How to use ERP rental software to manage the maintenance of your equipment
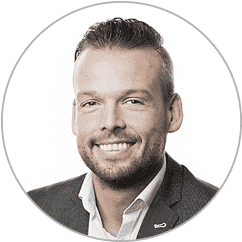
Table of contents
Equipment maintenance management is an important aspect in the rental industry. However, there are multiple questions that needed to be answered before planning and executing the maintenance. It’s critical to know what has to be done, how it needs to be done, and which capabilities are needed to execute the maintenance of the equipment. After that, it can be determined when the maintenance needs to be done and who can execute the tasks.
DynaRent can be used to manage the complete maintenance of your equipment. It allows you to create different tasks with particular capabilities, which only allows a specific resource with the same capabilities to execute that task. This will prevent the possibility of assigning a task to someone who is not able to perform it. Assigning a task to a resource can be done with the Service Planboard. The Service Planboard is a graphical overview where tasks can be planned and maintained. With the ability to set up the Planboard with your own preferences, it is easy to have an overview of your different tasks and resources.
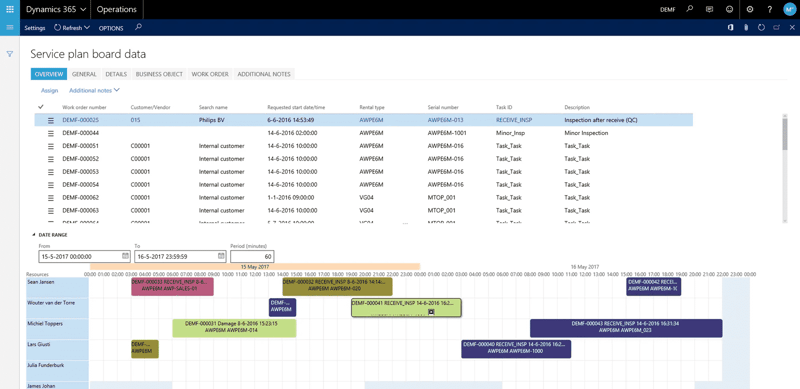
Image 1: Service Planboard with different tasks assigned to resources
Maintenance of equipment
With the use of maintenance plans for particular products, it is possible to create different maintenance tasks when using the equipment. A maintenance plan can be time-based, consumption-based, or a recall. Time-based plans will trigger a maintenance task when a specific time period has passed. For example, the equipment may need to be inspected every year. In that case, the recurrence of the maintenance plan is set to “occurs once a year.”
A consumption-based maintenance plan uses a meter on your equipment to indicate how much the equipment has been used. This can be in various rates: hours, days, kilometres, miles, etc. For example, after a car has been driven for 40,000 km, it likely needs a tire change. Therefore, it is possible to set the maintenance plan for this car to 40,000 km.
A recall maintenance plan can be created when the equipment is on-site with a customer and for some reason it needs to be returned. In this case, the maintenance plan contains a reason code which can be filled in, so it’s clear why it needs to be recalled. It is also possible to set the reset point to “on completion” or “when due.” This will determine when the next inspection needs to take place.
Tasks
When creating a maintenance plan, you also need a work order template with tasks attached to it. These tasks can have “task requirements.” On these task requirements, you can set up a specific capability that is needed to execute this task. DynaRent gives you the opportunity to setup a validation for the execution of tasks. By setting up a capability for the task, you can create a validation between the task and the resource. In order to plan a task with a specific capability on a resource, it is necessary for that resource to have the same capability.
For example, when your equipment needs technical maintenance because a part broke, a mechanic is needed. The task requirement on the maintenance task would be “mechanic,”. Image 2 shows how the mechanic capability is set up in the system. The resource has the same capability, as shown at the task requirements of the maintenance task, which allows this resource to perform this task.
Image 2: Resource with capability: mechanic
So, setting up the maintenance of your equipment can be done with three kinds of maintenance plans: time-based, consumption-based, and recall. Time-based plans will go into action after a specific time period. Consumption-based plans will be triggered using specific meters on your equipment. Recall occurs when your equipment needs to be returned for some reason. The planning of your maintenance can be done with DynaRent’s Service Planboard, and it is also possible to create a validation for which resource is able to execute which task. This can be done through the task requirements and the specific capabilities for the tasks and resources. This validation prevents the possibility that a task will be planned for a resource that is not capable of performing it.
Want to know more about maintenance plans, the Service Planboard, or capabilities for your resources and tasks? Download the fact sheet below or book a demofor a free demonstration.
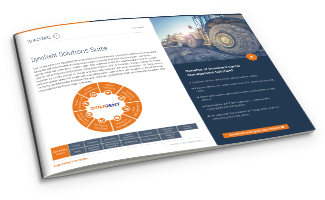