What Is the Bullwhip Effect and How Can You Reduce Its Impact?
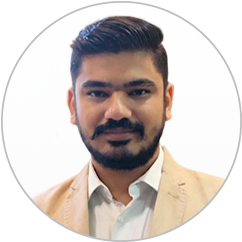
Table of contents
A bullwhip effect is an accelerated chain reaction that can impact industries. This usually leads to challenges for the supply chain as they need to quickly adapt to the changes. One of the biggest examples of the bullwhip effect was the Covid-19 pandemic in 2020, and there were adverse and favorable results.
Some industries, such as food manufacturing and groceries had increased demand, and the retail and restaurant business took a massive hit as governments across countries announced lockdowns and people preferred home-cooked meals. In 2020, there were 8,741 store closures in the U.S. and in 2021, 11,000 retail store closures in the UK. Some positives also came out of the pandemic. Since most of our time was spent indoors, home supplies were at an all-time high, and online giants such as Amazon and Ikea profited from this change in demand. Based on a report released by the U.S. Census Bureau, the total retail and food services sales in 2021 were up 19.3% from 2020.
At STAEDEAN, we try to understand challenges that plague our customers and develop solutions for Microsoft Dynamics 365 Finance & Supply Chain Management (D365 F&SCM), such as EDI Studio for electronic data interchange and Data Integration Solution for data integration, that can help our customers in the supply chain industry stay better connected through data synchronization, improve their intercompany communication, and streamline their order processing using Electronic Data Interchange or EDI.
In this blog, we will first explore the bullwhip effect and how it impacts supply chains and then explain how electronic data interchange and data integration can help you reduce the effects or help you be better prepared for the phenomenon.
What is the bullwhip effect in supply chains?
A bullwhip, as most of our readers might know, is a tool used to manage cattle and livestock. So, when a person uses a bullwhip, a small fluctuation caused by the flicking of the whip leads to a wave-like pattern. So, a bullwhip effect is based on the physics involved in cracking the whip, where a relatively small movement at the user’s end can cause the whip's wave pattern to increasingly amplify and cause a chain reaction.
When applied to the supply chain context, a small change in demand at the consumer's end can lead to a larger change at the wholesale, distribution, and manufacturer's end. So, the consumer is at one end of the spectrum and the manufacturer is at the other end. It is a small change at one end that gets amplified and escalates as it moves up the supply chain.
Therefore, any bullwhip effect creates an imbalance in the supply chain and leads to several issues, including insufficient supply of products or excess supply, customer complaints, and loss of goodwill, which can also result in loss of revenue. This could lead to products going out of stock or excess inventory that can force companies to offer discounts and cut prices to encourage buying.
What causes a bullwhip effect in the supply chain?
According to Forbes, the phenomenon was coined in the 1980s by economists at Proctor & Gamble. This could be due to several factors which we will delve into further in this section.
Demand changes from the retailer
If a retailer changes the number of orders that have been passed down the supply chain, this creates a ripple effect and affects wholesalers, suppliers, and manufacturers as they then have to cut down or increase production and arrange for other additional storage.
If retailers are forecasting increasing demand because of a sudden jump in sales or predicted demand which then crashes, that can cause a lot of problems as it escalates down the supply chain.
Communication issues
Very often, when documents are exchanged with incorrect information or not sent in a timely manner, it can result in improper lead time. Having processes in place for data quality checks and using technologies such as EDI messages can help you improve the document exchange process.
Lenient return policies
Although a great marketing tactic, return policies can sometimes work against you if retailers order products and return the product if it isn’t doing well in their store. This will result in excess inventory across the supply chain.
Order batching
There are several reasons why companies order excess inventory. They might anticipate demand based on historical data, or order a large batch for a better price, or due to expected manufacturing delays.
But this might be followed by a slump in demand from the retailer as they wait for the products to be sold off their shelves before ordering another batch.
Economies of scale
While manufacturing companies might use economies of scale to improve the cost and efficiency of their inventory, this might not always work in their favor if it doesn’t meet demand.
Price fluctuations and promotions
Retailers might share special discounts and cost changes to get inventory out or while opening a new store, which might increase demand temporarily. This will make it difficult to understand buying patterns and identify trends. If this is not effectively communicated down the supply chain, it could lead to demand distortion.
Relying on bad data
When retail chains, distributors, and wholesalers have disconnected systems and no quality checks, it is possible that they may have data silos, inaccurate data, and data duplication. If the organization uses data to make decisions about demand, this can hurt the supply chain and lead to excess inventory.
Example of bullwhip effect in practice
An automotive retailer releases a new marketing campaign for the holiday season and based on past data, expects sales to increase. The retailer will order more goods from the wholesaler, the wholesaler will then also increase their order based on the number of retailers they supply to, and the manufacturer will increase production.
But due to the pandemic strike, the market crashes since everyone is home and doesn’t want to invest in automobiles. Everyone in the supply chain will be stuck with the excess inventory that was forecasted. This could also work inversely, wherein the demand is predicted to drop, production is reduced, and finally, that leads to the scarcity of a product. Either way, this action from the retailer is amplified down the supply chain leading to major discrepancies between demand and available inventory.
What follows is exclusive offers and discounts to get consumers to the stores, or then it is time to make some tough decisions such as cost-cutting and writing-off goods as bad debts.
That’s the bullwhip effect in action, sometimes caused by an unprecedented event such as Covid-19. It starts as a slight oscillation of the whip’s handle, in this instance at the retailer’s end, and amplifies as the energy moves down the whip, which is at the manufacturer’s end. This wave-like oscillation is 3-4 times larger than the initial effect felt at the retailer’s end. So, the effect is felt the most at the manufacturer’s end, which is stuck with excess stock.
How can you reduce the impact of a bullwhip effect?
While some causes of the bullwhip effect can be controlled and monitored, sometimes sudden changes in customer demand and unnatural causes must also be factored in. Organizations that are better planned for changes in customer demand or market changes will better survive this phenomenon.
Clear communications
Using efficient technologies such as EDI for document exchange for starters that use global standardized formats can help companies streamline communication. It is also important to ensure EDI compliance while exchanging these messages. Additionally, clear communication between organizations can reduce any minor changes escalating into bigger issues.
Improving data quality
Organizations that connect their logistics and other systems with their ERP system have a better view of their data. Additionally, setting up a data governance strategy and investing in solutions that can help improve data quality will reduce errors and also help organizations improve decision-making and better demand forecasts for products.
Building resilient supply chains
Besides having a plan B when things go south, it is also important to act quickly when companies see a shift in demand. This doesn’t mean that companies should increase or reduce production and sourcing but set up a protocol for such situations wherein they reassess demand and market changes so that they do not misunderstand demand shifts.
Do you use Microsoft Dynamics 365 Finance & Supply Chain Management?
If you use D365 F&SCM, we have some great news! We offer Data Management Solutions that will reduce your worries and help you fast-track EDI implementation, integrate disparate systems, import and export data, streamline data entry, improve data quality, manage data distribution, ensure data security, enable data analytics, and more. Our solutions are embedded within D365 F&SCM, giving you a seamless user experience and negating the need to integrate with the ERP separately.
If you would like to learn more about EDI Studio and how it can help you streamline B2B communication with your trading partners, please download our solution factsheet from the link shared below.