5 Costly PLM Integration Challenges in Dynamics 365 ERP (And How to Avoid Them)
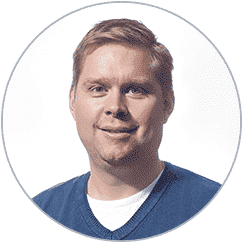
Table of contents
Integrating PLM and Microsoft Dynamics 365 F&SCM? Discover the major challenges of and their practical solutions.
Manufacturing works best when teams collaborate effectively. PLM and Microsoft Dynamics 365 Finance and Supply Chain Management (F&SCM) each handle different parts of the manufacturing process, but the real value comes when they work together. And that’s where a PLM ERP integration solution comes into the picture: it gets your systems talking so your operations run smoothly.
However, a market study suggests that 89% of the companies struggle with data and system integration. And, a McKinsey research states, ‘On average, large IT projects run 45% over budget and 7% over time, while delivering 56% less value than predicted. Software projects run the highest risk of cost and schedule overruns.’
These statistics highlight the need to pause, understand and analyze the PLM integration challenges in Dynamics 365 ERP.
Our blog looks at top 5 challenges and explains their impact on the business. Most importantly, the blog provides actionable strategies that help you overcome these challenges and ensure a smoother PLM-ERP integration.
Ready to integrate PLM and Dynamics 365 ERP? We can help you go live in 3 weeks! Talk to us now.
The Critical Importance of PLM Integration with Dynamics 365 ERP
In an IDC survey, 81% of executives admitted that poor integration is one of the biggest reasons their internal systems cause problems.
Both PLM (Product Lifecycle Management) and Dynamics 365 ERP hold essential data. Engineers rely on PLM for product design; manufacturing teams need ERP to procure, produce, and deliver those products.
Each system is critical; however, disconnected PLM and ERP give birth to complex issues that ultimately slow the manufacturing process. Without correct PLM Dynamics 365 ERP Integration, manufacturers run into:
- Cumbersome manual data transfers, increasing the risk of human errors
- Outdated, duplicate data and unclear ownership, causing inconsistent product records
- Misaligned Bill of Materials (BOMs) between engineering and manufacturing
- Operational delays due to limited visibility in engineering changes
- Inefficient change management process, slowing responsiveness
- Communication gaps between engineering and operations
Impact: Incorrect BOMs can cause a domino effect: incorrect procurement, quality issues, production delays, wasted resources, and ultimately, unhappy customers and financial losses. |
A well-executed PLM ERP integration eliminates data silos, enables real-time collaboration, and creates a single source of truth across the organization. It improves operational efficiency, product quality, and time to market and fosters innovation. Conversely, a poorly executed PLM ERP hurts your throughput and drives up costs.
With that in mind, let’s explore the five most common and costly PLM integration challenges in Dynamics 365 ERP and proven strategies for avoiding them.
1. How to Fix Data Synchronization and Consistency Challenges in PLM and Dynamics 365 Integration
PLM and Dynamics 365 ERP systems have different data formats and versioning methods for e.g., on the PLM or engineering side, design undergoes constant changes and has multiple versions.
On the other hand, the manufacturing side, or ERP, has production data and is not updated frequently. Inconsistent data in PLM and ERP, like mismatched BOMs, duplicate records, or incorrect versions, can impact procurement and production.
These data synchronization challenges undermine the reliability and integrity of data, reducing operational efficiency and product quality.
Why This Challenge Costs You
- Quality control issues: PLM ERP data consistency challenges can risk product quality. This can result in customer complaints, product recalls, and reputational damage.
- Delayed time-to-market: Outdated product versions in ERP lead to wrongful or delayed procurement, which ultimately delays deliveries. Multiple delayed instances affect product launches and innovation, negatively influencing competitiveness and growth.
- Increased operational costs: Poor quality control, production delays, procurement errors, and production disruptions all contribute to increased costs. A cumulative effect drains company resources and reduces profit margins.
How to Overcome This Challenge
To ensure a reliable PLM Dynamics 365 ERP Integration, it is essential to analyze each system's data structures and the fields that need to be shared. Standardizing data formats before integration help create consistent data. The existing database should be cleaned of redundancies and inconsistencies.
