PLM-ERP Integration: 10 Mistakes to Watch Out For!
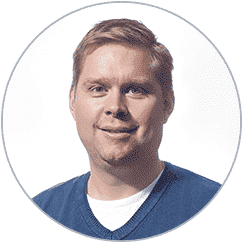
Table of contents
Using a PLM-ERP integration solution to connect your engineering and manufacturing worlds must be done right the first time to avoid additional costs, effort, and time for your manufacturing company. If you plan to integrate your PLM and ERP systems, you must be aware of certain mistakes that could arise throughout the process and avoid them.
We, at STAEDEAN, have assisted global enterprises in integrating their PLM systems with Dynamics 365 ERP. We have seen the common mistakes manufacturers tend to make while integrating their PLM and ERP systems and have helped resolve them.
This article will share the top 10 mistakes you must avoid before, during, and after the PLM-ERP integration to ensure smooth and successful integration.
What are the common mistakes before integrating PLM and ERP?
1. Using a manual import process
Some manufacturing companies believe a simple 'import-export' code can be used to send PLM data to the ERP manually. Manual entry processes could cause data duplication as there is no control over the data. Apart from being a time-consuming process, it could also result in data loss. The product items are not engineering-controlled, increasing the workload on the staff.
When integrating your PLM and ERP, look for a quick, reliable way to connect the two systems and avoid going the manual route.
2. Not considering all the factors for integration
Several factors come into play before you decide on the type of PLM-ERP integration you want. Not considering factors such as your functional requirements, the scope of the budget, whether you want to build or buy the integration, and what ISV or implementation partner you should look for could lead to an integration process with little to no direction.
Ensure you have every detail planned out for the type of PLM-ERP integration. Follow a well-planned methodology to accommodate scalability and ensure everyone is aligned.
3. Unfulfilled prerequisites
When planning to integrate your PLM and ERP systems, you must complete a specific set of prerequisites to ensure a meaningful sequence of processes. In some situations, companies have not implemented the ERP yet, and are beginning to look for an integration solution. There are also cases where businesses look for new PLM systems while searching for integration simultaneously.
The integration you select depends on the type of PLM and ERP systems you have in place. Therefore, you must have that defined before exploring integration options. You must prepare your ERP and PLM to ensure the integration is compatible to work with them.
What are the mistakes during PLM-ERP integration?
4. Underestimating data migration
The entire concept of PLM-ERP integration is centered around data. You need to have product data sent from the PLM to the ERP. Companies often underestimate, if not miss, the significance of data migration. Especially if you want to implement a new ERP system, wherein data loss issues could occur, and you might miss integrating vital data.
During PLM-ERP integration, you must migrate all your data and decide what to do with the existing data in both the new and old ERP and PLM systems.
5. Less focus on data cleaning and conversion
Let’s say you have an ERP running for two years with thousands of transactions made on your products. With such a vast amount of data, there are many decisions around how you want to clean up and convert the data while integrating your ERP with the PLM. Cleaning your data will avoid inconsistencies in the data location and format.
You need to evaluate whether to do conversion jobs on the data, which includes converting all the data to product and version numbers or leaving them as it is. These data cleanup and conversion jobs will affect the way you carry out your integration.
6. Inadequate analysis of data
Before implementing the integration, you must thoroughly understand what data you want to transfer and where it is located. This ‘data’ must be carefully identified, analyzed, and then selected to import from the PLM to the ERP. If you lack understanding of the format and type of data you want to transfer, it could be the starting point of a disorderly PLM-ERP integration.
Make sure you take time to analyze the data you want to integrate and the data format (XML, Excel, etc.) based on which the integration can pick and drop your product data.
7. Not sticking to set timelines
While implementing the PLM-ERP integration, you will have defined timelines for different phases of the implementation process. Ensure that you do not get ahead of yourself or become hasty with the set plans, as it needs to be done accurately and precisely to offer you problem-free integration.
To reap the long-term benefits of the PLM-ERP integration, plan each process with set schedules and minimize adjusting or deviating from the timelines.
What are the common mistakes after PLM-ERP integration?
8. Missing to test the integration
Most companies might think that the integration process ends once the PLM-ERP integration is set to be used by the end users. Skipping the step to test the integration with user acceptance testing (UAT) is vital as it determines if troubleshooting is required.
You must conduct a data quality check and test whether the integration produces the desired result.
9. Increased customizations
After the integration, you might add more data sets to be transferred from the PLM to the ERP. While this isn’t incorrect, it does result in additional effort for the implementation team, as they must accommodate changes. This leads to more time to carry out the integration, as you must repeat the entire preparation, configuration, and testing process for the new data sets.
Try to minimize repeated customizations to the integration, which you can do by thoroughly analyzing the PLM data you want to transfer.
10. Ineffective change management
After integrating your PLM and ERP systems, there will be a change in the ownership and maintenance of product data among the engineering and manufacturing teams. If not communicated properly, this shift in how data exists could lead to confusion around what data is owned by which system.
You must train the end-users involved in servicing, handling, and selling products, so they know how to read, translate, and use the data to carry out engineering and manufacturing activities.
What is the impact of PLM-ERP integration mistakes on your business?
There is a massive impact of a faulty PLM-ERP integration on your business. Some of the significant consequences include the following:
-
Loss of capital and investment as you would have an unsuccessful integration
-
Delayed production as the flawed integration may take a long time to fix
-
Operational issues as you don’t have the correct products and versions
-
Repeated effort and waste of time to do damage repair
-
Miscommunication and misalignment among the departments due to unclear data
How can you get started with PLM-ERP integration?
As a manufacturing company, you must be mindful of all the mistakes discussed above and try to avoid them to ensure a first-time-right PLM-ERP integration.
The next steps you can take are:
1. Look for a PLM-ERP integration that you can implement easily and quickly
2. Identify an implementation partner with proven expertise in integrating the PLM and ERP systems you use
3. Begin discussions and planning on what you want to achieve with the PLM-ERP integration
If you are using (or planning to use) Microsoft Dynamics 365 ERP, you might be interested in exploring the PLM-ERP integration solutions we offer embedded in Microsoft Dynamics 365 for Finance and Supply Chain Management.
We offer out-of-the-box PLM integrations for Siemens Teamcenter and PTC Windchill. Additionally, we provide an accelerated PLM integration framework that you can easily configure for any other PLM, PDM, or CAD systems.
Explore more about our PLM-ERP integration solution by checking out our factsheet, which gives you a peek into:
-
What the integration solution can do for your business
-
Benefits of PLM-ERP integration
-
Features of the integration solution