PLM-ERP Integration for Dynamics 365: A Beginner's Guide to Technical Jargon
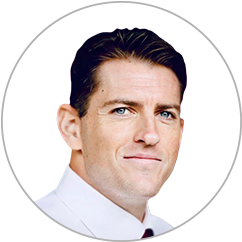
Table of contents
While discussing PLM-ERP integration, we as an Independent Software Vendor (ISV), and many others, tend to use ‘technical terms’ and ‘manufacturing jargon’ that’s common knowledge to only industry experts and technical teams. However, to accurately understand how the PLM-ERP integration works and benefits an organization, it’s crucial that every stakeholder involved is familiar with the most used terminology.
With a varied experience, we at STAEDEAN have helped global enterprises integrate their PLM systems with Dynamics 365 ERP, during which we’ve realized that these abbreviations, antonyms, and technical terms are used quite often and it’s always good to have them handy.
Although it may seem simple, this article is helpful for someone looking to brush up on the basics of PLM-ERP integration or anyone who isn’t involved in the technical side of your business. It’s our attempt to prevent you from ever having to rack your brains when researching or discussing PLM-ERP integration.
PLM and ERP: Back to basics
What is PLM?
A PLM system (Product Lifecycle Management) manages complex product development across all stages from ideation, designing, manufacturing, maintenance, and disposal. It is a software solution that has all your engineering information related to the product design and is more flexible. It integrates data, workflows, business systems, and people in a value chain to manage the entire lifecycle of a product efficiently and cost-effectively.
What is ERP?
The ERP (Enterprise Resource Planning) business system combines all the core processes of a company, such as HR, finance, procurement, manufacturing, services, supply chain, logistics, and shipping, into one system. However, modern ERP systems have evolved beyond the basics to offer efficiency, visibility, and intelligence across all your business aspects.
What is PLM-ERP integration?
A PLM-ERP integration helps connect the engineering and manufacturing worlds.
Manufacturing businesses depend on PLM and ERP systems for vital information to keep operations running smoothly. For instance, your manufacturing team depends on certain key information, such as the bill of materials (BOM), CAD data, routings, and product status from the PLM system to the ERP, to manufacture a product.
On the other hand, the engineering team could require certain data from the ERP system as well, such as logistical, vendor information, or pricing of the products. In such cases, connecting the two systems via integration is essential.
PLM-ERP integration allows the communication between PLM and ERP systems to happen seamlessly while maintaining data quality and integrity. This improves collaboration and increases efficiency, reducing costs you’d otherwise incur in damage control.
Commonly used terms during PLM-ERP integration for Dynamics 365
1. ECM: Engineering Change Management
Engineering change management is a process that provides a revision-controlled history of products throughout their lifecycle.
In Dynamics 365 F&SCM, ECM is a workflow-driven module that can manage different product versions in logistics and shipping. It controls and monitors product releases and enables traceability to track product attributes. This version and release control with centralized data ownership make the process of managing upgrades or changes in product data much easier.
ECM brings structure and discipline to the product data management process and enables products to be defined, released, and revised in a controlled manner, supported by workflows. With ECM, you can easily plan and manage product versioning, manage product lifecycles, and handle engineering changes.
2. ECR: Engineering Change Request
Engineering change request is used to request changes by any employee from any department within your company. It starts the process of making a change with discussions among the engineering team to assess the impact of the change and find the best potential solution.
Anyone can use an engineering change request to request a change, regardless of whether they are in the manufacturing, sourcing, warehouse, or sales departments. This update or change might be a recommendation for a new product, a problem you found while working on a product, a fix for an existing product, or something else entirely.
3. ECN: Engineering Change Notification
ECN is an organized form or document to communicate change in any product data, detailing the approved change to anyone who must know about the change. It authorizes the recipient to make changes to the design or process, such as purchasing new materials.
Playing a critical role in engineering and product development, it mentions what needs to be changed, the reasons for the change, when the changes must be made, and the necessary approvals to carry out the change.
4. ECO: Engineering Change Order
Engineering change orders provide a structured process for making changes to engineering products, wherein changes are proposed on the copy of the relevant data without affecting the master data. After the proposed changes, the ECO is sent through a workflow to the stakeholders, such as product owners, team leads, or finance managers, for the review and approval processes.
You can create an ECO based on an approved ECR or from scratch, including single or multiple products. The approval process can be automated as part of the workflow or as a manual step.
5. BOMs: Bill of Materials
Bill of materials is a centralized information source containing an extensive list of items required to create and manufacture a product, along with instructions to assemble and repair it. The format of a BOM is usually hierarchal, with the finished product at the top and the individual components and raw materials displayed at the bottom levels.
It can be referenced at various stages of a product’s lifecycle by different teams to ensure smooth production and plays a critical role in the manufacturing of any product. BOMs help you allocate resources and identify wasteful usage to develop more cost-effective products.
