What is the ROI of our PLM-ERP Integration for Dynamics 365? A 5-Step Guide
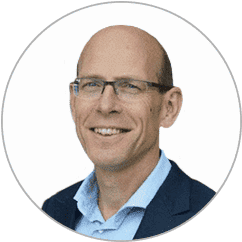
Table of contents
As a manufacturing company looking for integration solutions to connect your PLM system with Dynamics 365 ERP, one question at the forefront of your buying decision would be: What is the return on investment (ROI) you will gain from the integration?
Our PLM-ERP integration solution enables several manufacturing enterprises to streamline and simplify their data import process from PLM to Dynamics 365 ERP. During our customer interactions, many manufacturing companies assume that a simple import-export code could generate the same ROI.
However, when we explained how the ROI of our PLM-ERP integration is much higher, as it automates several processes and guarantees data quality, they quickly realized the clear distinction.
This article will share how you can calculate the ROI of our PLM integration for Dynamics 365 and maximize profitability with the solution's benefits.
To understand what the ROI of our PLM-ERP integration solution is, we will discuss the following:
Disclaimer: The ROI model calculates the 'net present value' cash flow impact over a 5-year period, as short-term and long-term benefits exist. We have modeled the ROI calculation using an example based on an average manufacturing business. However, these numbers are subject to vary based on the business case.
How to calculate the ROI of STAEDEAN’s PLM-ERP integration solution?
Calculating the ROI of the integration can be a complicated process. But it’s essential to know how well your business is doing and understand the long-term returns of the PLM integration.
While the number may never be completely precise, as the integration impacts virtually every aspect (both quantifiable and unquantifiable) of your manufacturing organization, it is possible to make an approximate estimation to measure the ROI and overall value of the PLM-ERP integration software.
Step 1: Calculate the expenses of transferring PLM data to Dynamics 365 before PLM-ERP integration
When not using a PLM-ERP integration, manufacturing companies could be using either of the two methods to send data from the PLM system to Dynamics 365 ERP:
-
Building a customized connection between PLM and ERP with coding and in-house or contracted third-party resources.
-
Using a manual data import process to send data from PLM to ERP.
In both the situations above, many processes, such as data import, data quality, and validation checks, are not automated. These manual processes lead to several operational challenges and delays in coordination and communication.
To know how much it would cost an average manufacturing company to send PLM data to Dynamics 365 without a direct integration, you need to know all your direct and indirect costs, the number of employees involved with product data, and the percentage of time each employee spends dealing with product data.
In a typical manufacturing company, the teams involved with product data include Design Engineers, Manufacturing Engineers, Production Managers, Procurement Agents, Sales Engineers, and Service Technicians.
You must consider the following costs:
-
Number of employees and effort involved in accessing the PLM data from multiple sources
-
The volume of the data you must import from PLM to Dynamics 365 each time
-
Time and effort to validate and check the quality of the data imported
-
The time required by the production team to report product revisions and changes back to the engineers
-
Time and effort for releasing products to the various companies or legal entities
-
The effort to track the product lifecycle stage and handle product attributes
-
Time lost in fixing data errors due to manual entry processes
Let’s take an example to understand this better.
Manufacturing Company XYZ uses a manual import-export process to send PLM data to Dynamics 365. The teams handling product data include 5 Design Engineers (in the PLM system), 5 Manufacturing Engineers, 3 Procurement Agents, 4 Sales Engineers, 3 Service Technicians, and 2 Production Managers (operating in Dynamics 365 ERP).
The percentage of time each employee spends dealing with product data differs. For instance, a Production Manager spends only 10% of their daily time in the system managing product data as they are more involved on the shop floor, as opposed to a Design Engineer, who spends about 40% of their daily time handling product data with different product versions, designs, and drawings.
In the table below, we calculate the total cost to manage product data manually:
*Data for the average annual cost per employee has been taken based on industry standards provided by Glassdoor.
To calculate the total cost for each team, (let’s say the Design Engineering team), we do the following:
The number of employees in the team handling product data (5) x The average annual cost per employee ($70,000) x The percentage of time each employee spends on product data (40% or 0.4) = Total cost to manage product data manually ($140,000).
