Why is Better Asset Management an Achievable Goal with ERP
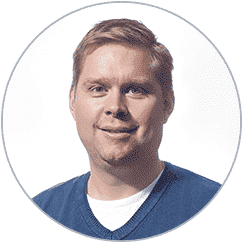
Table of contents
The Enterprise Asset Management (EAM) market size is expected to grow from USD 3.44 Billion in 2017 to USD 6.05 Billion by 2022, at a Compound Annual Growth Rate (CAGR) of 11.9%*. Despite the predicted growth rate, asset management or maintenance is perceived to be a costly affair in manufacturing businesses. Manufacturers are also wary of the fact that asset failure or asset downtime can cost them ten times the cost of planned maintenance resulting in production loss. There is also a belief amongst manufacturers that maintenance needs to be considered for all the existing assets. This is good for a maintenance-oriented company, but manufacturing businesses can also choose to start slowly and decide to start maintenance for the most critical processes and machines.
Manufacturing businesses can include asset management as a part of their ERP or can have separate asset management software. In the latter case, the challenge is a lot of integration that needs to be made where viewing cross-department data becomes a struggle. Whereas in the former case, if your maintenance is a part of your ERP, say on your Microsoft Dynamics system, no integration is required as it is a part of the same database. Maintenance can benefit other functions inside the ERP like inventory, procurement, HRM, etc. If spare parts are needed for maintenance, an integrated system can use the Material Requirement Planning (MRP) to plan procurement, stock availability, resulting in cost reduction and quicker repairs.
There are other elements in the maintenance systems like field tracking where it is very important to see historical data of maintenance work.
Maintenance software on an ERP solution can collate the data from the sensors attached to the assets and can enable a view of uptime/downtime through mobile access, streamlining the organization’s maintenance process. In summary, the system is helping organizations make smart decisions based on all those sensors. Now, imagine a huge chunk of data (big data) being collected by these sensors being used for predicting equipment failures even before they occur! It will be incomplete if we do not talk about IoT when talking about predictive asset management. [bctt tweet="The Internet of Things (IoT) is improving asset management practices radically. It pulls data from devices, machines, and equipment that enables deeper insight into operations. This, in turn, transforms a reactive approach into a proactive approach"] enabling decision makers to make quick and timely decisions.
Now, there are some manufacturers who make machines, which are not sold but are rented/leased to customers. In that scenario, rental asset management solutions along with appropriate asset management solutions, make sure that the machines at the customer sites keep running and therefore result in happy customers.
[bctt tweet="Overall, complete visibility and insights into availability and maintenance requirements for equipment is a wealth of information that can be used for the best decisions."] Add to that the spare parts planning and implement maintenance schedules accurately, that will result in minimizing downtime and costs.
If you want to manage diverse equipment service and resource needs with rich insights and automation or have additional questions on how your asset management solution can work seamlessly with your existing ERP, please fill the form below to get in touch with me.
Sources :
*Markets&Markets
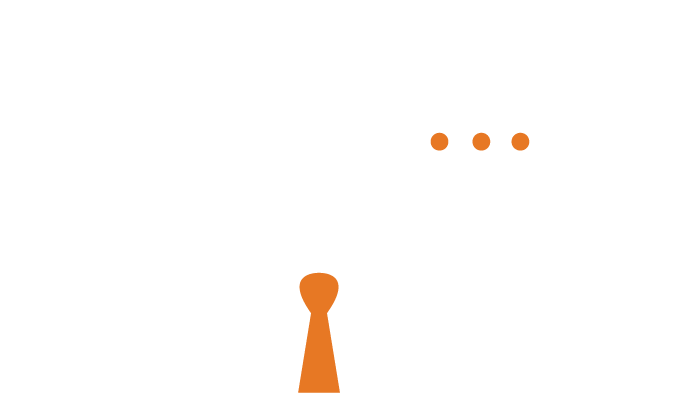