How can Pharma Manufacturing Software Save up to $50B Annually?
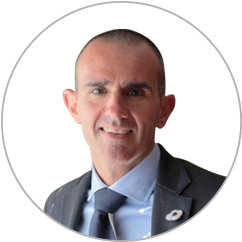
Table of contents
The pharmaceutical manufacturing industry is constantly under strain to innovate, meet stringent regulatory demands, overcome global competition, and deliver high-quality products in time to stay relevant in the market. Yet, operational inefficiencies continue to drain resources, with the industry losing an estimated $50 billion annually.
Operational delays, production errors, and supply chain disruptions not only increase costs but also threaten product quality and compliance. To meet market demands, a purpose-built pharma manufacturing software solution is needed, one specially designed to optimize efficiency by streamlining operations, reducing waste, and supporting regulatory compliance.
But why is it so difficult for Pharma Manufacturing companies to achieve operational efficiency? And why can only purpose-built ERPs help optimize their efficiency? Get answers to all these questions in our blog.
Why is Operational Efficiency Important for Pharma Manufacturing?
Operational efficiency can be defined as the capability to generate maximum output using minimum resources, time, and costs. When operations run without obstacles, production stays on schedule, costs are controlled, and products reach the market faster, strengthening your brand reputation and giving you a competitive edge.
Conversely, inefficiencies lead to wasted materials, underutilized resources, and costly delays, cutting profits and hampering growth. For example, inefficient operations lead to 30% higher total supply chain costs.
What are the Challenges in Achieving Operational Efficiency in Pharma Manufacturing?
Pharmaceutical manufacturing operations are highly complex and involve many stages, such as formulation development, active pharmaceutical ingredient (API) manufacturing, dosage form production, quality assurance, packaging, labeling, approvals, and batch release. Due to ever-changing regulatory demands, manufacturers must also undertake post-marketing surveillance.
The pharmaceutical industry is one of the fastest growing sectors, with an anticipated annual growth rate of 4.76% (CAGR 2025-29), resulting in a market volume of US $1,454 Billion by 2029. However, the increase in revenue and production volume brings challenges of its own.
Given the numerous stages and stringent regulatory demands, operational efficiency is difficult to achieve. Manufacturers face several obstacles that hamper productivity and compliance and raise costs. Let us look at some challenges derailing operational efficiency in pharmaceutical manufacturing.
1. Supply Chain and Inventory Bottlenecks: Pharma manufacturing supply chains are inherently complex and must adhere to strict standards and accurate operational controls. It comprises multiple interdependent stages, such as raw material procurement, inventory storage, production, and distribution that require precise coordination. Each stage has specialized needs and specifications. These complexities contribute to several operational inefficiencies, including
-
Inadequate inventory management: Pharmaceutical products and raw materials often have storage specifications, such as temperature, humidity, light, etc. Product integrity is compromised without proper supply chain management and inadequate monitoring, rendering goods unusable and causing huge losses. The pharmaceutical supply chain spans multiple geographies and timelines, challenging real-time visibility. A lack of transparency can lead to inventory stockouts, delays, and inefficiencies. Additionally, managing product recalls becomes more difficult without real-time tracking, increasing risks for manufacturers and consumers.
-
Regulatory non-compliance: Pharma manufacturers must ensure that all suppliers adhere to stringent regulations. Without qualified suppliers, manufacturers run into compliance risks and face penalties.
-
Unforeseeable disruptions Dynamic factors like geopolitical unrest, shifting economic conditions, and evolving regulations often cause sudden disruptions. Without proper planning, these challenges can lead to understocking or long lead times, further delaying production.
2. Disconnected Systems: Seamless pharma manufacturing requires collaboration between cross-functional departments like quality, supply chain, inventory, and production planning. However, when systems operate in silos, data becomes fragmented and creates inefficiencies in the operations as follows
-
Communication gaps: Missing or outdated data disrupts communication, creating process gaps that result in duplicate work or rework.
-
Strategy failure: Due to a lack of real-time data sharing, coordination gets impacted, and product/ organizational strategies fall through.
-
Higher operational costs: Without cohesive collaboration, inefficiencies in production, procurement, logistics, and process implementation crop up and lead to cost overheads.
3. Manual Errors & Rework: Pharma manufacturing companies often steer clear of technology and rely primarily on manual work and paper-based approvals. This dependence on manual work is mainly due to the fear of non-compliance; however, it introduces risks in operations and inefficiencies such as:
-
Financial losses: Manual processes lead to data entry or reading errors, causing incorrect formulation or labeling mistakes, leading to losses and non-compliance penalties.
-
Rework: Inconsistent and fragmented data giving way to duplicate work or rework, which in turn causes production delays and raises costs.
-
Production delays: Dependency on manual processes creates bottlenecks in the manufacturing processes due to slower response rates.