Applying the same calculation for all 6 teams, the total annual direct cost for Manufacturing Company XYZ to import product data from PLM to ERP is $525,600.
Step 2: Calculate the investment in our PLM-ERP integration solution for Dynamics 365
Before we can move on to calculate the cost savings and ROI, we must consider the investment required for our PLM-ERP integration.
For a detailed understanding of the cost, read: What Is the Cost of STAEDEAN’s PLM-ERP Integration for Dynamics 365?
The cost of our PLM-ERP integration is based on:
- Software licenses (includes the base price, cost per user license, upgrades, and minimum essential support)
-
Consulting services (includes installation, implementation, and training)
-
Additional support services (includes support plans with a certain number of tickets)
Taking the above example of Manufacturing Company XYZ using Microsoft Dynamics 365 Finance & Supply Chain Management and requiring 50 user licenses.
The consulting and implementation services cost $30,000 for Year 1 (considering the company has already implemented D365 F&SCM, activated the Engineering Change Management (ECM) module, and completed a primary analysis of the data to be imported). For the next 4 years, a minimum consultation fee is applied to cover any upgrades related to CAD or other internal data systems.
For additional support services, Year 1 stands at $0, as we offer minimum standard support within our software license fee. For the subsequent years, we have factored in support fees with a certain number of tickets to assist the customer with quick resolutions.
No investment is required toward hardware purchase, as our PLM-ERP integration is a cloud-based solution.
In the table below, we calculate the total investment for our PLM integration embedded in Dynamics 365:
*Prices are based on the current conversion rate from euros to USD. The final price will include a conversion fee at the processing time and could vary based on the business case.
Step 3: Calculate the difference in expenses and direct costs before versus after the integration
As the example calculation in Table 1 shows, it costs a manufacturing company about $525,600 per annum to manually send PLM data to Dynamics 365. This would bring the total cost for 5 years to $2,628,000.
On the other hand, investing in a direct PLM-ERP integration, as calculated in Table 2, drastically reduces this price, costing only $178,080 for 5 years.
The difference in your 5-year investment to send PLM data to Dynamics 365 before and after the integration is calculated by:
Total investment in manual data import ($2,628,000) – Total investment in PLM-ERP integration ($178,080) = $2,449,920.
With a staggering difference of $2,449,920, the PLM-ERP integration reduces your investment in managing product data by almost 14 folds.
Step 4: Calculate the direct costs you will save due to process efficiencies after integrating your PLM system with Dynamics 365
After implementing a PLM-ERP integration solution for your business, the following processes related to product data movement are fully automated:
i. Picking and dropping the data from PLM to Dynamics 365
ii. Ensuring data quality
iii. Validating the product data
iv. Managing product versioning
v. Releasing products to respective operational companies
vi. Offering insights on products and product lifecycle
vii. Handling product attributes
The key ROI of our PLM-ERP integration solution is that the automation drastically reduces the time your employees will spend dealing with product data. An integration solution eliminates the need for data cleanup and reduces the product’s service and warranty claims.
Using the same example of Manufacturing Company XYZ, we can estimate the cost savings due to process efficiencies after the PLM-ERP integration. To know how this would work for you, we recommend using the same model and adding your data to deduce your current costs. We have mentioned industry metrics ranges for the expected improvement as a guideline.
After the integration, the improvement percentage experienced by each time is different. Some teams (such as Design Engineers and Manufacturing Engineers) are more involved with product data and, therefore, will experience a greater positive impact from the integration.
In the table below, we calculate the cost savings due to process efficiencies for different teams:
*Industry metrics for the improvement percentage are based on our experience implementing PLM integrations for manufacturing companies. It denotes the average expected percentage increase in process efficiency after implementing a PLM-ERP integration solution.
To calculate the Annual cost savings (for example, the Design Engineering team), we do the following:
Total cost to manage product data manually ($140,000) x Improvement percentage after implementation (40% or 0.4) = Annual cost savings ($56,000)
Applying the same calculation for the remaining 5 teams, the Total annual cost savings for Manufacturing Company XYZ after PLM-ERP integration is $173,220.
