How to structure and monitor your bulk rental equipment
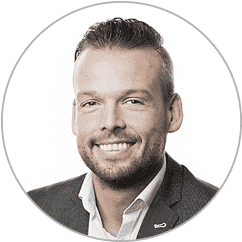
Table of contents
Every company within the equipment industry works with two categories of equipment. They work with serialized equipment and non-serialized equipment, this is also called bulk equipment.
The advantages of serialized equipment are, of course, that the equipment is uniquely identifiable. This makes it much easier to keep track of equipment, especially for transport or maintenance and service.
Financial departments can also gather information about serialized equipment easily, for example about a specific piece of equipment or its rental history. Bulk equipment does not have these advantages for several reasons. The high volume can make it almost impossible to serialize everything. It takes up a lot of manpower, so reducing costs can also be a reason to keep the equipment not serialized.
And if there’s no obligation to track equipment separately, why should you waste your money and manpower? This does not mean that there are no requirements regarding bulk equipment. It is also rented out. So, there must be a system that keeps track of your equipment. How else do you know which equipment needs service or transport?
How can you monitor your bulk equipment within your company?
Every company has different needs regarding the financial aspects of bulk equipment. There are many different options you can choose from:
- When purchased directly take bulk equipment as costs;
- When purchased, activate as fixed assets;
- Do a combination of both depending on the items;
Bulk equipment often involves enormous volumes that you need to handle within an equipment rental company. It is a daily challenge to monitor every piece of equipment logistically and financially, since there are no unique labels. Consequently, daily business process steps such as picking, packing, and prepping your depot, transportation, and return logistics, including quality inspection, are of the utmost importance.
