FAQs about the Weighing and Dispensing Process in Pharmaceutical Industry
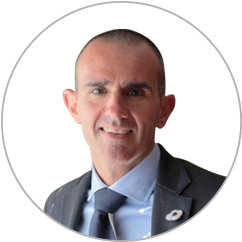
Table of contents
The Weighing and Dispensing process is a vital part of pharmaceutical manufacturing, as any inaccuracies can directly affect patient health and regulatory compliance. Additionally, accurate weighing and dispensing not only ensures product integrity but also contributes to cost savings by minimizing material waste.
One of the initial steps in the pharma production process, weighing and dispensing, lays the foundation for high-quality manufacturing practices, therefore, it is important to gain clarity and insights into the process. In this blog, we will address some of the most frequently asked questions about weighing and dispensing. We will also explore questions about the role of Enterprise Resource Planning (ERP) systems in streamlining these processes.
Q. What is the weighing and dispensing process in the pharmaceutical industry?
-
A. Weighing and dispensing in the pharmaceutical industry is a process of retrieving precise amounts of material from storage and preparing them to transfer to the production area.
Weighing and dispensing process is complex because each pharma formulation involves multiple components, each with its recipe and required quantities. It is critical to ensure that each ingredient is measured to its exact measurement and transferred to the correct batch for manufacturing. An accurate weighing and dispensing process ensures that finished products meet all specification requirements since the components consumed in production comply with the amount in the approved formula.
Q. What are the drawbacks of manual weighing and dispensing in pharmaceutical manufacturing?
-
A. Although the weighing and dispensing process is complex and critical, most of the companies still rely on manual processes to account for the quantities after scooping or pouring raw material and transferring them. This approach can have significant drawbacks that include:
-
Human Errors: Manual methods can introduce errors like misidentifying the materials, misreading the quantities required, or incorrect measurements, which can compromise the whole production process and quality.
-
Material Waste: The ingredients used in pharma manufacturing are high-risk, sensitive, expensive and controlled substances, therefore, excessive material dispensed due to inaccurate manual measurements translates into wastage and financial loss.
-
Limited Scalability: Manual processes are time-consuming and labor-intensive due to which scaling in response to increased demand becomes challenging.
-
Compliance Risk: Manual weighing and dispensing methods can contribute to errors and vulnerabilities that can compromise compliance with strict industry regulations and guidelines.
Q. What are the key pharmaceutical challenges that can be solved through an integrated weighing and dispensing system?
-
A. Manual weighing and dispensing have many challenges that can affect product quality. Integrating the process can help overcome these challenges as follows:
-
Quality Control: Integration ensures consistent accuracy in measurements in every batch. It can exercise tighter control over the formulations and eliminate the risk of human error thus enhancing the overall quality of the final product.
-
Inventory Reconciliation: Digitized weighing and dispensing solutions can track the inventory levels in real time. Additionally, once the material is dispensed for production, the inventory is updated automatically to mitigate the risk of stockouts and ensure uninterrupted production flow.
-
Cost Savings: By minimizing material waste through precise measurements and reducing the time spent on manual processes, integration can lead to significant cost savings. Improved operational efficiency can also enhance overall productivity, allowing companies to meet the market demands effectively.
-
Regulatory Compliance: Integrated systems are designed to support compliance with regulatory guidelines in the life sciences industry. They automate documentation and enhance traceability, making your company audit ready.
Q. How does an integrated Pharma ERP solution help in scale calibration for accurate weighing and dispensing in pharmaceutical manufacturing?
-
A. An integrated Pharma ERP solution can significantly enhance the efficiency and accuracy of scale calibration procedures in pharmaceutical manufacturing. Here are several ways in which it supports scale calibration:
-
Manage Scale Calibration Tests: An integrated Pharma ERP solution can automate the scheduling and management of calibration tests for weighing scales, ensuring they are performed consistently according to established protocols.
