8 Signs a Manufacturing Business Should Integrate PLM and ERP
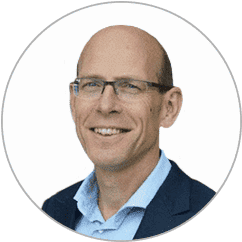
Table of contents
PLM and ERP are the brain and heart of any manufacturing company. Both are essential and equally important for all the business processes to occur smoothly.
Just like the brain and heart in your body, it is important that your business’s PLM and ERP systems are connected to ensure the proper movement of data. This ‘connection’ can be achieved through a PLM-ERP integration.
But how would you know when a PLM-ERP integration is necessary for your manufacturing enterprise?
With decades of experience working with various manufacturing industries, STAEDEAN has helped global enterprises integrate their PLM systems with Dynamics 365 ERP.
This article will share 8 clear signs that indicate you must integrate your PLM and ERP.
There’s an activity toward the end of this article to help you decide if a PLM-ERP integration is the right solution for you.
Why do you need to integrate PLM and ERP?
Manufacturing businesses depend on PLM and ERP systems for vital information needed to keep operations running smoothly. In such cases, connecting the two systems is essential when one system (ERP) relies on data from another system (PLM) to carry out critical activities.
Your manufacturing team depends on certain key information, such as the bill of materials (BOM) from the PLM system, to manufacture a product.
An integration solution allows the communication from the PLM to ERP to happen seamlessly while maintaining data quality and integrity. This improves collaboration and increases efficiency, reducing costs you’d otherwise incur in damage control.
Related Reading: Top 4 benefits of PLM-ERP integration |
What are the top 8 signs that indicate a need for PLM-ERP integration?
Sign 1: You are unable to create alignment among different departments
This is usually a result of several small information gaps and misalignments among various departments in your company. Since the design and engineering teams are only operating in the PLM system and the manufacturing, logistics, and distribution teams are only operating in the ERP system, there is no access to the product data overview.
All the teams work in silos with systems that do not talk to each other, impacting your teams’ communication.
With years of siloed data and functions, you struggle to have all your teams on the same page regarding any product information.
Sign 2: You are battling to keep up with your competition
Competition is an aspect every company must face and loves to stay ahead of. You could be in a situation where your competitors seem to do better than you, be it through reduced manufacturing costs, happier customers, or a higher profit margin.
But how did they get to this point? There is a good chance such manufacturing companies have integrated their PLM and ERP systems to ensure smooth operations.
Sign 3: You have a low first pass yield
You have a higher percentage of products that require some rework or corrective activity for the tested batch. Your first pass yield or throughput yield, which is a KPI demonstrating the quality and efficiency of your manufacturing process, is low.
This defective manufacturing could usually be due to inconsistencies in your overall process, making it less reliable.
All this rework results in longer lead times and poor bottom lines, ultimately taking a hit on your position and reputation in the market.
Sign 4: You incur repeated ad-hoc costs
With poorly aligned teams and a higher risk of defective manufacturing, you are bound to face some costs in fixing the process and products.
The defective products would have to undergo corrections and inspections, costing you double the time and money.
You are losing finances in either fixing the product, inspecting the product, or recalling the product. Not to mention the time you’ll waste in having long conversations with all the parties involved, such as your distributors, customers, and legal teams on why the product was of subpar quality or damaged.
Sign 5: You have an inconsistent supply chain
If you do not have a well-connected system in place, information gaps will develop due to manual data entry and maintaining multiple siloed systems.
If the manufacturing team has forgotten to send the list of parts required or has shared an older list due to incorrect data entry to the purchasing team, your entire production comes to a halt.
This supply shortage impacts your entire supply chain up to the end customer, who would likely be disgruntled to receive a late delivery.
There could also be cases where the BOM has been updated from its current version with the multiple iterations it goes through due to internal or external factors. If not communicated on time, this leads to incomplete, outdated, or incorrect product specifications for the purchasing team.
Sign 6: You do not have end-to-end visibility of your product journey
Designing, product engineering, manufacturing engineering, manufacturing operations, warehousing, and distributing are just some of the stages your product goes through before reaching the end customer.
However, with disconnected systems, you may not have a global view of your product data, which stage it is in, or a channel to quickly communicate product updates or changes — thereby increasing your response time.
You do not have access to real-time data changes or transfers, making it difficult to stay updated on the status of the product and make modifications if required.
For instance, you are notified that a particular product within your manufacturing product line has a defect. Without complete visibility into the data residing in the PLM and ERP systems, you would be unable to quickly trace the root cause and resolve the issue.
This impacts your planning around material sourcing, workforce capacity, and output forecasts — costing your products to be in rework, scraps, or waivers.
Sign 7: You cannot maintain data quality in PLM and ERP
Since essential data related to your product lies in different systems, you will have an additional and laborious effort in maintaining the quality and integrity of the data in all those systems.
With different data being entered manually by several teams with no standardized format, you have an increased scope of data errors.
Without an integration that could validate the data transfer from the PLM to the ERP, you are risking data changes that could remain undocumented. This further results in confusion among the engineering and manufacturing teams about the data ownership.
Needless to say, any impact on data quality could compromise product quality causing unmarketable products, or worse, liability claims from customers receiving products that don’t match their specifications.
Sign 8: You can barely spare time to innovate, research, and develop
When all your effort is going into putting out fires, there is very little time left to plan, innovate, and improve your product offerings.
Your employees’ time is injudiciously spent on repetitive data entries, checks, and coordination rather than focusing on product quality and innovation.
With limited ability to collaborate, your teams may be losing the vision to differentiate your products in the market, increasing your time to market and making it more challenging to reach your ideal customer profile.
Is a PLM-ERP integration the right solution for your business?
Here is a quick activity for you:
Count the number of signs you’ve noticed in your organization.
If you’ve answered ‘yes’ to 2 or fewer of the signs we’ve discussed above: Explore whether you first need to fix your internal processes and then look to integrate your PLM and ERP.
If you’ve answered ‘yes’ to 3 to 5 of the signs discussed above: Consider integrating your PLM and ERP systems at the earliest to improve business efficiency.
If you’ve answered ‘yes’ to more than 5 of the signs we’ve discussed above: Integrate your PLM and ERP systems without any delay to avoid losing any more money. Begin exploring the options you have for a PLM integration with ERP.
Here is a graphical overview of how manufacturers can win with PLM-ERP integration
(Click for a full view)
Ready to improve your manufacturing business’s efficiency today?
Now that you’ve seen the clear 8 signs that necessitate a PLM-ERP integration, you’ll be better positioned to decide whether it is the right solution for you.
Here are the next steps you could take:
1. Connect with your engineering and manufacturing teams to discuss the idea of a PLM-ERP integration
2. Analyze your PLM and ERP systems and look for software vendors that support integrations with your systems
3. Explore the various options you have for integrating your PLM and ERP systems, keeping in mind your time to market
If you are using Dynamics 365 ERP, then it could be worthwhile checking out the option of a standard PLM-ERP integration we offer. The standard integration is configurable, easy to use, with no coding hassles, and a quick implementation time.
However, if you think you would like some more information on PLM-ERP integration, or you are not on Dynamics 365 ERP, you could check out our comprehensive guide to PLM-ERP integration in the manufacturing industry.
This guide answers the following questions:
-
What are PLM and ERP with the differences?
-
Why must manufacturers integrate PLM and ERP?
-
What are the benefits of PLM-ERP integration?