6. Attributes
Product attributes are objective and measurable properties that describe and characterize a product through user-defined fields. It provides information about the product specifications such as weight, height, dimensions, capacity, and so on.
In Dynamics 365 F&SCM, you can set default values for attributes. They can be associated with various entities, such as product categories and channels. When any product is associated with a product category or channel, it inherits the same attributes and default values.
7. Mapping
In Dynamics 365, mapping is a mechanism that allows data to be copied between corresponding records by linking one field to another, making it easier to manage extensive BOMs or product documents in your business. With mapping, you can specify a particular relationship between sets of records: one to many, many to one, or many to many, and directly copy the required data from one record to another.
There are certain rules that must be followed while mapping data: the fields must be of the same type and format and the length of the target field must be equal to or greater than the length of the source field.
Our PLM-ERP integration leverages this mapping capability to ensure data quality by validating that the data is correctly mapped to standard Dynamics 365 ERP, decreasing the need for manual interaction.
8. Routing
Routing is a detailed set of instructions describing how a particular item is created. It includes activities to be performed, the scheduling priorities, the machinery involved, and the hours required for the run times. It is the basis for scheduling and resource estimates, providing information on the required tooling, operator skills, inspections, testing, and so on.
There are planning routings and active routings. Planning routings are used for a potential manufacturing order, which is converted into an active routing after successful negotiations and is used to fill a manufacturing order.
9. Staging journal
Staging journals also known as staging tables within Dynamics 365, is the location where any data that comes from the PLM is first posted. In the staging journal, data is validated based on the business logic or rules and transformed before processing it. It displays the history of the previous information flow of any product and is used to analyze the accuracy of the product data or BOM before releasing it. It automatically approves and activates the bill of materials on the PLM status change.
10. XML: extensible markup language
XML is a markup language similar to HTML, where you define your tags according to your needs instead of using predefined tags.
We at STAEDEAN, use XML as one of the formats to carry out PLM-ERP integration as the fundamental format of XML is standardized. It is the file format the PLM system can export to and is used to integrate BOMs or product data.
11. Web services
A web service is a collection of open protocols and standards often used for exchanging data between systems or applications. It is a type of API (Application Programming Interface) that supports XML and offers quick communication within and across the organization. Loosely coupled with synchronous and asynchronous functionality, it supports remote procedure calls and document exchange.
12. T4EA
T4EA is the Teamcenter Gateway for enterprise applications by Siemens Teamcenter. T4EA adds the connector to other enterprise applications and ERP systems, based on different technologies such as file exchange, web services, database connectors, or messaging. It supports the transfer of data: parts, documents, changes, BOMs, and so on, from the Teamcenter PLM system to any other external system such as ERP.
We provide out-of-the-box PLM integrations for Siemens Teamcenter, with which you can integrate the following:
-
Part data
-
Revision data
-
Product structure data
-
Product URL
-
Attributes
-
PLM Status information
13. ERP connector
ERP connectors are middleware that integrates an ERP with any other system to facilitate data transfer. Some popular ERP connectors include Microsoft Dynamics 365 ERP Connector, Epicor P21 ERP Connector, and SAP ERP Connector.
However, in the specific context of PLM-ERP integration, ERP Connector is a component of PTC Windchill. It is used to leverage the current standard Windchill ESI capabilities on the Windchill side without using any third-party EAI (enterprise application integration) software.
We provide a ready-to-use PLM integration for PTC Windchill. Some of the data you can transfer from PTC Windchill to Dynamics 365 F&SCM with our standard integration solution are:
-
Part data
-
Revision data
-
Product status
-
Product structure data
-
Product documents
-
Change information
-
Attributes
-
ECO - ECN integration
We also have experience in PLM integrations with 3DX Dassault and any other PLM, PDM, or CAD system with a configurable PLM integration framework.
14. Released product
The products released to a specific legal entity (company) are known as released products. You can use the “released product” functionality in Dynamics 365 to control which legal entity is allowed to transact on that item, especially in cases where you have multiple legal entities such as distributors to sell your products.
The released product could have different attributes than the product itself. With ECM, you can decide how much of the product data you want to release to different departments or companies you’re dealing with.
You can release complete product structures in addition to releasing products together with their engineering versions, in a single release action. You could release products in bulk to one legal entity or many legal entities at a time.
Ready to streamline your processes with PLM-ERP integration for Dynamics 365?
If you’re interested in integrating your PLM system with Dynamics 365 ERP, you might be interested in exploring the PLM-ERP integrations we offer. We carry out in-person or remote implementations and our PLM-ERP integration solution is fully embedded in the Dynamics 365 environment.
You could explore our intuitive and easy-to-use PLM-ERP integration solution by checking out our factsheet.
This factsheet shares information on:
-
What the integration can do for your business
-
Benefits of PLM-ERP integration
-
Features of a standard integration