How Can EDI Enhance Supply Chain Management in Dynamics 365—A Narrative
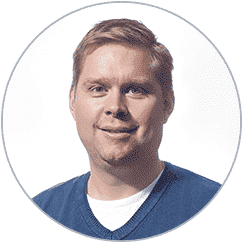
Table of contents
With the global Electronic Data Interchange (EDI) Software market estimated to reach USD 3,451.3 million by 2027, it is evident how much companies are relying on EDI. Among others, the three main business advantages that EDI offers are cost and employee efficiency, automated processes with fewer errors, and eco-friendliness. It can cut down your costs by eliminating the paper-based manual and monotonous work that requires you to invest a lot of time and resources. Besides, automated work helps in curbing the increasing environmental pollution substantially.
EDI helps organizations unburden some of the major workloads by streamlining the exchange of business communications internally as well as with its various stakeholders in the supply chain. With more and more companies adopting EDI, it makes sense to tap into its benefits already and stay ahead in your market.
How Can EDI Optimize the Supply Chain?
In this blog, we will be looking at the internal optimization of the supply chain process of a company through an imaginative narrative. Let’s call the company Ally, and assume it has several employees. To get deeper insights into what’s going on in its supply chain processes, let’s take four roles (the main characters in our story) in the company that are most affected and would seek an EDI solution:
- Sara, the Supply Chain Manager
- Chris, the Sales Manager
- Priyanka, the Purchase Manager, and
- Wally, the Warehouse Manager
The Challenge
Ally hired Sara a few months ago to see if she could optimize the supply chain processes. The company was growing, and hence needed a better supply chain.
Her job would be to analyze all the company’s supply chain processes and get a good insight into different areas to figure out what she could optimize.
Sara looked at the sales and purchasing departments. She found out that people in Chris’ and Priyanka’s departments were still processing orders manually. These were orders sent to business partners by e-mail, fax, and mail.
Parallelly, she also started analyzing the logistics part of the business. She understood from Wally that with the company growing, he had to process more orders. This was slowly reaching the maximum volume the warehouse could handle.
The Investigation
Sara wanted to help out all departments since she learned from Wally that an increase in the number of orders was inevitable. So, it would mean that the entire company’s processing capacity would reach the maximum in a few months.
The procurement and sales department in Sara’s previous company had switched to sending orders via EDI. That helped both the departments process many more orders quickly.
Sara, then, decided to find out if Ally could start using EDI. She inquired with the top 50 suppliers and customers to understand the current status of their digital transformation.
Apparently, 80% of them were already using EDI and were actually very excited to see Ally also moving to EDI since they were familiar with all the benefits of using EDI.
They gave feedback that Ally’s orders had an average of 20% incorrect and missed data entries, which resulted in more work for them in returns and adjustments.
Since EDI is not one standard format but includes numerous options and requirements, Sara started to map out all those factors immediately and concluded that 90% of the trading partners had different EDI requirements.
Her next thought was to relieve the warehouse and even save them from the work overload. For that, she evaluated if it was feasible to start using third-party logistics (3PL). It seemed that 50% of the products didn’t have to be handled or changed and could directly be sent to the customers. Those products were ideal for 3PL. That would reduce the workload in the warehouse, and consequently, make room for more growth.
The Solution
Ally is running Microsoft Dynamics 365 Finance & Supply Chain Management (D365 F&SCM). So, Sara needed to find an EDI product that would handle orders via EDI and was capable of doing 3PL warehousing.
Another requirement she had to look after was that the product was integrated into D365 F&SCM to make it easier for Ally’s employees—so that they didn’t need to change the ERP and business processes.
The product that could fulfill all their requirements—STAEDEAN's EDI Studio for D365 F&SCM!
This solution comes with triggers for sales and purchase order updates to send automatic EDI messages to your trading partners and automatically send tasks that need to be done by the 3PL.
Although EDI Studio is capable of supporting many different formats, Sara decided that it would be better to have the conversions done by an EDI VAN.
She would adjust the tutorial messages to the required format to communicate with the EDI VAN. The EDI VAN could then translate the message to the correct format the customer/vendors expected.
For the 3PL messages, she chose to handle the formats and processing in EDI Studio since that would be a more manageable number of configurable notifications.
To test the implementation, Sara started with 5 vendors and customers for the introduction of EDI. This controlled start was easier for Chris’ and Priyanka’s teams to adjust to the new way of handling orders.
Instead of resolving data discrepancies and conflicts via regular communication, the teams could see the validation issues inside Microsoft Dynamics 365 user-friendly forms. In the forms, the user can solve the data issues so the order can be processed further.
This new way of processing orders showed an increase in speed and accuracy. When evaluating with the “test” business partners, the feedback was that the orders were much more accurate. It was an easy setup fix if anything was wrong, and they noticed it was not repeating.
Not long after this first test, most communications were done via EDI. Only a few remained unchanged as these business partners were not yet capable of processing orders via EDI. However, once they would become capable, it was just a matter of changing a switch in EDI Studio.
Now that procurement and sales were working well, Sara and Wally started the project to move to 3PL. This, of course, had more impact on the business and Dynamics 365 to doing logistics. A new setup had to be created for the added warehouse(s) and products that were handled in the 3PL.
Since the purchase orders were already handled with EDI, the vendors would automatically receive the alternative delivery addresses. Nevertheless, they were also informed via other means of communication.
In parallel, the integration messages had to be created with STAEDEAN's Data Integration Solution for Dynamics 365 F&SCM. With an easy-to-use interface, multiple smart features, and the 3PL message tutorials, the configuration was soon completed.
This project was successful as well. Wally was delighted to see how the volumes through his logistics were way more manageable, and managing the 3PL was easier than he had worried about. The system was automatically dividing the logistical tasks over both logistic streams. So, he could see no challenges anymore in larger order volumes arising as a result of the company’s growth.
Those were the first steps Sara took in streamlining the supply chain operations. Now, she could start to focus on further optimization of the supply chain management, since D365 F&SCM (combined with EDI Studio) offers scalable possibilities.
The Next Steps
Optimizing their supply chain with EDI was very beneficial for Ally. Different departments got a quicker and smoother way of working, which realized the possibility of growth for Ally. Since everything was handled inside Dynamics 365 due to EDI Studio, the employees didn’t need to change their way of working. So, there was hardly any business process change they needed to adapt to.
Just like Ally, you can benefit from EDI too. We understand that optimizing the supply chain can pose a real challenge. Opting for an EDI solution can benefit you in the long run. If you would like to learn more about EDI and how to get started with EDI implementation for your D365 F&SCM ERP, we recommend that you download our free EDI Toolkit shared below.