6 Challenges in Engineer-to-Order Manufacturing Solved by PLM and Microsoft Dynamics 365 ERP Integration
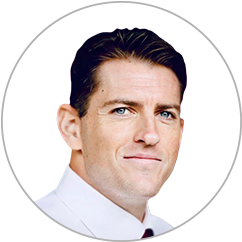
Table of contents
Unlike discrete manufacturing, made to stock, or made to order — the Engineer-to-Order manufacturing industry faces a unique set of challenges. From complex product designing to close involvement with customers, each product is different in engineering to order.
Naturally, if you are manufacturing products with the engineering-to-order approach, you would always look at ways to procure the best material while keeping costs down, decreasing lead times, and ensuring smooth communication among the various stakeholders.
With decades of experience in the manufacturing industry, we have helped multiple global Engineer-to-Order manufacturers break free from working in silos. They all had one major issue in common – disconnected PLM and ERP systems leading to gaps and loss in critical data.
This article will share the challenges of Engineer-to-Order manufacturing companies and how a PLM and Microsoft Dynamics 365 ERP integration solution can help you address these challenges.
What is Engineer-to-Order?
Engineer-to-Order (ETO) is a type of manufacturing where product engineering begins only after an order is received. ETO companies build individual products designed to meet their customers' exact specifications.
Each product is exclusive, complex, and requires a unique set of item numbers, bill of materials (BOM), and routings. ETO is also known as project-based manufacturing or custom manufacturing.
What are the major challenges of Engineer-to-Order Manufacturers? And how can PLM and Microsoft Dynamics 365 ERP integration software solve these challenges?
1. Complex products with high participation of customers
The entire manufacturing process of the ETO industry revolves around the customer. The product’s research, designing, experiments, prototyping, and engineering are initiated only after receiving a customer order with detailed specifications.
Each product is carefully customized, requiring robust designing and meticulous engineering. Every phase throughout the product development – design, engineering, procurement, assembly, is shared with the customer for ‘approvals,’ making it a constant back and forth between the manufacturer and client.
Solution:
Integrating PLM and ERP means you can quickly share any information at the earlier stages of the development with all the teams involved and the customer. This enhances collaboration and shortens the product's time to market.
2. Coordinating with a diverse set of stakeholders
Multiple teams are deeply involved in manufacturing a single product from start to finish. The design teams work in the CAD systems, engineers operate in the PLM system, and the procurement, suppliers, and production teams work in the ERP system.
The procurement team receives the bill of materials based on the engineer's product concept and the customer's feedback, making interdepartmental communication critical to the product's success.
Solution:
Different teams operating in separate systems are connected through an engineer-to-order PLM and Microsoft Dynamics 365 software. This enables centralized data management, which ensures that people across various departments, divisions, and locations can work with relevant, accurate, and updated information.
3. Scattered product information due to siloed systems
Manufacturing an ETO product involves significant engineering and design for each order, with loads of technical and operational information flow. You have to gather plenty of data related to different aspects of BOMs, drawings, product engineering, technical specifications, packaging, etc.
When your product data is spread across multiple systems, you have islands of data, resulting in delayed communication and data loss, with no proper documentation. For instance, the engineers must have access to all the relevant information related to the product once the order is confirmed. However, data stored in multiple systems causes a lengthier pre-proposal design work.
Solution:
Integrated PLM and Dynamics 365 ERP offer one source of truth with which departments can share data in near real-time. All the data related to your Engineer-to-Order products, such as versions, revisions, changes, or updates, are well documented and accounted for.
4. Longer lead times due to manual processes
Since every product has distinct characteristics, there is minimal scope for reusing knowledge. Each Engineer-to-Order product is highly complex and requires new variants of parts and designs with every order. There are different bills for each item, subpart, assembly, etc., to manufacture the product.
Multiple teams are operating in several systems, executing processes manually, meaning each piece of information is shared with a delay, and every activity, such as workflow approvals, takes more time.
Solution:
A PLM and Dynamics 365 ERP integration solution automates data import and product release processes. With automation, you save on the effort, time, and money spent on inspections, corrections, or damage repairs. It provides the relevant engineering and manufacturing teams access to reliable and up-to-date BOMs and other product data.
5. Ineffective change management leading to costly rework
The entire ETO process must be precisely planned as the products manufactured are complex. Several revisions may be required to finalize the engineering specifications of a customer. The ETO teams must share and request information with each other, track communications and design changes, and update quotes and estimates.
The change orders need continuous communication with the customer and internal departments with a high volume of data exchange, new action items, re-engineering, etc. If any change isn’t tracked accurately — it leads to additional expenses, rework, and further delay.
Solution:
Connected PLM and Microsoft Dynamics 365 ERP systems, ensure your ETO product data always stays updated based on the current version of the product. You have increased insight into product version updates during the numerous lifecycle stages of the product and have better control of costs and schedules.
6. Extensive product testing due to heavy customization
ETO-manufactured products undergo a higher level of testing and quality control. As the product is always manufactured for the first time, each has its unique lifecycle, and the testing cycles may go for more iterations.
The internal teams (engineers, buyers, production) test and validate the product after each phase based on the customer’s specifications. The product continues to the next stage of development only after the necessary approvals from the customer.
Solution:
You gain end-to-end visibility into the product status, changes, and supply chain, leveraging PLM and Dynamics 365 ERP integration. With streamlined communication and enhanced control of ETO products, the integration ensures data quality, making product testing smoother.
Do you need to integrate PLM and ERP as an Engineer-to-Order manufacturer?
Communication is key for Engineer-to-Order companies. Every person and department involved in the ETO process must have access to the necessary data.
If any piece of information is not shared correctly, or if any data is lost, it leads to missed orders, quality issues, mismanaging client expectations, and mistakes in the finished product.
Engineer-to-order PLM and Microsoft Dynamics 365 ERP integration guarantees that all relevant stakeholders involved in the ETO process have access to the updated information in real time.
How can we help you get started with PLM and Microsoft Dynamics 365 ERP integration today?
As an Engineer-to-Order manufacturer, you will gain multiple benefits with a PLM and Microsoft Dynamics 365 ERP integration solution. If you are interested in an intuitive, easy-to-use integration solution, you could explore our PLM-ERP integration solution for Microsoft Dynamics 365.
We offer out-of-the-box PLM integrations for Siemens Teamcenter and PTC Windchill. Additionally, we provide PLM integrations with 3DX Dassault and a PLM integration framework that you can easily configure for other PLM, PDM, or CAD systems.
Explore more about our engineer-to-order PLM and ERP integration for Microsoft Dynamics 365 in this factsheet, which shares:
- What the integration solution can do for your business
- Benefits of PLM-ERP integration
- Features of a standard integration solution