Mobility in Manufacturing: 4 Avenues to Increased Effectiveness
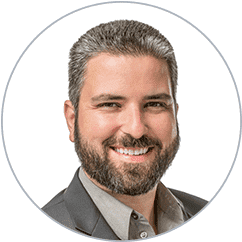
Table of contents
Mobility is ubiquitous. Almost everybody carries one or more mobile devices—smart phones, tablets, laptops being the most popular. Businesses have a huge opportunity to put mobility to work and make use of the devices their people already use to increase their productivity and competitiveness. That opportunity may even be more significant for manufacturing companies than many others. Let’s take a look at how mobility could benefit a manufacturing organization.
Let’s start with the assumption that your employees carry mobile devices, and that you have asked them to use their browsers or download an app to access business data from your ERP system. That, of course, implies that your ERP system supports mobile usage. Working solutions for this are widely available, including from STAEDEAN. You do need to make sure they fit your mobility business, and that people find them easy to use—or they won’t. The mobile software tools also should run equally well under the leading operating systems—Android, iOS, Windows Phone — and with popular browsers.
In our experience, people don’t like wasting time. It’s demotivating. More likely, your employees will be thrilled with the mobile capabilities you give them. By using their preferred mobile devices, they can enter their time and expenses as soon as they complete assignments or incur costs. If they perform certain tasks in the field, they can record their activities, project updates, comments, sales results, and more, and that information will reflect in the ERP system. If your human capital management (HCM) also connects with the ERP and mobile applications, payroll and financial details in HCM can be real-time complete and accurate. If you are a mobile manager running a mobile or remote team, you could also access the HCM system to review people’s skills and qualifications, and develop your workforce.
Here are a few areas of the business where manufacturers can take advantage of mobility:
Mobility and engineering: Timely change management
One of the key roles in almost any manufacturing company, the engineer, is often involved in tasks where mobility can make life easier. For example, when it comes to change management, it pays off to ensure that changes happen as early in the process as possible. The later they are made, the more expensive and complicated they become. Mobility can enable an engineer to record and transmit a change request from any device as soon as it presents itself. This could be at a customer site, the manufacturing floor, or almost anywhere else. Prompt recording and processing of a change request can make the following workflows much more efficient.
In that context, it would also help engineers to be able to look at pictures, drawings, and diagrams of equipment and parts while they are on customer locations or on the road. On their mobile devices, they could review assembly details and make sure that engineering change requests translate into the most effective next steps with great promptness and accuracy. They could even begin making modifications to parts or assemblies while they’re out in the field, while speaking with a customer. Of course, in customer or internal conversations, it would be most helpful if engineers could identify and source parts, along with costs and lead times, using the devices at hand.
Mobility and project management: Control and flexibility
Project and program managers need to be in control of their projects’ performance, delivery milestones, resources, and costs. Often, they find themselves on delivery and installation sites, or in facilities and situations where the only functional, connected technology is mobile. A project dashboard on a mobile device could immediately show performance to KPIs, help to assess and address risks in a timely manner, and verify critical dates and milestone achievements. The ability to review Gantt charts with project progress updates on a mobile device could also be very valuable. And, if project managers had the ability to review the current and projected earned value of their projects by means of mobility, they could be much more accountable to their companies.
Similar to engineers, project managers need to initiate change orders as a result of customer requests or the company’s R&D findings. Doing so demands adapting projects to changing conditions, tracking all the changes, and making sure projects proceed as customers expect. Mobile project management and information access could help ensure that changes flow into a project as soon as they become actionable.
Mobility and maintenance/services: Productive travels and efficient asset management
Maintenance and service specialists often spend months in the field, going from one customer site to the next. It’s most unusual for them to be at a desk with a computer. In the meantime, the home office updates maintenance schedules, customers’ needs change, and new parts and materials arrive. Seeing updated maintenance schedules and customer detail on a mobile device could save much time for busy technicians. Not only would they know what and where their next tasks are, they could also access material planning capabilities and pick the parts they will most likely need. Or, if they are reviewing a customer’s fleet or installed equipment that needs maintenance, they could schedule the appointment and also pick and ready the parts and materials for it. Check lists displayed on the mobile device could help ensure all parts and materials are available and that technicians take all necessary steps at the right time.
If technicians needed to see the lifecycle history of a customer asset, they could use their mobile devices to browse through records of past work, costs, and parts requirements, and they could also verify contract details and commitments in the same way. As they perform work, they could record their consumption of materials and parts in real time. Prompted by their mobile apps with the most likely locations and tasks, they could easily enter their time spent on assignments and make sure it is allocated to the proper account. Of course, taking notes in the field to track the fault liabilities of certain machines or keep the engineering team informed would be an easy task as well.
Mobility and inventory/warehousing: Faster, more accurate task performance
Warehouse and fulfillment workers are usually out and about. They pick, pack, and ship goods, or receive them at the loading dock and check them into inventory. Managers do what they can to make sure the internal movements and activities in the flow of inventory and goods are efficient. That sometimes means they need to make adjustments in staffing and tasks.
ERP data on a mobile device will help workers pick, pack, and ship the right items without needing to access stationary computers. If they can use a well-designed mobile app, they will also perform their jobs with minimal errors. Managers, in turn, could take advantage of mobility to review inventory histories and stock levels on the spot. They could also easily review the flows of items from the warehouse to production or through fulfillment and shipping, making timely adjustments to advance the productivity of people and processes.
Want to learn more about how we work with mobility solutions to manage ERP systems? Talk to an expert today!