Step 5: Calculate the additional cost-saving benefits after implementing the PLM-ERP integration
Once you invest in our PLM-ERP integration solution, you can expect additional cost-saving benefits for your manufacturing business:
Cost-saving operational benefits
-
Streamline operations as business processes are now quicker and more efficient
-
Increase the speed of manufacturing with faster cross-departmental data sharing
-
Shorten lead times with lesser errors due to process automation
-
Enhance collaboration among all supply chain stakeholders
Cost-saving customer benefits
-
Improve customer satisfaction
-
Reduce customer churn and increase customer retention
-
Deliver products to customers more timely
-
Strengthen customer relationships for the long-term
Cost-saving strategic benefits
-
Generate higher revenue by spending more time on research and development
-
Increase profitability with maximized operational efficiency
-
Stronger competitive positioning in new markets
-
Enhance user experience with a unified, standardized, and embedded solution
On average, based on the above additional cost-saving benefits, you will save a minimum of 20% on operational expenses with an automated PLM-ERP integration solution.
You can read more about the benefits of our PLM-ERP integration solution here.
The ROI of the PLM-ERP integration over a 5-year period
To know about the long-term benefits and ROI gained from the integration, let’s model the ROI over a 5-year duration.
Continuing with the same example of Manufacturing Company XYZ, let’s assume the baseline annual revenue for the company is 200 million dollars ($200,000,000). To calculate the minimum revenue improvement (gross margin increase) for the 5 years, we assume a 0.5% percent in Year 1, 1% in Year 2, 2% in Year 3, 3% in Year 4, and 4% in Year 5.
Although industry standards claim a revenue improvement upward of 60 to 70%, existing research cannot quantify the exact percentage. Hence, we have considered the minimum expected improvement based on the cost savings mentioned above (in Table 3).
Regarding the investment in our solution, Year 1 includes the cost of software licenses and implementation; for the subsequent years, only the software license fee (with minimum consulting services) is considered.
Since the implementation time is relatively short, you will see immediate benefits (in terms of daily activities) and begin experiencing additional benefits within 6 months of Year 1 (as reflected in the gross margin increase and cost savings).
In the table and graph below, we calculate the ROI of the PLM-ERP integration over a 5-year period:
To calculate the gross margin increase for Year 1, we do the following:
0.5% of the baseline annual revenue ($200,000,000) = $1,000,000
Following the same calculation for the remaining years, at the end of the 5 years, the expected gross margin revenue increase will be $8,000,000.
You will also save on costs (including operational expenses) as most previously manual processes are now fully automated. We assume the cost savings for Year 1 to be 30% of the Total annual cost savings (calculated in Table 3).
With time, you will continue to experience cost savings as the long-term benefits of the PLM-ERP integration materialize. These long-term benefits include streamlined cross-functional communication, reduced production errors, lesser product recalls, increased production speed, etc.
So, for Year 2 and Year 3, cost savings will incrementally increase, at a minimum of 40% and 50% of the Total annual cost savings. In Years 4 and 5, the cost savings will remain stable at an average of 30% of the Total annual cost savings.
To calculate the cost savings, for Year 1, we do the following:
30% of the Total annual cost savings ($173,220) = $51,966
You can apply the same calculation for Years 2 through 5 with their respective percentages.
To calculate the Net cash flow for the 5 years, we do the following:
(Cost savings + Gross margin increase) - Investment in solution = The net cash flow
Begin your journey of PLM integration with Dynamics 365
With an understanding of the return on investment you can expect from our PLM-ERP integration software, we hope you are better positioned to decide whether it is the right solution for you.
Investing in a PLM integration solution embedded within the Dynamics 365 environment maximizes operational efficiency without the hassles of designing, coding, and associated costs. Ensuring data quality and ownership, the integration solution can be implemented within two to four weeks.
You can talk to our experts, who will guide you on the best approach to integrate your PLM with Dynamics 365.
Alternatively, you can download the solution factsheet to learn more about the solution offerings.