Questions to Ask Your Engineers and Manufacturers Before PLM-ERP Integration
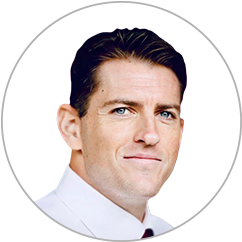
Table of contents
As a manufacturing company, you might be planning for PLM-ERP integration to efficiently control your processes, from idea generation through product launch to end of life. The PLM system (Product Lifecycle Management) and ERP (Enterprise Resource Management) are critical in developing and managing your products.
You must know that integrating your PLM and ERP systems directly impacts the end-users, in this case, the engineering and manufacturing teams. It is, therefore, essential that when on the lookout for a PLM-ERP integration solution, you have discussions with your internal teams and consider their input, so you invest in a solution that maximizes profits and boosts productivity.
While providing PLM-ERP integration for Dynamics 365 Finance and Supply Chain Management, we have interacted with multiple companies wherein the management and IT team benefitted from discussing specifics about the PLM-ERP integration solution with their engineers and manufacturers.
This blog shares a few questions you can talk about with engineering and manufacturing teams, so you are better prepared for your integration’s functional requirements.
Questions to ask your engineering team before PLM-ERP integration
1. What PLM data do you share with other legal entities and operating companies?
The first question that must be discussed with your engineers is the PLM data they often have to share with different teams in the manufacturing supply chain.
You can consider the following:
-
The data requested by manufacturers to produce and assemble products
-
The bill of materials (BOMs) required by the procurement team to buy the right materials
-
The product data that the warehousing and storage teams use
-
The data needed by the sales team about all the product specifications
2. What is the current throughput yield of the products?
This question is asked to check the accuracy of the data communicated from the PLM system to the ERP. A low throughput yield (YTP) or first-pass-yield indicates a high percentage of scrap and rework which could stem from incorrect PLM data.
3. What kind of ERP data do you want insight into while working on the product?
While predominantly PLM data is shared across several legal entities, sometimes, operational and logistical data in the ERP is essential for the engineers working on the product. This is especially beneficial when multiple products on the production line require changes and you have open production orders.
Check what kind of data would be valuable for the engineers while developing your products so they can better monitor and control product changes with insight into the logistical impact of the products.
4. Which daily data import processes do you want to automate?
With disconnected PLM and ERP systems, your engineers may be doing the entire activity of data import manually, consuming a lot of time, effort, and productivity hours.
For instance, some companies depend on data entry tools, or Excel, which must be updated daily and shared via email or share folders to the manufacturing teams, who then update it on their product master sheets.
5. Where is the engineering and design data located?
You must ask this question to know where all your engineering and design data is stored, such as the PLM, CAD, PDM, etc.
Outdated data needs to be updated in every single place, and you must collate and gather the data to prepare for the integration.
6. What is the format and type of the PLM data?
The format of the data residing in the PLM (or CAD, PDM, etc.) is essential to know if it is compatible with the ‘output format’ of the PLM-ERP integration solution.
While most manufacturing companies have Excel, XML, or JSON data formats, it is good you have this sorted from the start.
7. How much legacy data exists in your current PLM system(s)?
When integrating your PLM and ERP systems, you could be dealing with legacy data dating back 10 to 15 years. Discussing this question with your engineers will help you know the amount of data cleanup and migration required and if there are any data sets that you must get rid of.
8. Which skillsets are required for the integration to be successful?
Along with other teams, including IT, your engineers have a say in the best integration solution for your business.
You can consider the following:
-
Do you want a customized, low-code, or out-of-the-box solution?
-
Would a cloud-based or on-premises solution be more suitable?
-
Can customizations be handled in-house, or do they require external dependency?
-
Do you have one legal entity set up, or are there merger and acquisition plans in the future?
-
Who will oversee and manage the change in data ownership after integration?
Questions to ask your manufacturing team before PLM-ERP integration
1. What is the effort from each manufacturer dealing with product data?
Just like importing data from the PLM is cumbersome on the engineering side, it is just as much, or even more, time-consuming for the recipients at the manufacturing end.
Different teams on the shop floor invest plenty of time and effort into collating and updating the product data in the relevant locations or master sheets. Any change in the item master impacts all the modules, such as purchase, sales, production, etc., resulting in duplication of effort.
This information will offer insight into the urgency of PLM-ERP integration, as you will realize you are losing money in lengthy, manual operations and compare it with the ROI of the PLM-ERP integration.
2. What data do you need from the PLM to the ERP?
Check the data your teams operating in the ERP need from the PLM system to execute daily business. You can corroborate this data list with the list shared by your engineers to ensure all the data required is listed.
Usually, the following data is integrated:
-
part data
-
product revisions/ updates
-
attributes
-
product status
-
routings
-
bill of processing
-
engineering documents
3. How many legal entities do you operate with?
Based on your business, you could be dealing with one, two, or multiple legal entities. You will need to consider the integration strategy as you could have data move from:
-
the PLM or CAD to the engineering company with PLM integration or
-
the engineering company to the manufacturing plant.
This also helps you determine whether to build your integration based on a one-to-one or one-to-many relationship.
4. What is the percentage of defective manufacturing and product recalls?
Like checking throughput yield with your engineers, you must check the percentage of defective manufacturing with the production staff. This lets you gauge the degree of incorrect manufacturing, ad hoc costs due to repairs, and delayed productions.
Once you do a root cause analysis, you can get a clearer picture of the exact problem areas within the process and ensure the PLM-ERP integration solves them.
5. What is your data strategy post PLM-ERP integration?
This key question guides you on how data will be utilized by the manufacturing, purchasing, and warehousing team after integrating your PLM and ERP.
You can consider diving deeper with the following:
-
Do you want to automate the data import processes, or do you have add-on requirements such as optimization?
-
Do you have plans to further utilize this data with dashboards for other data transformation processes?
6. Do you need to migrate existing ERP data onto one system?
In case you are adopting a new ERP system or have multiple ERP systems running, it is critical to have some standardization in place.
Think through the following:
-
Do you want to implement a new ERP system?
-
How do you want to migrate existing data?
-
What data requires cleaning or sorting?
All of this must be analyzed to ensure you do not miss integrating vital data.
7. Who will lead the integration project from the manufacturing side?
Discuss with your manufacturers to identify the proper representative of the manufacturing operations. This individual(s) can collaborate and communicate with the implementation partner on the manufacturing functional requirements of the integration, as they will be familiar with the ERP.
Want to get started with PLM-ERP integration?
While mostly members from IT, management, inventory staff, and finance team are involved in deciding the type of PLM-ERP integration solution for your business, it is always a significant value-add to incorporate the perspective of your manufacturing and engineering teams as well.
Going through a comprehensive process is better than having disruptions during the implementation. This also helps you identify critical areas where your engineering and manufacturing teams might require training after PLM-ERP integration.
If you are using (or planning to use) Dynamics 365 ERP, you might be interested in exploring our PLM-ERP integration solutions. We offer out-of-the-box PLM integrations for Siemens Teamcenter, PTC Windchill, and a configurable PLM integration framework for other systems.
You can explore more about our solution offerings in the factsheet linked below.
If you are still finalizing your ERP system, or are not on Dynamics 365, you can look into our guide to select the right PLM integration.