Requirements for Project-Based Operations in the Real-Time Enterprise
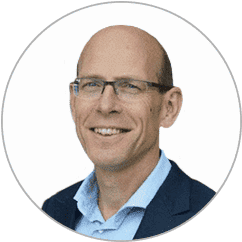
Table of contents
Shortening product lifecycles drive manufacturers to adopt project-based approaches to manufacturing and R&D. In real-time enterprises that respond immediately to changes in the competitive climate and customer needs, project-based operations offer the flexibility and control companies look for. For real-time enterprises to gain the value of project-based manufacturing and R&D, they need to right tools to control and manage their accelerating activities, or they might face unacceptable disruption and compromise the quality of their projects.
Real-time enterprises adopt project-based approaches to R&D and manufacturing
For decades already, manufacturers and analysts have observed ever shortening product lifecycles in industrial manufacturing. More recently, analysts began referring to average product lifecycle lengths of two to three years, with an increasing number of manufacturers’ products developed within those accelerated time-frames. At some point, short-lifecycle products generated fifty percent or more of most companies’ revenues, replacing offerings that generated a significant cash flow for five to ten years, or even longer.
Product lifecycles continue to shrink, prompting companies to adjust their strategies and operations. As real-time enterprises, they respond quickly to business climate changes, disruptive technologies, and emerging market needs. For many of them, that means bringing greater control and flexibility to manufacturing, the supply chain, and R&D, and widely adopting project-based and collaborative approaches. As you see in the 2014 report Global Manufacturing Outlook: Performance in the Crosshairs by KPMG, 88 percent of the business leaders interviewed said that the future of their innovation depended on partnerships as opposed to in-house initiatives.
Agility and insight needs in the real-time enterprise
When manufacturers become real-time enterprises, some of them newly adopt project-based manufacturing. Companies that already performed project-based manufacturing are evaluating their practices for greater nimbleness and speed, running more projects concurrently as well as in sequence. For many of them 3D printing becomes the preferred prototyping approach as they aim to reduce the time it takes to turn a design into a valuable product. In the supply chain, the project-based preference of real-time enterprises results in more short-term engagements, with more parties.
On the way to the real-time enterprise, manufacturers need software systems that enable the control and momentum they require. Common system requirements we hear include:
-
Tracking inventory per project and reallocating inventory to another project
-
Advanced, robust planning capabilities to plan and perform complex, concurrent projects profitably and within customers’ budgets
-
Effective tools to manage increasingly complex supply chains
In addition, the real-time enterprise needs to understand the earned value of its many projects. The ability to track and report on such important KPIs as ETC (estimate to completion), EAC (estimate at completion), and CPI (cost performance index) becomes business-critical in ensuring successful projects.
Project-based race car R&D and manufacturing
If any company could be said to exemplify the idea of a real-time enterprise, it would be Lotus F1 Team. The company develops the fastest possible race cars, an extremely complex product with more than 15,000 parts. Every race is treated as a separate project. Processes happen very quickly, with an immediate feedback loop from manufacturing and testing to design and engineering. Sensors on prototype models produce a massive data yield that engineers analyze. Starting with the aerodynamics division, Lotus F1 Team manages all design, manufacturing, and testing processes and data in Microsoft Dynamics AX and STAEDEAN Advanced Discrete Manufacturing. Later this year, the integrated solution will be rolled out to the entire operation. While the goals and operating environment of Lotus F1 Team are unique, many emerging real-time enterprises will adopt similar project-based, accelerated process approaches in their development, testing, and manufacturing.
The real-time enterprise is an important, interesting topic that I hope to return to in upcoming blog posts about product readiness and the interplay of design and manufacturing. In the meantime, I welcome your feedback and questions. Get in touch by contacting STAEDEAN.