4. Inefficient Allocation of Materials & Resources: Real-time visibility into inventory, equipment, and resource availability is crucial to optimizing material and resource utilization. However, disconnected systems and data silos often create operational inefficiencies such as:
-
Resource wastage: Due to a lack of collaboration, manual processes, and outdated data, materials are allocated to the wrong processes, resulting in material wastage or shortage.
-
Underutilized or overburdened equipment: Due to incorrect planning, manufacturing equipment may become underutilized, leading to cost overheads, or overburdened, leading to maintenance issues or equipment breakdown.
-
Schedule conflicts: Misallocating material and resources may lead to conflicts affecting the production timelines.
5. Fragmented Data and Planning: Pharma manufacturers must manage a large volume of data in formulations, regulatory documents, or audit trails. When this data is stored across disconnected systems and managed manually, it leads to the following production inefficiencies:
-
Inefficient planning: Poor visibility across the operations and data silos lead to inadequate planning and inaccurate forecasting.
-
Compliance risk: Inaccurate and fragmented data can result in audit failures, compliance penalties, and reputational damage.
Know 7 main reasons why standard ERPs fail to meet Life Sciences Requirements! |
How Does Purpose-built ERP Software Enhance Operational Efficiency in Pharma Manufacturing?
Standard ERP software is not equipped to navigate the challenges of pharma manufacturing operations, such as traceability, regulatory compliance, formula management, and quality control. It does not have features that support complex supply chains, digital approvals, access control, weighing and dispensing, and laboratory information management systems, which are required for day-to-day pharma manufacturing operations.
Tailor-made pharma manufacturing software addresses industry challenges by offering specialized features to streamline supply chains, optimize resources, support regulatory compliance, and boost operational efficiency as follows:
-
1. Data management and Traceability: Pharma manufacturing ERP software centralizes the data to ensure integrity and eliminate data silos, thus mitigating the risk of wrong formulation or production delays. It also provides real-time data visibility across cross-functional teams, facilitating efficient planning, forecasting, strategic decisions, and operational efficiency. Accurate real-time data assists in maintaining audit trail and traceability and supports your efforts in complying with FDA 21 CFR Part 11, EU GMP Annex 11, and other local and global regulatory guidelines.
-
2. Automated Workflows: Pharma manufacturing ERP software helps boost operational efficiency by reducing the dependency on manual processes, which are time-consuming and prone to errors. It also automates manufacturing processes and quality checks to enhance quality control. An automated documentation system helps strengthen the audit trail to be inspection-ready. Digital approvals through e-signature are reliable, enhance data security, and save time compared to paper-based approvals.
-
3. Integrated Systems: Seamless communication across cross-functional departments enables the teams to work in symbiosis. With a single source of truth, it is easier and quicker to access updated data and deliver high-quality products in less time. Real-time end-to-end visibility across the different departments strengthens the ability to track and trace raw materials and end products. Streamlined traceability takes the burden off the resources and optimizes their efficiency.
-
4. Efficient Resource Management: Pharma Manufacturing ERP software provides real-time visibility of resource status. This enables the manufacturers to allocate resources to required processes and optimize their utilization. Optimized utilization directly impacts the production timelines and the bottom line.
-
5. Supply Chain Optimization: Pharma manufacturing ERP software helps maintain an approved vendor list with vendor qualification status, an approved manufacturer list, and an approved customer list to automate manual verification. This assists manufacturers in collaborating with compliant stakeholders and safeguarding themselves against non-compliance. Real-time visibility eliminates the risk of overstocking, understocking, or extended lead time.
-
It has advanced features to monitor specialized storage conditions according to specifications. ERP solutions designed for pharma manufacturing also automate the dispensing of raw materials after checking the product, order, batch, and container information before dispensing (item, batch and sub-batch number, quality status, and expiry date)
How Does Pharma Manufacturing Software Save up to $50 Billion?
Pharma manufacturing ERP software optimizes operations, resource allocation, and data management and supports compliance, contributing to significant cost savings. Automating approvals and workflows, centralizing data, and minimizing manual errors can boost operational efficiency by up to 96.6%. All these changes result in faster and cost-effective production cycles and meeting market demands on time. Additionally, real-time data insights and accurate forecasting help pharma manufacturers prevent costly business disruptions. Strong compliance support to the operations avoids the risk of costly regulatory penalties, too.
Why STAEDEAN Pharmaceutical Manufacturing Software?
Pharma manufacturing ERP software requirements are unique, and a solution that can navigate the complexities and boost operational efficiency is needed. STAEDEAN Pharmaceutical ERP is an out-of-the-box, all-in-one solution designed to meet industry challenges.
Our solution streamlines quality control, supply chain management, inventory tracking, and data governance. By standardizing workflows, optimizing resource allocation, and automating documentation and approvals, it significantly boosts production efficiency and reduces manual errors and delays.
It also supports compliance efforts by strengthening traceability, implementing e-signature workflows, and enabling a meticulous audit trail.
STAEDEAN Pharmaceutical ERP solution, embedded in Microsoft Dynamics 365 Finance and Supply Chain Management (F&SCM), not only manages operations but also maximizes efficiency, agility, and growth.