Maintenance: the heartbeat of equipment asset management
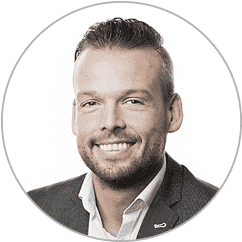
Table of contents
Equipment asset management—specifically, maintenance—is quite literally what gives your company a lifecycle to profit from. And maintenance is complex. To start, consider the many types of equipment a single company owns. What they rent to others, or perhaps provide service for as a third party. Different types of equipment, different usage scenarios, and different customer needs lead to a wide range of maintenance requirements.
In turn, different types of maintenance, from periodic maintenance to corrective maintenance, carries its own set of demands. Just at a high level, you need to consider many different categories. It ranges from:
- obligatory yearly inspection
- maintenance based on usage
- pre- and post-delivery inspection, emergency repairs
- routine but regular performance checks
- And much more
Since a single equipment type might involve multiple maintenance scenarios within a lifecycle. So you’re dealing with a dense matrix of needs.
A few equipment asset management examples:
- For equipment that will require spare parts replacement, you need accurate records and forecasting. This is the only way you can determine what you need. For example, which spare parts are needed? what resources are required to replace them? and of course the timing for both. You’ll also need to coordinate availability. This is how you can ensure that parts are available before a job starts. Coordination is also needed to get them delivered to or picked up by your resources.
- If you work with complex equipment, it’s more than likely that you’ll need to be ready to verify that service engineers meet certification requirements. Such requirements can vary depending on region, equipment use scenario, and maintenance type. You need integrated equipment, customer, and resource records with agile search and flexible planning tools.
- Costs and invoicing for equipment maintenance are often not straightforward, especially for corrective maintenance on rentals. A customer might be responsible for a malfunction. In that case, you’d want the ability to bill the customer in part or full for maintenance. That involves smart analytics about equipment history and trends, configurable contracts, and strong links to ERP accounting.
- IOr what if you’re planning and executing maintenance for equipment that’s still under warranty? You need to know what specific procedures you need to follow to comply with warranty conditions. Again, you’ll want fully integrated records that cover all angles for equipment, resources, customers, maintenance types--flexible but bulletproof against errors!
What’s the key to coordinating a diverse range of equipment maintenance needs?
A service management solution that combines industry-specific functionality with full ERP and CRM integration. Innovative equipment asset management depends on your equipment maintenance strength and flexibility. In today’s market, you need automation and complete insight to realize profitable equipment lifecycles.