What are the Data Governance Challenges in Manufacturing?
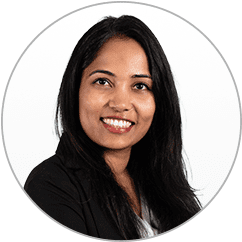
Table of contents
In the manufacturing industry, coordination between different systems and team members plays a crucial role in the smooth functioning of the production process. And data governance can play a vital role in the success of manufacturing organizations. However, the 2021 study by Weforum and Boston Consulting Group, revealed that only 39% out of 1300 manufacturing executives interviewed for the report had successfully scaled data-driven use cases beyond the production process of a single product.
This is not surprising! As seen in several other industries, manufacturing organizations manage multiple systems which could include legacy systems that might be disconnected. Each of these systems performs a specific function generating different types of data using different data nomenclature. So, you have volumes of unconnected and ungoverned data which only adds to the complexity of the situation and makes it difficult to make data-driven decisions.
At STAEDEAN, we build solutions for Microsoft-based ERPs and understand the domino effect of challenges due to poor data quality in the ERP. We have built solutions that can help our customers manage data workflows, master data, data quality, integration, migration, analytics, and security and compliance in Microsoft Dynamics 365 Finance & Supply Chain Management ERP. And therefore, in this blog, we will focus on some of the major data governance challenges in D365 for the manufacturing industry, and how our solutions can help solve those.
What are the data challenges that the manufacturing industry faces?
Below we list some of the general data management challenges often seen in manufacturing organizations.
1) Data Quality
Discrepancies or errors in design specifications or material requirements can negatively impact the production process. Coordination between team members and business systems requires integration and validation of data.
2) Master Data Management (MDM)
Master data management or MDM acts as a central repository for key master data, ensuring consistency and secure distribution of data across the organization in a controlled way is crucial for the success of manufacturing organizations. Organizations may choose to manage MDM within their ERP and PLM systems or by adopting an external system depending on their business requirements.
3) Data validation and lack of coordination
Challenges can arise in data validation, especially if there are no data governance processes that mandate the need for validation of critical information across or in specific business systems. Additionally, if you have a global enterprise, coordination between team members can be tricky and frustrating if not streamlined using a data governance solution.
4) Data silos
Manufacturing organizations that use multiple systems including a Warehouse Management system, a PLM system, and an ERP system to name just a few. If these systems are not integrated, then you have islands of data riddled with errors as employees are manually transferring data between systems. Additionally, if a company is spread across regions, you might have the same company using different business systems for the same process in different regions with differing data structures.
5) Moving data from legacy systems
Older legacy systems used by manufacturing organizations might need complex integrations and may be difficult to connect with other cloud-based solutions such as a new ERP or a master data management solution.
6) Massive data volume
On average, manufacturing organizations churn out copious amounts of data from generated sensors, machines, production lines, and supply chain activities which are in different formats. Additionally, data could come in from suppliers, logistics, third-party logistics, and so on. Classifying and managing this data and then deriving business insights from it can be a time-consuming and difficult task.
7) Ensuring compliance
Across manufacturing whether it is food or healthcare, there are strict rules and regulations that organizations have to adhere to. Protecting customer information and also ensuring data privacy and security while maintaining compliance can be a challenge.
8) Predictive maintenance
Predictive maintenance ties in very closely with analytics and business intelligence. If done accurately it can reduce costs and also help predict equipment failures in advance.
Two of the main systems housing data for manufacturing organizations are the Product Lifecycle Management System (PLM) and the Enterprise Resource Planning system (ERP). Having clean data in both these systems is crucial as they serve as the backbone of efficient product development and manufacturing, enabling organizations to bring innovative products to the market while optimizing operations and resources. Data usually flows from the PLM system to the ERP system and if that data is not complete, accurate, validated, and consistent, you cannot guarantee success in business processes that are driven by the ERP. Let’s understand the journey of data between PLM and ERP systems.
The data journey from PLM to ERP
The process begins with the Research and Development (R&D) team, which conceptualizes new products and extensively uses the PLM system to feed data on the multiple iterations of the product before this data can move to the ERP. The R&D team collaborates to determine factors like materials, design specifications, and performance goals with various teams including production and sales.
Next comes design and engineering. The design phase involves Computer-Aided Design (CAD) and Computer-Aided Manufacturing (CAM) software. However, the PLM system's role doesn't end here. It extends to include a Product Lifecycle Management perspective, facilitating communication with other teams. Once the design for the product is finalized, that data flows into the ERP system.