For example, PLM data integration solutions need data to be aligned for versions and releases. A standard Microsoft Dynamics 365 ERP does not support product data versioning by default; product versions and releases are available only after the ‘Engineering Change Management' (ECM) is activated.
The integration solution should ensure real-time bidirectional data sharing and establish a single source of truth. To ensure data integrity, it is also necessary to establish ownership rules. For example, the engineering side owns the product specifications, whereas Dynamics 365 ERP owns pricing and inventory.
Pro Tip: A staging journal can act as a validation layer when data from PLM is transferred to Dynamics 365 ERP for better data governance. |
2. How to Tackle Manufacturing Workflow Disruption Challenges in PLM-Dynamics 365 ERP Integration
PLM workflows are typically iterative and focused on design evolution, such as design reviews, engineering change requests, and approvals. They focus on design, innovation, and compliance. In contrast, ERP workflows are linear and focused on manufacturing needs, such as inventory procurement and production scheduling. They focus on efficiency, production deadlines, and inventory control.
Why This Challenge Costs You
- BOM inconsistencies: Due to different workflows, the BOM is updated more frequently in PLM than ERPs. Without process integration, the manufacturing team may refer to outdated BOMs for their tasks, resulting in incorrect procurement.
- Production delays and errors: Process misalignment, insufficient communication, or misunderstandings between cross-functional teams result in duplicated efforts, rework, and inconsistent production, causing delayed deliveries and costly errors that produce incorrect products.
- Reduced innovation and customer satisfaction: Ineffective collaboration between cross-functional teams restricts the sharing of critical insights, limiting innovation and delaying product deliveries. Lack of PLM ERP production alignment directly affects customer experiences and potentially harms the company’s reputation and retention
How to Overcome This Challenge
Stakeholder collaboration is challenging yet critical. Facilitating transparent communication and clearly defining roles for the teams involved is essential.
Standardizing workflows and training the stakeholders on the integrated workflows ensures everyone understands their roles and responsibilities and their impact on others.
Monitoring and feedback post-integration are also essential to maintaining morale and optimizing operational efficiency.
Pro Tip: The training should not be limited only to the manufacturing and engineering teams; any other department dealing with product data should be trained in how the data is stored. |
3. How to Overcome Technical and Architectural Challenges in PLM-Dynamics 365 ERP Integration
-
Today’s products are no longer just mechanical; they often combine electronics, mechanics, and software in one design. Additionally, customers often have customization requirements, further complicating the process. The global supply chain and its disruptions bring more variables into the equation. Therefore, the complexity of integrating PLM and Dynamics 365 ERP extends beyond mapping data to:
1. Middleware complexity: Many integration solutions rely on middleware, a software layer connecting two systems. Such solutions require additional infrastructure and resources. Initial setup and licensing are costly as well as time-consuming. Ongoing updates and software maintenance become an extra responsibility for the business owner.
2. Real-time integration vs batch integration: It is important to determine synchronization intervals that do not impact the performance.
3. BOM structure differences: Engineering BOMs are aligned according to design logic and technical specifications, whereas manufacturing BOMs are aligned according to production processes and resource allocation. Since these two structures serve different purposes, aligning them during integration isn’t straightforward; it often requires advanced logic to make them work together smoothly.
4. Version and change management: Aligning product versions on PLM and Dynamics 365 ERP to make sure that any design changes made by engineering are correctly updated in the manufacturing system.
Reading Material: Learn how SMART Technologies improved their supply chain management with STAEDEAN’s PLM ERP Integration Solution. |
Why This Challenge Costs You
- Operational disruptions: External platform or middleware failures can interrupt critical operations, causing unexpected downtime and production delays.
- Quality issues: Poorly aligned BOMs and version mismatches can lead to production errors. Defective products often get rejected, and rework or reproduction drives up costs.
- Slow decision-making process: Delays or errors in data synchronization slow down decision-making and reduce the organization’s ability to respond to market demands.
How to Overcome This Challenge
Organizations should build a comprehensive strategy to overcome the technical and architectural challenges, starting with data structure, BOM format, and PLM and Dynamics 365 ERP workflow analysis.
Middleware disruptions can be overcome by choosing a PLM integration architecture built into the Microsoft Dynamics 365 ERP environment. Such solutions can be implemented rapidly and extend the user-friendly Microsoft experience. Additionally, maintenance and updates get managed at the same cadence as Microsoft.
