Why Life Sciences Can't Rely on One-Size-Fits-All ERP System? [Infographic]
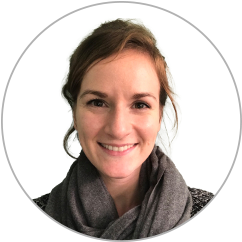
Table of contents
Life sciences are one of the most highly regulated industries, requiring strict adherence to quality, traceability, and security standards. Companies also need to manage complex inventory and supply chain operations while ensuring rigorous control over regulated data. While general-purpose ERPs provide a good foundation, they lack the specialized features needed by ERP for pharma industry to meet the sector’s demands.
Unique challenges of Life Sciences companies
-
1. Regulatory Compliance Gaps:
Adhering to compliance guidelines is essential in the life science industry due to the critical nature of its products. However, the compliance landscape is dynamic and complex, and even minor violations are likely to trigger warning letters or scrutiny from regulatory agencies. They can also lead to severe consequences like product recalls or penalties. Standard ERPs, built for general business needs are not designed for the sector's unique needs and often lack the depth to meet the regulations.
-
Electronic signatures: General-purpose ERPs as against ERP for pharma industry are likely to provide basic e-signature functionality; however, they are not stringent enough to comply with FDA 21 CFR Part 11 and EU Annex 11. For example, they may fail to provide robust audit logging of failed signatures, and may not be available for all GxP critical workflows.
-
Audit trails: Most standard ERP audit logs do not cover all crucial events. The inability to log electronic signature failures and modifications to critical records can weaken the audit trail. Additionally, they are not designed for human readability, making audits more cumbersome.
-
Supply chain qualification: Standard ERPs lack adequate controls to account for the qualification status of material vendors and manufacturers. As a result, implementing reduced testing following a risk-based approach becomes more difficult, making it more challenging to ensure compliance with required standards and increasing time and cost for quality departments.
2. Security Challenges
Standard ERPs lack granularity, flexibility, and control required to meet the security needs of pharmaceutical manufacturers, impacting their ability to remain compliant.
-
Granular role-based access: While standard ERPs typically enable the configuration of permissions based on role, they are not granular enough for the controls required by life sciences companies. This may make it difficult to impose stricter role-based permissions that prevent unauthorized users from making critical changes, such as, material disposition updates.
-
Field-level security: Standard ERP systems often lack the field-level security needed to protect sensitive data effectively. Without this capability, life science manufacturers cannot configure the system to address their specific needs, for example defining and safeguarding sensitive fields such as product lifecycle state.
-
Security audit trails: Unlike ERP for pharma industry, standard ERPs may not log security-related changes – leaving gaps in audit trails that can result in non-compliances.
3. Production Controls:
Standard ERPs often lack the controls needed to ensure that production workflows are consistently followed and controlled according to predefined quality standards. This gap in functionality can hinder critical quality and compliance checks, reduce efficiency, increase throughput time, and expose manufacturers to financial and compliance risks.
-
Quality orders: Generic ERPs often lack the flexibility to configure quality testing at all relevant production points. For example, while they may support quality tests for raw materials and finished products, they often do not provide adequate in-process quality testing, making it difficult to manage continuous production processes within the ERP.
4. Quality Management:
Every product in the life sciences industry must meet the highest quality standards, as any deviation can seriously affect patient safety and a company's reputation. ERPs for the pharma industry have robust quality control measures critical to meet the industry’s regulatory and operational demands.
-
Material disposition control: Standard ERPs offer limited flexibility in controlling material disposition, leading to inefficiencies in conditional releases and extended production lead times.
-
Test specifications & results management: Many ERP systems lack automatic versioning of analytical specifications. They fail to offer complete support for all types of testing, such as multi-level tests. General-purpose ERPs may not allow the copying of test results across sites or multi-level bills of materials (BOM), leading to manual data entry and inconsistencies.