If the ERP is integrated with the PLM and other systems, then this data flow will be seamless and without manual errors. An integration solution can help you connect your ERP, PLM, and other systems and ensure that you have a holistic view of data. It is possible that team members who have access to the ERP system might not have access to the PLM or other systems, so an integrated view of data with limited access can be helpful, especially for the Product or Supply Chain Managers. The ERP focuses primarily on production, sales, and finance, ensuring the product's execution is successful. Therefore, it is essential the data in the ERP is accurate, completed, has certain conditions, is validated, and is secure.
It is important to have data governance in both the PLM and ERP systems to derive value from the data for manufacturing organizations. You should evaluate techniques to maintain clean and accurate data in both these systems. Implementing a data governance solution for each of these systems could be one way of solving the issues of poor data quality, or implementing an external master data management system could be another alternative solution. However, the external MDM system will not be able to perform data cleansing in each of the systems and you will have an additional system to manage in addition to your existing business systems and applications.
Let’s look at an example to follow the data lifecycle for a car manufacturing process to better understand the data flow in a manufacturing organization. Picture the research and development (R&D) team is based in Europe. Let’s assume that the production facilities exist in India and Japan and that they want to provide conditions for alternate materials to meet availability and market demand. They want to be able to provide these conditions in the ERP. Since the materials suggested locally are different, these materials need to be approved by the Engineering Manager, and then the Supply Chain Manager before this data is sent to the Production Manager. If there was a data governance solution in the ERP to manage this process, it would simplify and automate this process for a product record ensuring the successful journey from conceptualization to production. Additionally, a workflow will help since the ERP has more fields and different naming structures, so the responsible data owners can fill in crucial fields assigned to them in the workflow or approve data. And data quality rules can ensure that the data entered is accurate and consistent. Once that data is filled in and approved it can be securely distributed using a master data management solution.
The master data for this company is centrally managed from Europe since the R&D team is based in Germany. So, they distribute the master data to other organizations where they can utilize the information. Some team members from the local companies can be given editing rights for certain fields such as product material, which can trigger a workflow for approval when changed. Using our Data Governance Solution embedded within Dynamics 365 F&SCM, you can add data quality rules, data workflows, and also manage master data distribution and successfully manage this scenario and several other use cases and challenges.
Are there any data challenges specific to manufacturing in Dynamics 365 ERP?
Dynamics 365 ERP systems can present specific data quality, data entry, data distribution, data integration, and master data management challenges and use cases within the context of the manufacturing industry. Below are some of those challenges that can cause issues across processes.
- Data entry with mistakes and a lack of validation can lead to production delays and inaccurate inventory records.
- Without rules for duplicate entries, there could be duplicate records for products, materials, or suppliers that can be confusing and cause delays for the procurement, production, and reporting teams in carrying out their tasks.
- Missing data fields can make production planning and reporting difficult.
- If the data quality for products doesn’t include attributes, variants, and descriptions, it could hinder demand forecasting, production planning, and inventory management.
- Ensuring accurate information about suppliers, lead times, and pricing is important for procurement and supplier management.
- Managing accurate inventory data across multiple locations, tracking stock levels, and ensuring data is up to date can be difficult.
- Managing complex BOMs (bills of materials) with multiple levels and components, ensuring accuracy, and updating them as products evolve is a challenge without integrations with other systems such as the PLM system.
Our Data Governance Solution can help you resolve the above challenges in Dynamics 365 F&SCM using configurations, simplifying, and streamlining business processes for your organization.
Are you considering a data governance solution for your organization?
Implementing a data governance software can help you drive value from your data to derive a single source of truth. If you are considering a solution that can improve data quality, data workflows, and master data management for Microsoft Dynamics 365 Finance & Supply Chain Management, then STAEDEAN’s Data Governance Solution is worth considering. Our solution can integrate with any business system, perform data migrations into Dynamics 365, help you enrich imported data, and provide a holistic picture of your business data.
Using our solution, you can connect Dynamics 365 with any business application, perform data migrations into D365, prepare and extract data for analytics, create data entry workflows, improve data quality, and manage master data to ensure the data that reaches production is accurate and validated. Our Data Governance Solution can help you improve collaboration, streamline business processes, and control master data distribution in D365 F&SCM.
If you are keen to understand our solution better, we recommend downloading our Data Governance Solution factsheet from the link below.