Pro Tip: STAEDEAN’s PLM Integration Solution is embedded in Microsoft Dynamics 365 ERP platform and follows the monthly upgrade policy of Microsoft, ensuring your solution always runs on the latest version. |
If you are looking at building the integration solution, read our insightful Build vs. Buy guide, which can help you make an informed decision.
4. How to Drive User Adoption and Manage Change in PLM-Dynamics 365 ERP Integration
Before the integration, the two standalone systems, PLM and Dynamics 365 ERP, had different workflows, business processes, and user roles. When PLM and Microsoft Dynamics 365 ERP are integrated, it brings a technical and operational shift in the organization. It changes the way the cross-functional teams collaborate and manage data between them. User adoption, especially if the change is perceived as complex or disruptive to established routines, is low.
Why This Challenge Costs You
- Lack of ownership: If the changes in ownership are not appropriately communicated, a gap is created, directly impacting data integrity.
- Employee dissatisfaction and frustration: Confusion with the new system and inability to discharge their responsibilities can affect morale.
- Low ROI: Inadequate PLM change management strategies may cause poor adoption, which will defeat the purpose of PLM Dynamics 365 ERP integration.
How to Overcome This Challenge
Change management should be handled in a structured and transparent way. Identify the stakeholders from both sides and engage with them to understand their concerns and gather input.
It is crucial to articulate the integration objectives, expected changes, and benefits. Updates regarding the same should be communicated promptly along with transparent timelines.
Adequate training and support should be planned and executed for the users. Maintaining user manuals and tutorials after the initial training also helps.
Pro Tip: Hiring a consultant adept at implementing integration adoption solutions can help ensure a smooth transition and maximize the benefits. |
5. How to Handle Maintenance and Governance Challenges in PLM-Dynamics 365 ERP Integration
Maintenance and governance issues challenge the Dynamics 365 ERP integration success because they directly affect the data quality, consistency, accuracy, and usability.
Poor data governance due to unclear data ownership, manual data entry, and inconsistent data creates an environment of errors and non-compliance. Inadequate version control and change management lead to engineering and manufacturing teams referring to different versions of BOMs.
Maintenance issues also become complex when data volumes grow, and systems evolve. Frequent PLM and Dynamics 365 ERP updates can create compatibility issues and break established workflows. Failure to resolve promptly can disrupt operations and impact production.
Why This Challenge Costs You
- Compliance risk: Poor data governance increases potential data security risks and compliance failures, resulting in penalties and reputational damage.
- System downtime: Inadequate maintenance practices lead to system downtime, which impacts deliveries and the company’s ability to capture market demands.
How to Overcome This Challenge
PLM integration strategies should define data governance rules by defining clear roles, responsibilities, and ownership to ensure data accuracy, consistency, and accountability. When PLM integration is implemented, a validation layer should confirm the data accuracy before it is put into action.
The success of PLM and Dynamics 365 ERP integration depends on how organizations carefully manage system upgrades or updates. Maintenance requires rigorous planning, testing, and coordination to prevent integration disruptions.
Pro Tip: When you purchase a PLM-Dynamics 365 ERP integration from an Independent Software Vendor (ISV), the vendor handles upgrades and maintenance, freeing your team to focus on strategic priorities. |
Conclusion
PLM integration with Dynamics 365 ERP can strengthen the manufacturing operations only when challenges are tackled with a robust strategy.
The data synchronization issues lead to production errors, manufacturing process integration issues can produce inconsistent BOMs, and technical complexity increases downtime.
Without user adoption, the ROI of integration cannot be realized, and finally, without a strong governance model and ongoing maintenance, the system updates can become a source of disruption.
You can address the PLM Integration challenges in Dynamics 365 ERP with strategic planning, stakeholder collaboration, and a strong ISV partner.
STAEDEAN’s PLM Dynamics 365 ERP integration is a no-code, intuitive solution embedded in Microsoft Dynamics 365 ERP. Bidirectional data sharing is facilitated in real time, improving collaboration between the engineering and manufacturing teams.
Our easy-to-use solution offers preconfigured templates for PTC Windchill and Siemens Teamcenter. It also supports rapid implementation with a wide range of PLM, PDM, and CAD systems, including Keytech, Dassault Systems, Autodesk, Solidworks, Revit, Revalize, and more.