-
Sample management: Advanced sampling plans – with sufficient flexibility for pharmaceutical needs – as well as full chain-of-custody tracking are often missing, increasing the risk of wastage or non-compliance.
5. Lot Traceability Limitations
End-to-end traceability is a critical pillar of pharmaceutical manufacturing, underpinning compliance with GMP regulations, enabling rapid recall execution, and ensuring product integrity throughout the supply chain. While standard ERPs provide batch-level traceability, this granularity is often insufficient for regulatory and operational needs. ERPs for the pharma industry enable full lot traceability with unit-level tracking, leveraging unique identification dimensions to support precise genealogy, deviation management, and recall readiness.
-
Unit-level identification: Standard ERPs typically do not track unique containers or drums, which is required not only for GMP, FDA, and serialization (DSCSA) requirements, but also for enhancing the management of production and manufacturing processes. For example, a sub-batch tracking dimension allows for handling variations, such as different concentrations, within the same batch.
-
Compliant labeling: Standard ERP batch tracking is insufficient for precise and compliant labeling. Purpose-built ERP generates regulatory-compliant labels for samples, materials, and shipping.
-
Integration with Lab Information Systems (LIMS): Standard ERPs provide only batch-level data entities, leaving no corresponding data entity to which LIMS test results can be mapped. Purpose-built ERPs provide a corresponding data entity, enabling LIMS integration for automated test results and strengthening traceability.
What happens when standard ERPs are used to run Life Sciences Operations?
1. Risk of Non-compliance: Companies failing to meet regulatory guidelines may face heavy penalties and legal proceedings.
Pharma companies lose $2.2 million to $39.2 million annually due to non-compliance.
2. Operational Inefficiencies: Inefficient operations lead to substantial financial setbacks, impact the ability to compete, and drain resources.
Inefficient supply chains push up the costs by 30%.
3. Missed Opportunities: A lack of proper R&D infrastructure can stifle innovation as well as delay the time-to-market of new products.
Approximately 80% of clinical trials do not meet the initial enrollment goals and timelines, and these delays result in a loss of $8 million in revenue per day for drug discovery companies.
4. Reputational Damage: Inconsistent products due to the absence of robust quality management cause patient mistrust and reputational setbacks.
43% of total GMP violations are Data Integrity Violations.
What are the features of an ideal Life Sciences ERP solution?
An ideal Life Sciences ERP solution needs to have comprehensive features that support the industry's production workflows and compliance needs. It should be:
1. Pre-configured solution: Standard ERPs can take years to implement, as life sciences companies must define their processes, configure the system, and validate the solution. A pre-configured solution, on the other hand, comes with workflows such as batch release engineered for the life sciences industry. This drastically reduces the implementation time, costs, and project failure risk. Additionally, ERP for the pharma industry also has:
-
Compliance Support: To help meet regulations like FDA 21 CFR Part 11 and EU GMP Annex 11
-
End-to-end Traceability: To trace and track every unit from warehouse to production, distribution, and recall
-
Integrated Quality Management: To control and assure the highest quality in every production batch seamlessly
-
Scalability and Flexibility: To grow and adapt to changing business needs in alignment with the company strategy
-
Industry-specific Modules: To support innovation efforts, enable efficient warehouse management, facilitate accurate weighing and dispensing, and more
-
2. Compliance-Ready Solution: ERP for pharma industry come with critical features, including built-in compliance capabilities, making them GAMP 5 Category 4 configurable systems that meet regulatory requirements. This eliminates the need for customizations that would push the solution into GAMP 5 Category 5, reducing the validation burden and simplifying compliance efforts.
3. Integrated LIMS and Weighing and Dispensing systems: The ideal solution should offer integrated options for LIMS and W&D systems or have industry-ready integration and data management tools, to reduce the tech stack complexity and risk of manual errors stemming from duplicate data entry. Data management tools should centralize the data and safeguard sensitive information.