STAEDEAN Life Sciences Solution Helps Pharma Companies Comply with FDA ICH Q6A Specification Requirements
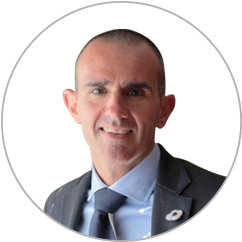
Table of contents
- Specifications are GMP-critical for product quality and patient safety, requiring pharma companies to set requirements efficiently and in compliance with regulatory guidelines.
According to the FDA guidance prepared under the auspices of the ICH in Q6A Specifications: Test Procedures and Acceptance Criteria for New Drug Substances and New Drug Products: Chemical Substances, specifications are important standards that are proposed and justified by manufacturers and sanctioned by regulatory authorities as conditions of approval.
The Importance of Drug Specifications and Tests
The FDA provides guidelines on the setting and justification of acceptance criteria and the selection of test procedures for new drug substances of synthetic chemical origin, and new drug products produced from them.
As defined by the European Medicines Agency, a specification is a list of tests, references to analytical procedures, and appropriate acceptance criteria, which are numerical limits, ranges, or other criteria for the tests described. It establishes the set of criteria to which a drug substance or drug product should conform to be considered acceptable for its intended use.
The specifications may relate to one or more physical, chemical, biological and/or microbiological aspects of the drug substance and/or drug product. Tests must be performed under the stated conditions on representative samples.
Specifications are GMP critical data, and they are vital for product quality and, in the case of pharmaceutical drug products, patient protection. It is essential for a pharmaceutical company to have an efficient and regulatory-compliant approach to setting requirements.
STAEDEAN Life Sciences Solution's Compliance Features for Specifications
Given the importance of specifications, the ERP system must be capable of reflecting and managing them in the most efficient and controlled way, while staying compliant with the regulations.
The STAEDEAN Life Sciences solution allows the management of test specification aspects, such as:
- Specifications versioning
- Approval workflow
- Internal specifications
Specifications Versioning
Specifications are constantly evolving. Particularly during the early stages of product development, firms have very limited knowledge and experience regarding the product.
As the manufacturer gains experience with the product formulation and the test methodology, changes in specifications may be necessary to ensure the methods are robust and capable of producing consistent and reliable analytical results. Changes in the product or its manufacturing process may further impact analytical testing.
Any changes in specifications shall be routed through a change control procedure and appropriate regulatory approval shall be sought before implementing the revised specifications.
With the STAEDEAN Life Sciences solution, you can create multiple versions of the same specification, each associated with a validity period. Using a certain specification version requires approval and activation during the current period. Obsolete specifications can be deactivated to avoid usage within the system.
This approach allows simplified management of specification changes while keeping track of the version history. Managing specification changes within the ERP system avoids paper-based management of different versions which requires more effort and is more susceptible to mistakes.
Approval Workflow
Acceptance criteria in regulated companies is crucial so the STAEDEAN Life Sciences solution requires specifications to be approved before they can be used in the system.
This approval is mandatory and can be secured via electronic signature to provide an additional level of control in compliance with 21 CFR part 11. To guarantee full traceability, the system records the approver’s name and the date and time of the approval.
The STAEDEAN Life Sciences solution also provides workflow functionality to ensure specifications are processed and approved consistently and efficiently. A workflow is a set of steps with predefined rules and conditions that will result in an automated process for approvals. The steps and conditions of the workflow can be configured in a flexible way to match companies’ requirements and business processes.
Internal Specifications
When defining test acceptance criteria, pharmaceutical companies may choose to have tighter in-house specifications at the time of release. This provides increased assurance to the applicant that the product will remain within the regulatory acceptance criteria throughout its shelf life.
In fact, from a regulatory perspective, the concept of different acceptance criteria for release vs. shelf-life specifications is applied to drug products only. Specifically, more restrictive criteria are applied for the release of a drug product than to the shelf life.
In the European Union, there is a regulatory requirement for distinct specifications for release and for shelf life to be different. Examples where this may be applicable include assay and impurity (degradation product) levels.
The STAEDEAN Life Sciences solution includes the ability to define two different levels of acceptance criteria for each test—internal and external specifications. Test results are checked against both specifications.
Learn More About STAEDEAN
STAEDEAN Life Sciences solution is a complete, cloud-based ERP solution for Life Sciences powered by the Microsoft Dynamics 365 platform. With our industry solutions and expertise, we help biotech, pharmaceutical, and medical device manufacturers optimize processes and meet complex regulatory compliance with ease.