Time registration in Industrial Equipment Manufacturing
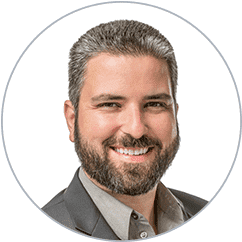
Table of contents
Two ways to handle time registration and invoicing of external resources in project-based manufacturing
Project-based manufacturers often outsource subcontracting work from a job to external workers or resources. In Industrial Equipment Manufacturing for Microsoft Dynamics NAV, you can follow two main scenarios to manage the time registration and invoicing of such external resources. The main difference between them is how time registration takes place, and the key question is whether or not an external resource registers time worked in a time sheet in Industrial Equipment Manufacturing. Understanding these two methods for managing the time registration and invoicing of external resources will help you work effectively in Industrial Equipment Manufacturing.
Time registration with a time sheet
The user is assigned a resource code which is connected to a user ID to provide access to Microsoft Dynamics NAV. You can grant the resource access as a limited user, who can navigate to the Resource Portal to register hours on a time sheet.
Time registration is handled in the same way as all other resources: The resource is planned on a resource planning line, from which assignments are created and maintained in the resource task. The resource task is selected in the time sheet that sets the process of registration, approval, and posting in motion. The time lines also post the resource planning lines, enabling project managers to follow progress.
However, the resource or the resource’s employer will send an invoice for the actual time. That needs to be matched with the time posted. A function in Industrial Equipment Manufacturing called Get External Resource Lines in the purchase invoice line makes this possible. By using this function, you can retrieve resource ledger entries of the type Usage as purchase invoice lines, thereby creating the purchase invoice detail. The retrieved entries are from those resources marked as Job Purchasing Resource and for which a vendor number is specified.
When posted, the purchase invoice creates resource ledger entries of the type Purchase. No postings are created in the job, because they were already made through the time registration system.
This time-sheet scenario implies that there is no direct link between time and invoice posting. Hours are posted to the job through the time registration system and costs are taken from the resource card. The vendor invoice is created based on the retrieved resource ledger entries with the same cost.
A recommendation: In this scenario, it is a best practice to create the invoice detail on behalf of the vendor. If you take that step, matching and posting the vendor-approved purchase invoice is a snap.
Time registration without a time sheet
This scenario bypasses the time registration system and is more closely connected to the actual invoicing. In this case, the external resource is not linked to a user ID and therefore cannot access Microsoft Dynamics NAV.
The resource is still being planned on the resource planning line. However, in this case a purchase order is created instead of an assignment to a resource task.
The external resource submits the hours worked to the back office, where resource planning lines can accordingly be posted. From this posting, you can print a payment certificate as an invitation to the vendor to create an appropriate purchase invoice.
With the vendor invoice, you can post as invoiced the purchase order created earlier. Industrial Equipment Manufacturing lets you link the purchase order line to a source, job, and ledger entry. When the purchase order is posted as invoiced, job ledger entries are updated accordingly to reflect the costs and quantities actually invoiced.
In this scenario, all related job ledger entries are updated with the new, average unit cost. Here is an example to show how it works:
On a job, 40 hours were purchased from an external resource. For these hours, three separate postings were made, resulting in three job ledger entries. Initially, the cost per hour was calculated as 50.60 per hour.
The invoices came in at three different rates. The average cost column shows the rate for each job ledger entry once the invoice is posted. For instance, after the posting of the final invoice each entry has a cost of 51.98.
Job Ledger entries |
Cost |
In-direct 10% |
|
Rate |
Avg Cost |
Calculation |
16 |
46,00 |
50,60 |
Invoice 1 |
45,00 |
49,50 |
(45,00+10%*16)/16 |
12 |
46,00 |
50,60 |
Invoice 2 |
47,50 |
50,67 |
(((45,00+10%)*16)+((47,50+10%)*12))/28 |
12 |
46,00 |
50,60 |
Invoice 3 |
50,00 |
51,98 |
(((45,00+10%)*16)+((47,50+10%)*12)+((50+10%)*12))/40 |
If you want to learn more, or see a demo of the time registration capability and other features in Industrial Equipment Manufacturing, please get in touch contact STAEDEAN.
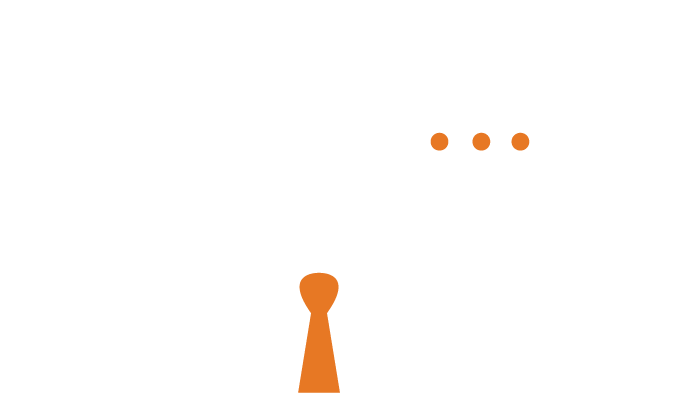