The Three Main Advantages of the Internet of Things (IoT) for Manufacturers
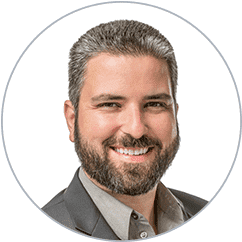
Table of contents
As we mentioned in our post on February 6, there are many possible ways the internet of things can benefit manufacturers. From product development to delivery and after-sales service, connected devices show the potential of huge advantages. There are three main areas of benefit for manufacturers associated with the internet of things—the design, development, and manufacture of products; tracking and improving products throughout their life cycle; and the management of the assets used in the process.
Closing the loop in product design and testing
In product development and testing supported by the internet of things, connected sensors on product components can deliver detailed information about the performance of product and materials in real-life conditions. Manufacturers of aircraft, cars, train engines, and other transportation machinery place devices on engines, components, or complete products as they take them through their paces and determine their performance, safety, durability, and other critical values. One STAEDEAN customer, in the F1 Team, a maker of race cars, produces as much as 40 terabytes of data in every test run. Mining and analysis of the accumulated data help the company adjust processes, design, and bills-of-material to create faster, more reliable, and safer cars, planes, or trains. Today, the sensors these manufacturers use are not always on the internet of things, which introduces a certain inflexibility. If all the placed devices were connected, engineers could review the data in real time, quickly adjust test runs or environmental conditions based on what they see, and use the feedback sooner in production.
Connected lifetime tracking of products
Given the permission of their clients, manufacturers could also keep tabs through the internet of things on how their products do in the next stage of their existence—once they are out of the factory and in use by customers. They could immediately spot any potential issues in design, components, and materials, and understand much better how customers actually use their products. Based on the information they receive and analyze, they could help customers avoid breakdowns and performance problems, and revise the design of products and components to achieve more durable and higher-performing results. In learning from the internet of things about the real-life usage of their products by customers, they probably would come across usage scenarios and conditions they did not anticipate, and could then modify their designs to better support the productivity and safety of their customers. For example, if manufacturers make machines that enable customers to produce devices or components, it would likely be of advantage to understand the actual workloads and how they change over time.
Better control over resource utilization
The internet of things could also help operations managers ensure the utilization of their equipment and facilities is at 100 percent or as close to it as possible, minimize downtime, and help identify and address any bottlenecks or under-utilization to maximize throughput. In global enterprises, the internet of things could provide a data stream that results in a comprehensive view of the productivity and performance of plants and equipment, allowing managers to report on the information by product, country, facility, vendor, and other criteria. Connected sensors could also support inventory management, prompting procurement to act when levels of required materials or components fall below a certain level. Or, they could ensure the productive utilization of expensive machinery and equipment by initiating production only when a preset threshold of demand has been achieved.
Insight from data streams in the internet of things
The internet of things and big data go hand in hand. Within very little time, connected sensors can produce huge masses of information. To make all that data meaningful and actionable, manufacturers need to take advantage of the right business intelligence and reporting tools. They also need to find ways to loop their findings into product design and engineering. For that, there needs to be a close connection between data gathering, analysis, and product life cycle management (PLM) systems. STAEDEAN Advanced Discrete Manufacturing provides such PLM integration in addition to supporting all operational aspects of a manufacturing company. It also includes a layer of BI capabilities to enable sound, realistic decision-making, forecasting, and planning based on data evidence.
Anytime and anywhere manufacturers use expensive, complex machinery as a key asset in production, connected sensors in the global internet of things can report on output, materials, and key quality and performance metrics. No longer would teams of people have to travel to visit production sites to record their findings manually. Data from the internet of things could draw immediate attention, followed by timely, corrective action, such as repair, maintenance, or replacement.
It does not matter where in the world the data generated through the internet of things originate. Much like robots, connected devices in the internet of things can report from production, exploration, and test environments that are not safe or accessible for humans—in orbit; the bottom of the ocean; toxic, hot, or extremely cold conditions; or deep underground. From there, sensors can provide real-time data to help people understand the performance of machinery and materials, so they can more effectively drive performance, plan materials, design products, and elevate their quality.
Systems integration and two levels of asset management
Advanced Maintenance and Service, a component of Advanced Discrete Manufacturing, allows manufacturers to track and maintain their own and customers’ machinery and equipment in integration with the internet of things and a company’s ERP system. The connected devices of the internet of things themselves are assets that need to be procured, deployed, tracked, and maintained, another area where Asset Management can help. STAEDEAN Business Integration Solutions such as Connectivity Studio can ensure that the manufacturing infrastructure is seamless and that information can flow from the internet of things to Asset Management and the ERP system, reaching the people who need to make decisions and direct production.
The internet of things in your strategy
At a more strategic level, companies aiming to gain the full benefit of the internet of things need to incorporate it into their planning and business process management (BPM), so they can produce long-term value and follow a path of continuous improvement. In that effort, a BPM solution such as STAEDEAN RapidValue, designed to connect strategy, resources, and processes, can be invaluable in translating the potential of the internet of things into measurable benefits.
The internet of things also eases the tracking of employees and teams. In the next blog post, scheduled for February 25, we consider that application for both manufacturing and construction industries and also see what the internet of things can offer construction companies.
To share your ideas, questions, or experience with the internet of things, please connect and drop us a line.