Maximize your efficiency with these 5 production management solutions
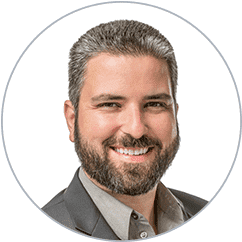
Table of contents
Manufacturing businesses always aim to operate as efficiently as possible, no matter whether they are heavy equipment manufacturers, engineer-to-order (ETO) companies, or mass-produce standardized products. What are the most important production management software capabilities that make unprecedented efficiency possible?
Here is a short list of the top-five, must-have manufacturing software elements you need when you make complex, high-value, ETO, or innovative products. If you produce anything like advanced machinery, specialized transportation systems, manufacturing robotics and controls, or state-of-the-art facilities systems – this is for you.
#1: Modern, connected ERP in the cloud
Your production management software should be an ERP system that supports your manufacturing processes and all your other business activities in one environment. Using traditional, specialized, stand-alone systems becomes too time- and resource-consuming to make sure everybody has the information they need, and processes bog down.
The easiest way to deploy contemporary ERP is in the cloud, where you can spin up capabilities and see the outcomes quickly. The cloud helps you avoid a lengthy deployment that can easily become unpredictable. Instead of having to budget for data center hardware and networking technologies, you can focus on functionality and processes that support your efficiencies and business metrics.
Today’s powerful, cloud-based ERP can provide much of what you need. If you integrate a manufacturing software suite, you can bridge almost all remaining capabilities gaps through efficient configuration instead of coding. Your data migrations and integrations are also much more efficient in the cloud.
#2: Closing the loop between production and engineering
Even innovative companies struggle with connecting manufacturing, powered by ERP, and engineering and product design, where teams commonly use a product lifecycle management (PLM) system. We still see workflows where employees have to manually duplicate and process information.
In this case, inefficiency can get expensive. Customer-requested changes are harder to implement and take longer to move into production, which may already be underway. Procurement of the right materials and parts may also take longer than necessary, and costs may balloon when deadlines must be met.
What’s most efficient is integrating your production management software with PLM systems, so you can enable a smooth, bidirectional flow of information. That’s the best way to avoid unproductive disruptions, give customers what they want, and get engineering updates to the production floor. Compound the efficiencies if your production plants and engineering teams are in different time zones or countries.
#3: Mobile enablement wherever possible
Companies are becoming more creative when it comes to using mobility, but most of them have barely begun to explore it. Think about all the formal and informal workplaces in your manufacturing organization – production areas, warehouses, vans, distributed and home offices, customer locations, vendor meeting rooms, coffee shops, parking areas, and so forth.
Then imagine what people – field service workers, sales associates, warehouse managers, production planners, maintenance managers, and others – need to do there and how it would be to their advantage to access software capabilities and data instantly.
In the cloud, you can provide easy, secure mobile access to ERP functionality and information. Enterprise mobility tools like STAEDEAN’s Dynamics Anywhere Mobility Studio make it easy to bring mobility to any business process. It’s too inefficient to require employees to find a computer elsewhere in the facility, travel to a company location, or ask somebody to retrieve data for them. What’s more, mobility is more than efficient – it can be truly transformative.
#4: Configure, price, quote (CPQ) functionality
Your production management software needs to support the configure, price, quote (CPQ) process that takes care of translating customer requirements into viable product configurations and puts a price tag on them.
You don’t want to replicate information manually, because it wastes time and generates errors. It’s in your customers’ best interests to implement a smooth path with reliable information, all the way from the first conversation to an approved quote and on to the engineering bill-of-material (EBOM) and the manufacturing bill-of-materials (MBOM).
A powerful CPQ module can help you make design and production more efficient as you standardize and reuse components and apply business rules to new product configurations. It can also improve the customer experience by allowing your sales associates to produce a viable, competitive quote within hours instead of weeks.
#5: Asset management and maintenance
Equipment downtime, poor performance, or substandard output is inefficient, both in your own production workflows and when it happens in customer operations. Your production management software should include asset management capabilities that give you the means to gather and process data from manufacturing equipment or machine products at customer sites and pinpoint any deviations from the up-time, quality, or performance levels you promise or maintain.
Armed with machine data insight, you can proactively repair or improve the operation of customers’ machine products or your own production equipment. If you perform proactive maintenance for customers, your revenue and customer retention can also grow. Usage data from customers’ machines can flow back to your engineers’ PLM system, so they can improve designs to make your products more competitive and valuable.
These manufacturing management software capabilities within a connected ERP environment are essential.
To learn more about accomplishing great efficiencies and other results with modern ERP, download our whitepaper .
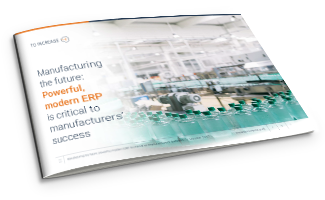