Managing Product Data in PLM and ERP: The What, Why, and How
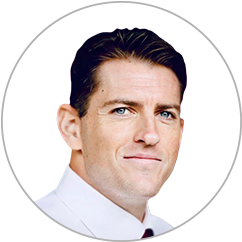
Table of contents
72% of manufacturing managers consider data sharing to improve operations within the business, according to a Boston Consulting Group study. As a manufacturing business aiming to become digitally mature, it is crucial you have the right technology to store, manage, and share your product data.
At STAEDEAN, we help global manufacturing businesses manage their product data efficiently through cloud-based PLM integration solutions embedded in Dynamics 365.
This article will discuss everything manufacturing companies need to know about product data by answering questions on:
- What is product data in the manufacturing industry?
- What are the types of product data?
- Why is it important to manage product data?
- Why is it challenging to handle product data?
- How can you manage product data efficiently?
- How to get started with managing product data?
What is product data in the manufacturing industry?
Product data refers to all the information related to a particular product type within your manufacturing business that offers end-to-end details about the product type, sub-types, and all associated documentation.
In a typical manufacturing company, multiple systems host different product data. The PLM system contains the concepts, designs, and engineering information about the product, and the ERP possesses data around the logistics, pricing, and production of the product.
What are the types of product data in a manufacturing process?
For an average manufacturing business that uses PLM and ERP, two types of product data items exist:
i) Engineering items: These refer to the finished goods to be manufactured where design is part of the engineering team. These items reside in the PLM and include product data related to the product's design specifications, drawings, descriptions, properties, and engineering iterations.
ii) Standard items: These are the list of parts required to make the finished product and sub-parts purchased from suppliers. Examples include consumables, fixtures, tools, packing items, and key assembly items.
Depending on your business situation and the legal entities you operate with, you could have more product data and item types.
Some examples of product-relevant data include:
- Bill of materials (BOM)
- Bill of processing (BOP)
- Part data
- Product versions/ revision data
- Attribute lists
- Product structures
- Routings and mapping
- Product status information/ product lifecycle stage
- Engineering change orders (ECO)
- Engineering change requests (ECR)
- Engineering documents and links
- Engineering change information
Why is it important for manufacturers to manage product data?
Product data is at the heart of manufacturing. It is the basis of the entire manufacturing process from order to delivery.
Manufacturers use product data to obtain product designs and drawings and translate them into manufacturing jobs. The product data is used by different teams (internal and external) throughout the production process, be it designers, engineers, procurement, suppliers, or manufacturers.
Any error in product data has a massive impact on your entire process leading to defective manufacturing, supply chain disruptions, and production halts. Therefore, manufacturers must manage their product data efficiently to maximize productivity and eliminate communication silos and costly reworks.
Adopting technology that increases the sharing of product data throughout the organization to streamline operations is a good starting point.
Why is it challenging for manufacturers to handle product data?
Today's customers want specialized products and short lead times from ordering to product delivery. To respond to customers' needs, manufacturers rely on product data to manage their products efficiently.
However, all product data cannot be found in one location. This data is spread across different systems, such as the PLM, PDM, CAD, and ERP systems, making it challenging for manufacturing companies to manage it in one location.
You have data islands when your product data is running in silos across multiple systems. Not having data synchronized and updated makes you unable to share recommendations or timely updates, resulting in missed opportunities.
Different teams deal with varying sets of data and formats, leading to inconsistencies, and it becomes challenging to track changes in product design or manufacturing, hurting your business.
With your product data sitting in disconnected PLM and ERP systems, you, as a manufacturing company, will struggle with manual paperwork, slow response times, lack of data visibility, and operational delays.
How can manufacturing companies manage product data efficiently?
To stay agile while managing product data that lies in several software systems, manufacturers require a standardized method of creating, sharing, and maintaining product information. You can achieve this quickly by connecting multiple software systems (PLM, PDM, or CAD) to your ERP with an integration solution.
A PLM, PDM, or CAD integration with your ERP automates several business processes within your manufacturing company, offering benefits such as:
- Increased operational efficiency with real-time access to data
- Reduced time to market and enhanced productivity
- Streamlined supply chain with reduced errors and manual operations
- Strengthened interdepartmental collaboration with simplified communication
How to get started with managing product data using a PLM-ERP integration solution?
When looking to integrate your PLM, PDM, or CAD system with your ERP, you can consider the following:
1) Connect with your engineering and manufacturing teams to discuss the idea of a PLM-ERP integration.
2) Define the nature of the integration solution you require.
3) Analyze your current PLM and ERP systems and look for vendors that offer integrations supporting those systems.
For instance, we offer intuitive and configurable PLM integrations for businesses using Dynamics 365 as the ERP.
How can we help you manage product data with a PLM-ERP integration solution?
If you use/ plan to use Dynamics as your ERP system (Dynamics 365 Finance and Supply Chain Management or Dynamics AX), you could explore our PLM-ERP integration solutions.
We offer out-of-the-box PLM integrations for Siemens Teamcenter and PTC Windchill. Additionally, we provide a PLM integration framework that you can easily configure for other PLM, PDM, or CAD systems.
Our PLM-ERP integration automates many processes related to product data movement, such as:
- Picking and dropping the data from PLM to D365
- Ensuring data quality
- Validating the product data
- Managing product versioning
- Releasing products to respective operational companies
- Offering insights on products and product lifecycle
- Handling product attributes
To begin your journey of managing product data using PLM-ERP integration, check out the whitepaper we've linked below.