Building: If you consider the overall time taken to build a PLM-ERP integration solution which includes planning, hiring, and developing, it will average around one year for your software to go live. This results in a delay in connecting your business’s PLM and ERP, which can impact operations at the entire organization, as it is an additional year of having to deal with scattered data and improper workflows.
Buying: The implementation time takes about one to two weeks, which could vary based on the implementation effort and is excluding user acceptance testing (UAT) and training. You can enjoy streamlined operations immediately after the implementation.
6. Maintenance of the PLM-ERP integration solution
Building: You must check and test the software with every new release of the ERP system (in this case Microsoft) and accordingly change the logic to make it work. There is a possibility of your integration breaking if Microsoft has a new release, but you’ve missed out on testing your solution. This ‘testing’ to maintain your software is a continuous, costly, and cumbersome process.
Buying: In most cases, the ISV offering the integration solution will take care of the software maintenance requirements. For instance, we maintain the PLM integration solution in line with Microsoft’s release schedules and ensure the software is updated and running on its latest version.
7. Innovation and futureproofing of the integration software
Building: While building the solution, if you opt for a straightforward code, you may have to re-code the entire solution to add additional fields or attributes. It’s important to develop the solution by being mindful of any future needs you may have. This could translate to untimely higher costs, but it’s better to have your solution accommodative of future needs than having to build the code again.
Buying: An ISV can take care of any innovation or enhancement you’d want to bring into the software after implementation. For instance, our PLM-ERP integration solution is constantly enhanced with new features to meet the market trends.
It considers any future needs your business may have and you could easily:
-
Have a bidirectional information flow from ERP to PLM, by adding a connectivity solution component to the PLM integration.
-
Add additional fields or attributes with a technical configuration.
-
Integrate large data sets (BOMS with thousands of components) seamlessly.
-
Adopt any changes in the BOM and import the data.
Building or buying PLM-ERP integration — What’s right for your company?
Building versus buying PLM-ERP integration software is undoubtedly a big question for manufacturing companies.
One of the major challenges of building a PLM integration is that any ‘missing component’ of the solution would mean a loss of data, cost, and time. You’d have to start development all over again or lose time fixing the bugs, all while your data movement from the PLM to the ERP system doesn’t occur efficiently.
This makes it critical for a comprehensive planning phase in place while building the PLM-ERP integration, to reduce errors, especially when there are such huge volumes of data involved.
If you can build a PLM-ERP integration with all the right expertise and can afford to invest your time into developing the solution, perhaps with a slower implementation, then you have the option of building the PLM-ERP integration solution.
However, if you are clear on what you need and want a quick time to implementation, with no hassles around development, coding, and maintenance, then a standard PLM-ERP integration is the way to go.
To further dive into each approach and make an informed decision, our ‘Build versus Buy’ guide provides detailed insights.
In our guide you will discover:
- Pros and cons of building versus buying a PLM-ERP integration solution
- Key factors that influence your build versus buy decision
- A questionnaire that will help you choose the approach that suits you the most
Once you’ve read the guide, you will have a clearer understanding of which approach will help you meet your manufacturing goals and avoid costly mistakes down the line.