How to Manage Equipment Maintenance in STAEDEAN Rental Management in D365?
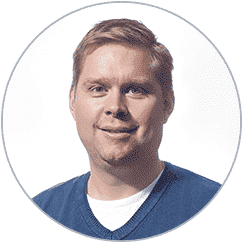
Table of contents
If you are in the business of renting out products, there is one thing that you dread more than anything else — downtime of assets causing a ripple effect, with delays impacting the entire rental lifecycle leading to revenue loss.
To avoid any operational disruptions, you need to know how to carry out maintenance within any rental management software options that you’re considering.
With over 19 years of deep expertise in the rental business, we can stand by one fact — all rental businesses, be it a rental depot, a manufacturer renting out, or a distributor handling rental equipment, must adopt maintenance as an integral part of their business.
But how does equipment maintenance actually work in our rental management software? In this article, you’ll discover how you can maintain your equipment in STAEDEAN Rental Management to maximize uptime.
What are the types of maintenance?
Depending on the circumstances, maintenance could be broadly classified into two types:
Scheduled maintenance: This is when the rental object’s maintenance is planned and undergoes preset-listed maintenance. It includes preventive, predictive, and routine maintenance.
Unscheduled maintenance: Here, the rental object requires unplanned maintenance that could result from asset breakdown or damage. It includes corrective, delayed, and emergency maintenance.
While maintenance is only done when a customer is not using a rental object, the need for maintenance could arise at any time due to unforeseeable conditions. Therefore, having a robust maintenance plan and a strong maintenance team would be helpful to ensure a smooth rental fleet.
Now that you’ve seen an overview of the maintenance process, let’s investigate how you can carry it out in our rental software.
How can you carry out maintenance within the STAEDEAN Rental Management solution?
The STAEDEAN Rental Management solution has a comprehensive work order system to carry out and manage all kinds of maintenance processes. A work order is an order related to the rental object that comprises all the tasks to be performed.
To understand how equipment maintenance works in STAEDEAN Rental Management, we will cover:
- Maintenance plans covered by STAEDEAN Rental Management
- Equipment maintenance tasks performed in STAEDEAN Rental Management
- Maintenance information provided by STAEDEAN Rental Management
- STAEDEAN Rental Management features supporting equipment maintenance
What are the maintenance plans covered in STAEDEAN Rental Management?
There are two maintenance plans the STAEDEAN Rental Management software solution provides:
1. Time-based maintenance: Here, the scheduled maintenance of the equipment is carried out after a particular period is over. It could be weekly, monthly, quarterly, or annually. For instance, calibration of an MRI machine every quarter or inspection of a forklift every year.
2. Consumption-based maintenance: Also known as usage-based maintenance, here the scheduled maintenance plan uses a meter on your equipment to indicate how much the equipment has been utilized. This rate could be in terms of hours of operation or miles of usage. For instance, routine oil change of a car after driving 3000 miles or replacing inverter batteries after 15000 operational hours.
These maintenance plans are preventive and routine scheduled plans. However, STAEDEAN Rental Management does not cover predictive maintenance plans. Maintenance plans could be directly created based on the service agreement and the type of rental object.
Unscheduled maintenance is also covered in STAEDEAN Rental Management depending on the type of repair a piece of equipment needs such as including corrective, delayed, or emergency maintenance. For such recalls, the maintenance point can be set to ‘on-completion’ or ‘when due’, so that the reason for the recall is clear.
Here you can see a screenshot of a maintenance work order within our software: (Click on the image for a full-screen view)
What kind of maintenance tasks can you perform in STAEDEAN Rental Management?
There are six main task types that can be performed in STAEDEAN Rental Management: service, transport, delivery, load, internal load, and internal delivery. You can perform several configurable maintenance tasks under the ‘services task type’ of STAEDEAN Rental Management. For instance, inspection and repair of a rented truck would be a configurable maintenance task under the service task type.
The maintenance tasks can be customized and entered in STAEDEAN Rental Management to carry out specific maintenance related to the rental equipment. Some of the maintenance tasks are:
- Inspection of the rental object
- Repair of damages
- Enhancements or updates
- Changing of spare parts
What information on maintenance can STAEDEAN Rental Management offer?
There are several elements around the planning and execution of maintaining rental equipment. All stakeholders involved must have readily accessible information on the what, who, and how of maintenance. STAEDEAN Rental Management can offer the following information regarding rental maintenance:
Time for maintenance: The forecasting feature in STAEDEAN Rental Management can give you an estimate for the amount of time required to carry out maintenance of any rental object end-to-end. You can also enter the actual time taken for maintenance, draw comparisons and improve processes for swift and effective maintenance.