-
Set Up Calibration Frequency: The integrated system allows you to define and track the frequency of calibration for each scale, supporting efforts to maintain compliance with regulatory standards and helping ensure that equipment is calibrated at the appropriate intervals.
-
Manage Calibration Reports for Audits: An integrated Pharma ERP solution can generate and store comprehensive calibration reports, enhancing transparency and traceability, which makes it easy to produce documentation for audits.
-
The STAEDEAN Life Sciences Weighing & Dispensing interfaces with your scales to manage calibration and verification tasks that are designed to verify the accuracy of instruments used for weighing the materials. If you do not calibrate your scale when required, you will not be able to use it for your weighing operations. This ensures that only calibrated instruments are used to weigh components. You can manually create instrument control tasks when needed, or they can be automatically enforced by the system based on a configured frequency. Different calibration tests can be defined as part of the control task.
-
Written instructions and procedures can be set up for each calibration test to support the operator during its execution. It is also possible to implement a requirement for an electronic signature and a second-person verification to complete the check. Ultimately, you can print a report to maintain a record of all the calibrations and verification activities performed for each scale.
Q. What are the weighing methods used in pharmaceutical industry?
-
Weighing operations can be challenging for pharmaceutical manufacturers as it involves precisely measuring various products with different physical properties. How you execute your weighing operations will be based on your needs. Four different ways include:
-
Standing weighing: This is the most common approach to weighing quantity as a mass. An empty container is put on the scale to measure the tare, and then the product is poured into it to measure the gross weight. Tare management functionalities are usually available on scales to display the net weight instead of the gross weight so that operators can easily dose the missing quantity up to the target.
-
Counting pieces: This is the simplest way to measure the quantity of products required in manufacturing. This process applies to products that the operator can count quickly and accurately. For example, if manufacturing a product requires 10 bottles, the operator can simply count each bottle and declare the total number. However, counting pieces is recommended only for small amounts to minimize the risk of incorrect counting due to human errors.
-
Counting by weighing: When the amount to be counted goes beyond a few pieces, we need to use an alternative method for measuring the quantity, such as counting by weighing. Knowing the average weight of a unit, the operator can weigh the amount on the proper scale as a mass and get the counted units as a result. For example, production requires 30 bottles of an ingredient. If it is known that each bottle weighs, on average, 100 grams and there are 50 bottles in a pack, then the operator can put a full pack on the scale and remove bottles until the weight corresponds to the required number of bottles. Even though this process requires more time and effort than simply counting pieces, it provides more accurate results. When the amount to be counted goes beyond a few pieces, we need to use an alternative method for measuring the quantity, such as counting by weighing. Knowing the average weight of a unit, the operator can weigh the amount on the proper scale as a mass and get the counted units as a result. For example, production requires 30 bottles of an ingredient. If it is known that each bottle weighs, on average, 100 grams and there are 50 bottles in a pack, then the operator can put a full pack on the scale and remove bottles until the weight corresponds to the required number of bottles. Even though this process requires more time and effort than simply counting pieces, it provides more accurate results.
-
Weighing by difference – Weighing by difference method allows for the execution of the weighing operation by subtracting the quantity from a full container until the subtracted quantity reaches the target value. This is commonly required, especially for liquid components and solutions, which must be picked from the original container via syringes or pump.
Q. What are the factors that influence weighing accuracy in the pharmaceutical industry?
-
Weighing operations measure the ingredients required to be added to a manufacturing process. The weighing operation is executed by picking up the material from a container and placing it on a scale. The accuracy and efficiency of this process depends on the following factors:
-
Product type: Each product type has different characteristics, such as particle size distribution, bulk density, or material flowability, that must be considered. For example, the best practice for a powder product is not necessarily suitable for a liquid one. Carefully evaluating these physical properties will help you identify the right procedure.
-
Scale properties: To obtain correct results, it is essential to determine the proper scale to be used for weighing operations. For example, if you are weighing heavy products on a very sensitive scale, it will be difficult for the operator to position them correctly. Even worse, they might overload the pan, resulting in wrong measurements and, therefore, wrong production batches. The scale selected for the execution of the weighing operation must be able to measure the amount you need with the expected accuracy.
