3 Ways Equipment Rental Software Can Help You Plan Better
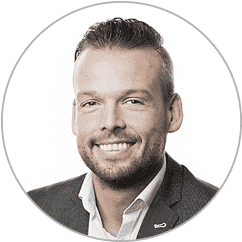
Table of contents
Planning of different tasks plays a crucial part in a well-oiled equipment rental process. A planning department requires the latest work order information continuously, allowing them to make changes “on the fly” and avoid any errors. Proper planning is essential to ensure efficiency and quality when carrying out tasks for your customers.
At STAEDEAN, we have learned a great deal from our equipment rental customers. One of their top concerns was inefficient planning that was costing them considerable time and money. Clearly, these businesses needed an efficient planning tool that would enable a smooth rental process. It equips your planning department with a complete overview of resources and equipment.
In this blog, we will cover how an equipment rental planning tool can help with various planning activities in a rental process.
Here are the different ways an equipment rental planning feature can benefit:
Resource planning
Every organization needs agendas to plan and coordinate work throughout the day. However, planning resources across your organization can be a full-time job. Not only does it involve a considerable amount of work, but you also need to look into different agendas of each employee, and plan accordingly.
By planning your resources well, you are finding the right worker for a particular job. This can be tricky and time-consuming without a good overview of all the work plans and the pending tasks.
A rental software with a planboard can give you visibility into every employee, their schedules, and the unfinished work details. Once you validate the types of tasks a particular resource is capable of performing, you reduce the risk of assigning a wrong employee for any given task.
Equipment maintenance
Equipment maintenance management is an essential aspect of the rental industry. However, you need to answer a bunch of questions before planning and executing the maintenance.
It is critical to know what needs to be done precisely and how you must do it. Then, you also need to consider which capabilities are required to execute the maintenance of the equipment. And, finally, you can determine the time of maintenance and the right resource who can perform the necessary tasks.
You can create different maintenance tasks for equipment by using various maintenance plans for particular products. A maintenance plan can be time-based, consumption-based, or a recall as follows:
- Time-based projects will trigger a maintenance task when a specific period has passed. For example, the equipment may need to be inspected every year. In such a case, the recurrence of the maintenance plan is set to “occurs once a year.”
- A consumption-based maintenance plan uses a meter on your equipment to indicate how much the equipment has been used. This can be at various rates: hours, days, kilometers, miles, etc. For example, after a car has been driven for 40,000 km, it is likely to need a tire change. Therefore, it is possible to set the maintenance plan for this car to 40,000 km.
- A recall maintenance plan can be created when the equipment is on-site with a customer, and for some reason, it needs to be returned. In this case, the maintenance plan contains a reason code which can be filled in, so that its recall purpose is clear. It is also possible to set the reset point to “on completion” or “when due.” This will determine when the next inspection needs to take place.
An ideal solution can help you manage the complete upkeep of your equipment. It allows you to distinguish tasks with particular capabilities. Then, it assigns work only to those resources whose capabilities match with a given task. This will prevent the possibility of allocating responsibility to someone who is not capable of performing it.
Task allocation
When creating a maintenance plan, you also need a work order template with tasks attached to it. These tasks can contain “task requirements.” On these task requirements, you can set up a specific capability that is needed to execute this task.
By setting up a capability for the task, you can create a validation between the task and the resource. To assign a task to an employee, he/she must have the necessary capabilities.
For example, when your equipment needs technical maintenance because a part broke, a mechanic is required. So, the task requirement for this maintenance task would be ‘mechanic’. This ensures the assigned worker can perform this task.
A rental solution with a planboard allows you to:
- Plan the day-to-day operations within your organization, giving you an entire overview of the planned and to-be-planned work for the internal and customers’ work
- View your employees’ daily agendas to monitor and record every movement
- Easily document and monitor your customers’ invoices
Altogether, this gives the planning department the ability to plan work at any given moment accurately.
Conclusion
Having an effective, all-rounded plan in place offers complete visibility into your rental equipment. It gives you the ability to move forward with a greater understanding of your entire rental process. Some of the key benefits are:
- Reduction in overall costs
- Optimum usage of your resources
- Maximum utilization of your rental equipment
- Increase in profits
- Decrease in time wasted
At STAEDEAN, we consider the out-of-the-box Service Planboard as one of the best additions over the years to our DynaRent Solutions Suite. It provides a graphical overview for your planning department to assign the right task(s) to your organization’s resources.
Interested to learn about how an equipment rental software with a planning tool can help your business? We are more than happy to discuss. Book a free demo today.