Equipment rental software gives you great flexibility for monitoring bulk equipment. It lets you configure per equipment how you want to monitor this equipment financially. You can decide to create a fixed asset with multiple child assets, enabling complete financial monitoring and depreciation for all pieces of equipment.
Some of the important bulk rental processes for high volume products are:
- Availability overview (per depot/region)
- Rental
- Sub-rental
- In-house logistics
- Transportation
- Service and maintenance
- Return quality inspection
Below is an example of a multi-depot graphical bulk equipment overview in DynaRent for Microsoft Dynamics 365 for Finance and Operations.
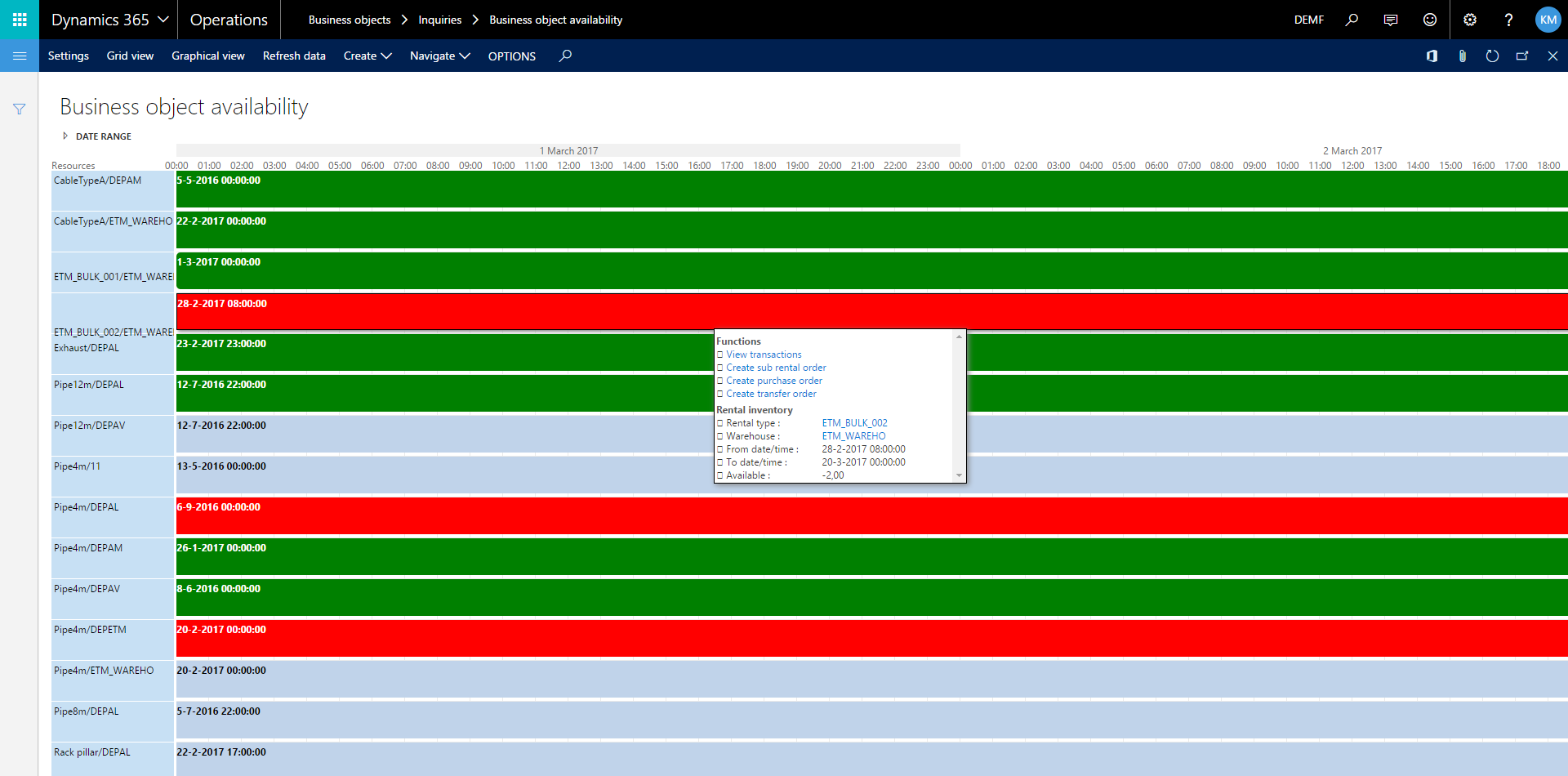
Image 1: Overview of bulk equipment rental in Dynamics 365 for Finance and Operations
From this screen, you can easily create rentals, and you can also take replenished actions for your bulk equipment rental:
- Purchasing - purchase equipment
- Sub-rental - temporary sub-rent equipment
- Internal movements - move equipment from one depot to another
During return, it is important to perform a quality inspection of the high-volume bulk equipment. Therefore, you can register different inspection options using this feature, including:
- Good quality - Stock will become available in your inventory.
- Damaged - Generates repair work orders.
- Lost - Generates a financial loss journal entry.
- Scrapped - Generates a financial scrap journal entry.
- Surplus - Increases inventory.
Finally, as you can see, depending on the registration, automatic actions will be created. This can easily be configured to your own needs to make sure the follow-up actions are done accordingly.
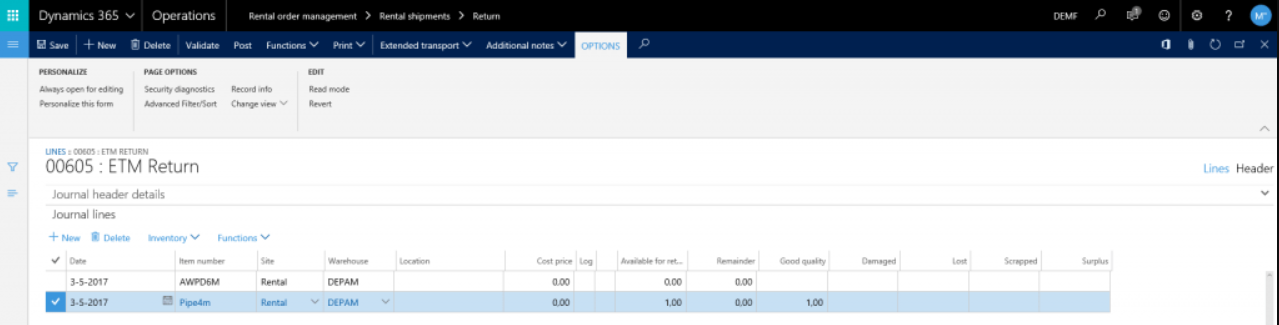
Image 2: Overview of bulk equipment rental in Dynamics 365 for Finance and Operations
Curious to learn more about what features to look for in equipment rental software? Download the tipsheet below.