-
Required amount: The less time the weighing operation takes, the better it is for your production scheduling. If you want to minimize the amount of time an operator spends doing weighing operations, it is essential to train operators to evaluate the more convenient option to get the quantity weighed out.
Q. How does an integrated Pharma ERP solution solve weighing and dispensing challenges of the pharmaceutical manufacturing industry?
-
An integrated Pharma ERP solution is instrumental in addressing the challenges associated with weighing and dispensing in the pharmaceutical manufacturing industry. Here are a few challenges it tackles:
-
Inconsistent Quality: A Pharma ERP solution accurately identifies the correct ingredients required for each batch and ensures they are weighed and dispensed precisely. This precision is crucial for maintaining product quality and compliance with regulatory standards.
-
Low Throughput: By automating the weighing and dispensing processes, a Pharma ERP solution significantly improves the turnaround time for production. This automation allows manufacturers to operate more efficiently and meet production demands effectively.
-
High Operational Costs: Improved accuracy, minimized material waste, and reduced manual labor help in lowering operational costs. Streamlined processes and improved productivity with the help of an integrated Pharma ERP solution can boost the bottom line.
-
Inadequate Compliance: An integrated Pharma ERP solution offers robust documentation and traceability features that simplify compliance with regulatory requirements. Additionally, it includes advanced functionalities, such as second-person verification for critical weighing steps, further enhancing the reliability of the weighing and dispensing processes. An integrated Pharma ERP solution featuring a weighing and dispensing solution can be the key to success in today’s pharmaceutical manufacturing environment, where regulations are changing rapidly to meet ever-increasing demands.
Q. What are the benefits of using a weighing and dispensing solution embedded in Pharma ERP solution?
-
A Weighing and Dispensing system integrated with the ERP offers several benefits that enhance efficiency, accuracy, and compliance in the pharmaceutical industry. These benefits include:
-
Automatic Material Identification and Transfer: A pharma ERP solution identifies and matches the exact material required for production. Additionally, it also ensures that expired material is not qualified for weighing or production. Post weighing, the ERP solution also transfers material values and attributes from weighing scales directly into the ERP.
-
Instant Inventory Reconciliation: A pharma ERP solution streamlines inventory management by automatically reconciling the inventory stock levels and reducing the risk of stockouts.
-
Regulatory Compliance: A pharma ERP solution enables electronic signatures to support your compliance efforts with FDA 21 CFR Part 11 and EU GMP Annex 11. It also manages global and material-specific processing rules to help meet compliance with standard operating procedures
-
Streamlined Labeling: It reduces labeling errors by printing labels directly from the ERP system for a perfect match with product name, weight, and unit.
-
Improved Traceability: A pharma ERP solution maintains detailed records of raw materials, providing essential traceability information, including:
-
-
Product name and number
-
Date and time of weighing and dispensing operation
-
Location of weighing and dispensing operation
-
Dispensing operator
-
Unit weight
-
Dispensed quantity
-
STAEDEAN Life Sciences Weighing and Dispensing Solution
The STAEDEAN Life Sciences Weighing and Dispensing solution enables manufacturing operators to execute the weighing processes accurately. It assists in complying with Good Manufacturing Practices (GMP) by covering the most common weighing procedures—standard weighing, counting pieces, counting by weighing, and weighing by difference—as outlined above.
It is important to note that STAEDEAN is not limited to typical scenarios. Being oriented to the needs of the pharmaceutical industry, the software also offers a wide range of advanced features to cover pharmaceutical business scenarios such as the adjustment of the solution’s physical properties (e.g., pH adjustment), and the fill-up to the target volume.
Our solution is specifically designed and developed to meet the highest standards of accuracy, reliability, and safety, thus ensuring the quality of the product being manufactured, with benefits on the scrap rate, yield rates, and customer satisfaction.