Life Sciences Manufacturing: A Digital Maturity Roadmap
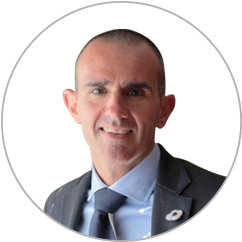
Table of contents
Learn how to move from cumbersome, paper-based operations to optimized, AI-based processes that are fully self-aware and continuously adaptive.
Life sciences manufacturing is rapidly evolving. Fierce competition to bring safe and effective medicines and medical devices to market—including novel cell and gene therapies—is driving the need for a convergence of speed, quality, value, agility, and sustainability across the value chain.
To meet these demands, pharmaceutical companies, biotech firms, medical device developers—and their manufacturing partners like CDMOs—must embrace modern production techniques and digital technologies that automate workflows and facilitate data analytics. Gains in efficiency are essential for taking advantage of new opportunities.
While some Life Sciences companies have been keeping up with the pace of change, many are still mired in paper-based processes and legacy systems that can’t handle the growing volume and velocity of valuable data. For these companies, a paradigm shift in manufacturing efficiency and optimization is required, just to stay competitive. Manual workflows, data silos, disparate systems, and unharmonized data all put drug and device developers at a greater risk of errors, delays, and a lack of regulatory compliance.
A Roadmap for Digital Plant Maturity
In October 2023, BioPhorum published an update to its ground-breaking Digital Plant Maturity Model (DPMM), which describes how Life Sciences manufacturing facilities can move from cumbersome, paper-based operations (Level 1) to optimized, artificial intelligence-based processes that are fully self-aware and continuously adaptive (Level 5).
While Level 5 is intentionally aspirational, today’s Life Sciences organizations are quite capable of—and should be—functioning at Level 3 or Level 4 of the model, using digital tools to support advanced manufacturing techniques, drive decisions, and prevent bottlenecks due to shortages of raw materials, component parts, and product inventory.
BioPhorum’s Digital Plant Maturity Model outlines a roadmap towards manufacturing optimization. Progress since 2017 has enabled leading drug and device manufacturers to target Levels 3 and 4, with laggards still stuck at Levels 1 and 2.
Companies currently operating at Level 3 or Level 4 of the DPMM enjoy more opportunities today. Digitalization offers key advantages that impact product quality, safety, and availability, including:
- The elimination of error-prone, manual interventions
- Reduced risk of batch failures and product contamination
- Access to insights that anticipate shortages and deviations
- Support for regulatory compliance
Reason to Become More Mature
BioPhorum’s DPMM is designed for two broad audiences. Shop floor operations professionals, manufacturing IT practitioners, and software suppliers, for example, can use the model to explain the benefits of investing in digital platforms to plant managers and directors, and highlight the requirements for moving towards a more digitally mature plan. Senior executives and business leaders can also use the model to make strategic decisions about which of their various plants would benefit most from a digital upgrade.
At STAEDEAN, we’ve been helping Life Sciences organizations embrace digital transformation since 2008. In the early days, we were moving companies from the pre-digital Level 1 to the digital islands described by Level 2. While that still happens to some extent today, most of our current customers are on a path to facilities that are fully connected (Level 3) and predictive (Level 4).
Many Life Sciences organizations are using outdated ERP systems.
Talk to STAEDEAN about digitalizing your company today for
greater efficiency and cost savings.
Most of the Life Sciences CEOs, CIOs, CFOs, and other executives we talk to realize the importance of modernization and aspire to become more integrated as quickly as possible. They all know that being complacent at Level 1 or Level 2 makes it harder to compete and pushes their compliance risk to unacceptable levels.
The move in digital plant maturity from Level 2 to Level 3 is all about eliminating points of failure and risks, due in large part to siloed information and a complex network of disparate solutions that don’t communicate very well.
Many plants at Level 2 have organizational boundaries between information technology (IT) and operational technology (OT). Moving to higher maturity levels integrates shop floor control systems (usually part of OT) and site-wide operational systems (typically controlled by IT).
AI is a huge driver of advancing digital plant maturity, with many companies eager to leverage the AI-based tools available today, such as Microsoft Dynamics 365 Copilot, while future-proofing their businesses for the advancements of tomorrow. We’re seeing a great deal of urgency about getting to Level 4 as quickly as possible. According to BioPhorum, this level of the DPMM “represents the highest level of automation and integration achievable with current technology”.
How Mature Is Your Plant Today?
BioPhorum offers a Digital Plant Maturity Model (DPMM) Assessment Tool that can help you determine where your plant (or network of plants) stands today, as well as what you need to do to reach higher levels.
You can use the tool to assess your digital maturity in these eight areas:
- Manufacturing Execution and Process Automation
- Process Development
- Laboratory Execution
- QMS
- Manufacturing Support
- Supply Chain
- People and Culture
- Cybersecurity and Operations
By guiding you across these separate but tightly linked activities that are critical to effective drug and device manufacturing, the assessment tool gives you the language and mechanisms you need to have productive conversations with the right stakeholders. BioPhorum encourages companies to use their results “for internal and external benchmarking, IT roadmap development, influencing software suppliers, transformation planning, investment justification, and dependency mapping”.
At the end of the process, you may realize that you need different maturity levels at different sites for different modalities. A biologics network, for example, may have a greater digital maturity level than a small-molecule network. According to BioPhorum, knowing this kind of information “lets you make conscious decisions on where investment is needed based on your business needs, as not all your sites or networks will need the same level of digital maturity. Knowing a site’s current DPMM level and your target level allows you to build a roadmap to help you get there”.
At STAEDEAN, we take a similar approach to assessing the digital maturity of Life Sciences organizations. We can work with you to identify gaps and provide an evolutionary roadmap for implementing the right infrastructure strategy, product strategy, data migration strategy, and cloud validation strategy.
As a Microsoft partner with the most comprehensive Enterprise Resource Planning (ERP) solution for Life Sciences organizations, we can help you leverage all of Microsoft’s solutions and platforms—including Microsoft Dynamics 365 Copilot—to get you to Level 3 or Level 4 of the Digital Plant Maturity Model so you can compete more effectively.
Some of our Life Sciences clients come to us with a legacy ERP system from SAP, Oracle, or another provider—or no ERP system at all. We help them switch to Microsoft Dynamics 365 and provide purpose-built modules for digitalizing STAEDEAN Life Sciences Supply Chain Management, STAEDEAN Life Sciences Quality Management, STAEDEAN Life Sciences Warehouse Management, and other industry-specific activities.
Other customers come to us on old Microsoft platforms, and we migrate them to the cloud while adding our modules. Still others already have the latest Microsoft ERP system and approach us to expand their supply chain, warehousing, and quality management capabilities, as well as to receive support with compliance.
STAEDEAN Life Sciences Management Is the Most Complete ERP Solution for Life Sciences
Convenient, configurable modules are purpose-built for Life Sciences organizations. Our solution can be added as needed, making it easy to scale so it grows with your specific needs
All of our solutions are specifically designed for Life Sciences organizations and can be easily configured without any expensive customization work. Very quickly, you can start to collect, integrate, and analyze the data you need across your production chain, while supporting your efforts to comply with standards and regulations such as GMP, GAMP5, FDA 21 CFR Part 11, and EU Annex 11.
STAEDEAN's pharmaceutical, biotech, and CDMO clients are located throughout the U.S., Europe, and Australia.