Digital Quality Control Systems/Laboratory Information Management Systems (LIMS) and the Evolution of CDMOs
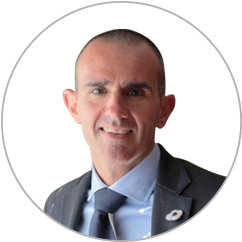
Developers of sophisticated new biologics want their CDMOs to have the most sophisticated quality management tools.
In response to the burgeoning market for biologics, Contract Development Manufacturing Organizations (CDMOs) are increasingly adopting Laboratory Information Management Systems (LIMS) as a vital part of their operational strategies. This blog post will delve into the trend, explore the importance of Laboratory Information Management Systems, and identify ways in which they enable CDMOs to thrive in a highly competitive marketplace.
Because executives at many Biotech and Biopharma organizations work on groundbreaking Advanced Therapy Medicinal Products (ATMPs) based on genes, tissues, and cells, they rely on manufacturing partners that have a more modern mindset. Creating ATMPs requires a high level of expertise and sophisticated facility capabilities—airlocking, decontamination, deep freezing, etc.—and it’s a bit of a disconnect if a CDMO is using cumbersome paper-based systems, manual workflows, and inaccurate methods of data collection to support these cutting-edge competencies.
Emerging CDMOs that come out of the gate with digital quality control system/LIMS have been charting the path towards industry-wide transformation, pressuring larger manufacturers that may have been more legacy minded to adopt advanced quality control systems themselves. CDMOs with a strong focus on digital technologies around data analytics and quality are better positioned to collaborate with Biotech firms seeking optimized processes, improved efficiency, and real-time insights.
What’s more, since the regulatory landscape for ATMPs is complex and continually evolving, compliance experts at Biotech organizations want CDMOs that can help them ensure compliance and streamline the path towards commercialization. With a digital quality control system in place, CDMOs can provide better service to all their customers in the following ways:
1. Enhanced Efficiency and Streamlined Operations
A LIMS enables CDMOs to streamline their operations and enhance efficiency throughout the production lifecycle. This is especially important for ATMP manufacturing, which requires a high degree of precision and accuracy. By replacing paper-based workflows with digital solutions, manual entry errors are reduced, documentation is more easily accessible, and collaboration among stakeholders is accelerated. Digital transformation not only improves internal processes but also enhances client and partner interactions by providing real-time access to quality data, fostering transparency and facilitating faster decision-making.
2. Compliance with Stringent Regulatory Standards
Laboratory Information Management Systems offer robust tools to maintain regulatory compliance by automating documentation, enabling real-time data tracking and analysis, facilitating audit readiness, and ensuring a complete and consistent record of compliance activities.
3. Data-Driven Decision Making
LIMS empower CDMOs to make data-driven decisions, via real-time visibility into Key Performance Indicators (KPIs) and quality metrics. Stakeholders can rapidly collect, analyze, and report on vast amounts of quality data, enabling them to identify trends, patterns, and areas for improvement. This data-driven approach enhances overall product quality, reduces errors, and helps CDMOs identify exciting ways to add value to client partnerships.
4. Better Collaboration and Greater Transparency
Effective collaboration between CDMOs, clients, and partners is paramount to success in the biologics contract manufacturing market. Leveraging digital quality control systems allows for seamless collaboration, irrespective of geographical boundaries. CDMOs can securely share real-time quality data with clients, enabling them to monitor and track the manufacturing process. This transparency builds trust, strengthens relationships, and facilitates a faster response to emerging issues or potential risks. Additionally, these systems provide a central repository for documentation and deliver seamless communication, ensuring that all stakeholders are aligned and well-informed.
5. Traceability
Digital quality control systems enable automatic material tracking and tracing, making it easier to identify and address any issues or deviations that may arise during manufacturing.
6. Scalability
ATMP manufacturing is a rapidly evolving field, with constantly changing requirements and technologies. Digital quality control systems provide the flexibility and scalability needed to adapt to industry trends and regulatory changes. They also allow for easy integration with other digital systems and technologies, facilitating continuous improvement and innovation.
Choose a LIMS / Advanced Quality Management System That’s Purpose-Built for Life Sciences
At STAEDEAN, our mission is to give Life Sciences organizations the advanced technology they need for tackling the operational challenges and regulatory changes they face every day. As leaders in the discipline of business process engineering and improvement, we’ve become a trusted partner for leading CDMOs in the U.S., Europe, and Australia.
Our comprehensive, scalable STAEDEAN Life Sciences Enterprise Resource Planning (ERP) solution is embedded into Microsoft Dynamics 365 and delivers easy-to-implement modules that cover every aspect of your business, from quality control and supply chain to weighing and dispensing.
The STAEDEAN Life Sciences Quality Management solution goes beyond laboratory processes to streamline and automate planning, ordering, sampling, production scheduling, acceptance criteria, certificates of analysis/conformance, stability studies, approval workflows, and more. We give you everything you need to integrate operations across your divisions and departments.
The LIMS component of STAEDEAN Life Sciences Quality Management delivers visibility into every aspect of laboratory operations and provides unparalleled digital accuracy, data analytics, assurance metrics, and rules-based decision support.
Through real-time communication and visibility throughout your operations, our integrated digital quality control solution helps ensure product excellence and cost control—plus GxP and regulatory compliance—at a fraction of the cost you’d expect. With STAEDEAN Life Sciences Quality Management in place, you’ll be able to:
-
Ensure accurate monitoring
-
Maintain data integrity from a single source of truth
-
Comply with FDA 21 CFR Part 11, EU Annex 11, country-specific regulations, and other industry standards
-
Improve accuracy and streamline validation with automated, digital process optimization
Don’t Get Left Behind—Go Digital Now!
As the biologics contract manufacturing market continues to grow, CDMOs need to embrace digital technologies to remain competitive and deliver innovative manufacturing services. By adopting cloud-based, digital quality systems, CDMOs can optimize operations, foster collaboration, and position themselves as industry leaders in the era of advanced drug manufacturing.
The time to eliminate manual, paper-based processes and take your productivity to the next level is now.