Reliable spare parts forecast: STAEDEAN Rental Management can provide information on the spare parts needed to successfully carry out maintenance for any work order. This improves the first-time-right percentage and allows technicians to know the spare parts required before carrying out maintenance, preventing any time loss.
Expenses forecast: The rental software provides insights into the costs incurred on equipment maintenance. For instance, if a piece of equipment that needs corrective maintenance is in a different city from where the current technician is, the expenses would include travel fare, spare parts, tools needed, the time required, and maintenance team costs.
Maintenance histories: Since every product or equipment in the depot is connected to a work order, the entire history of maintenance done in the past can be seen. This is useful for maintenance done after a long time or when a new technician is assigned.
Maintenance insights: Upon using the software for maintenance, several insights can be drawn to optimize rental processes and maintenance plans in the future such as, selling or scraping a particular object, minimizing unplanned downtime, and identifying risks for maintenance.
Maintenance insights such as delayed, future, history, and checks displayed:
How can STAEDEAN Rental Management’s features improve the efficiency of rental equipment maintenance?
Single dashboard with overview: STAEDEAN Rental Management has a service plan board with an intuitive user interface that allows relevant users to see a graphical summary of each equipment work order comprehensively, resulting in efficient rental lifecycle management.
Here you can see a service plan board with a graphical overview:
Accurate task allocation: The work order can give the planner information on the availability and capability of technicians. This allows planners to assign tasks to technicians based on an open slot in their schedules and their ability to perform the maintenance.
Efficient work management: After being assigned a particular maintenance task, the field technician can log into the STAEDEAN Rental Management, and access detailed knowledge of the maintenance work orders that are open, assigned, and pending with the due dates, timelines, ready-reference material, and spare parts.
Task status updates: Planners and technicians can document and view how far the rental object is in the maintenance process with the dashboards and planning screens in STAEDEAN Rental Management. For instance, if a car requires a change of tires and the spare tires are yet to arrive in the workshop, the status could show 'awaiting spare parts'.
Here you can see a work order workspace for technicians and planners:
Real-time tracking: It is essential that the maintenance team knows the location of the rental object in use to carry out any unscheduled maintenance. The real-time tracking within STAEDEAN Rental Management offers this information, and you can immediately address any sudden need for maintenance.
Reminders and alerts: Whenever a piece of equipment is entered for maintenance work order, the system could be configured for the maintenance team to receive alerts in advance, even before a rental object’s maintenance is due. This can be done using the Standard Dynamics 365 F&SCM functionalities such as a business event and power automate, and alerts could be sent out via emails.
Maintenance quality checklist: After the equipment maintenance is completed, a technician is required to complete a task-based checklist to verify the grade of maintenance. This checklist comprises questions addressed to the technician to authenticate whether the due processes have been carried out or not. The checklist questions can be customized depending on the equipment so that each equipment can receive meticulous care.
Seamless communication: You can easily find the contact information of all the stakeholders associated with a particular rental object in the work order. This allows quick communication as multiple people could be involved in renting out a single piece of equipment. For instance, you can view the information of the primary contact person to communicate any breakdown or issue, the person registering the complaint, and the company utilizing the equipment.
Quickly accessible reference documents: Product manuals, maintenance guides, and instruction sheets could be uploaded or shared onto the software by experts, so technicians have all the required information in one location, accessible on their mobile devices as well.
Who would carry out equipment maintenance?
The team involved in maintenance depends on the size and complexity of each business. Typically, there would be a maintenance manager who oversees all the tasks, the maintenance task planner who would be handling the software, allocating tasks and work orders, a maintenance technician would be carrying out the maintenance and maintenance clerks who could support in administrative activities and logging information on hours of the task.
Can STAEDEAN Rental Management address your equipment maintenance needs?
STAEDEAN Rental Management is a comprehensive rental management software, which leverages all the capabilities of Dynamics 365 Finance & Supply Chain Management with embedded rental technology.
If you’re looking to streamline and enhance your business with Dynamics 365 as a platform, then STAEDEAN Rental Management could be a choice for you. Beyond maintenance, the solution covers each aspect of a rental object and much more.
You could explore more about the rental software we offer by booking a personalized demo. The demo could help answer your questions, such as:
- How STAEDEAN Rental Management supports equipment maintenance?
- What insights on equipment maintenance can you gain?
- Is the solution a good fit for your specific requirements?
After visualizing what the software can offer, you can evaluate the various options you have and determine if our solution is the right fit for you.