How Takt Time Helps You Avoid Waste and Optimize Production
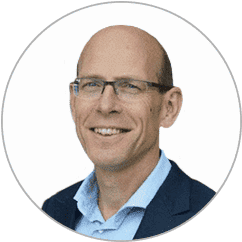
Table of contents
In lean thinking, takt time gives you a production rhythm that maintains an optimal, waste-free flow to satisfy customer demand. In some ways, takt time is a radical idea because it goes against the ingrained habit of producing above demand to protect against unforeseen circumstances. Many discrete manufacturers, even construction companies, implement takt time concepts to their advantage, managing projects at a different level of discipline and structure. STAEDEAN solutions support lean practice and takt time with the right levels of control and flexibility.
A Worst-Practice Experience: Everything but Lean
Early in my career, I was part of an episode that illustrates by means of a bad example why lean practices and takt time are a good idea. The company where I worked was getting ready to assemble a new product and had high hopes for its reception in the market. An aluminum component of this product was produced through extrusion, which was not within the company’s capabilities. We purchased the aluminum extrusion as a batch from a vendor. I had already made the order when somebody a couple of levels above mine instructed me to double it to make sure we would not run out of this crucial component.
Eventually, several tons of the aluminum extrusion arrived, taking up a larger-than-expected space in the facility. It was a great example of visual management in that we had to park it in a crossroad space which reminded us every day of how huge a blunder it was. We did not run out of this component, but, because the product did not make as big a splash as had been expected, we had far too much of it. Soon after the product launch, a redesign meant that the extrusion components on hand became useless.
Several years after I left that company, people were still trying to unload those aluminum parts, for which the company had paid at least $70,000. Eventually, they found somebody to re-smelt them, but they did not recoup their investment.
The company’s planning for the new product was off, and I was asked by “push oriented” sales planners to order parts for which there was no need, and much worse, no plan… no rhythm negotiated to govern a sensible “pull." Unfortunately, I have seen this sort of avoidable mishap in many companies.
Takt Time Sets a Sustainable Production Rhythm
Takt time, derived from the German word “Taktzeit,” which refers to a musical meter indicated by a metronome, offers a practical alternative. In lean thinking, takt time is defined as the net time available for work divided by customer demand. Or, more formally, work time per period divided by units required per period. Takt time gives you a steady beat to run production.
For example, if a bicycle maker’s demand is for 16 bicycles per day, that number would define the takt time for the production of bicycles and components. In an eight-hour day, takt time periods would be thirty minutes. The bicycle maker would organize the fabrication of components and the receiving of parts not made in-house to sync with the takt time. A good example in construction is the asphalt delivery to pave a road. A paver and traffic support for twenty loads per day will definitely waste loads 21 to 26 if shipped, or they will be recycled, but not laid down after they cool in the “pipeline."
From Just-In-Case to Just-In-Time
Just like lean as a whole, takt time goes against the legacy traditions in companies. Many manufacturers prefer to make and source components in batches and store them, expecting better economies of scale and improved efficiencies. However, my example and many other experiences in customer businesses demonstrate that this is risky. You tie up costs and resources in parts that you may never need, for products that might not ship, and flaws in these parts or their demand assumptions might not be noticed until too late in the process. The result is waste, the antithesis of lean practice. Takt time avoids waste by enabling a flow that aligns with actual demand. In many companies, takt time involves a cultural change, because people are used to working ahead to fill expected demand and want to be perceived as busy at all times.
Implementing takt time becomes more complicated when vendors are involved. That’s when companies negotiate just-in-time (JIT) delivery with trading partners, so they receive the right amount of parts or materials exactly when they need them. Business sometimes build a small buffer into takt time to allow for any possible process inefficiencies as they work toward lean operations. As processes become more productive, takt time can indicate a faster rhythm.
Expanding the Reach of Takt Time
Outside of discrete manufacturing, taking advantage of takt time is more challenging. In construction, for example, where most projects are unique, processes can be highly divergent. Construction companies try to operate more efficiently and practice lean principles by industrializing parts of the business. They shift the manufacturing of architectural and infrastructural components—imagine, if you will, walls, plumbing, joists, or pre-cast concrete segments—to a production facility where they can run in takt time. Assembly takes place at the construction site. Even so, the high specificity of construction projects requires a high level of expertise and intra-organizational trust to establish sensible takt time intervals. Subcontractor management adds further complexity.
ERP to Support Lean Practice and Takt Time
STAEDEAN supports lean production with takt time in several ways.
Flexible workflows. In STAEDEAN Advanced Discrete Manufacturing and the STAEDEAN Construction Solution, you can leverage the workflows your organization needs to validate project budgets and schedules to create buy-in for business processes that reflect takt time. In the STAEDEAN solutions as well as in Microsoft Dynamics AX, these workflows are highly adaptable, making it easier for manufacturers and construction companies to let people collaborate and make the timing of project elements a team commitment. Workflow design allows teams to prioritize and route projects for proper treatment, and accelerate lower-risk projects that require less intervention. They can fit projects closely into their business model as they generate estimates, conduct planning, gather approvals, define tasks and timelines, perform production, manage quality standards, and incorporate customer feedback or changing requirements. In projects, takt time may not have enough iterations to allow a narrow, quantitative error analysis, but people have the tools and resources to be accountable and use due care in making commitments.
Project templates. While construction and complex manufacturing projects may not repeat entirely, many of their elements are so similar that they can serve as the initial building blocks for new projects. Physical components and designs often echo past work, even if the final deliverables are unique. When you use the STAEDEAN solutions, you can save projects or sub-projects as templates and re-purpose them as needed, reusing the same work breakdown structure, bill-of-materials, and other project elements as starting points. With each use, you can refine the tasks involved to improve their efficiency and the quality of the result. When your team understands these templates, learning from experience becomes more pervasive and meaningful.
Task management. When you manage internal or subcontractor resources in manufacturing and construction projects by means of STAEDEAN software tools, you can insert buffers of time in specific tasks or groups of tasks to maintain a desirable pace that balances available resources with requirements. As your contributors and processes become more efficient, you can refine and move these buffers. The use of such cushions needs to be carefully monitored so you don’t inadvertently foster inefficiencies. In the newest versions of our solutions, enhancements in the task planning and task management capabilities will make it easier to maintain visibility in takt time flows.
I welcome your ideas and feedback. Drop me a message using the form below.