Does My Manufacturing Business Need to Integrate PLM and ERP?
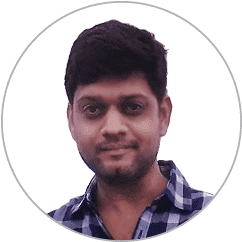
Table of contents
To evaluate the need for Product Lifecycle Management (PLM) and Enterprise Resource Planning (ERP) integration, you need to understand what these two systems can do individually and together. Over the last few decades, the manufacturing industry has seen a shift in focus from bulk production to more and more custom-made orders.
The rising demand for customized products alongside the constant need to maintain high quality and affordability has led to a new set of challenges for manufacturers. Now you have to produce a wide range of products in smaller batches and ensure they correspond with their relevant documentation to achieve a seamless supply chain. Complex products and ever-changing customer requests further add to the challenge.
A PLM-ERP integration solution helps streamline the product data flow to ensure cost-efficiency, accuracy, and a faster go-to-market.
PLM and ERP are two separate, yet, essential business systems that play a significant role in enabling a seamless, rewarding supply chain. Unfortunately, until recently, they stayed separated within an organization, and the world was oblivious to the power of their combination.
We’ve helped our customers bridge the gap between their designing and manufacturing systems through PLM and ERP integration for over a decade now at STAEDEAN. We understand the value of seamless integration between the two systems. Our customers already consider it a necessity because the most frequent questions we get asked are around:
-
How do we integrate, and what tools do we use?
-
How do we keep the integration up to date and robust?
-
Where do we find a partner with the right focus and experience?
If you’re a manufacturer trying to evaluate if your business needs a PLM and ERP integration, here’s a rather simple answer:
If you are maintaining the same data in both PLM (engineering team) and ERP (manufacturing team) systems, then integrating them will enable better data quality and a seamless supply chain.
However, to get a complete sense, let’s first understand what these two softwares can do individually and together, and how a PLM and ERP integration can benefit your organization.
The role of PLM in the manufacturing industry
Product Lifecycle Management (PLM) is an information system that helps coordinate the data and processes associated with the development of a product throughout its life cycle. It focuses on the entire life cycle of a product, from concept through disposal.
The operations in manufacturing begin with PLM, where product ideation, planning, and designing take place. This means a PLM system can collect all the information and data on the product elements, thus enabling an efficient product development process.
The role of ERP in the manufacturing industry
Enterprise Resource Planning (ERP) automates and supports an array of administrative and operational business aspects such as sourcing, accounting, logistics, customer or vendor relationships, etc.
ERP complements the PLM offerings further by focusing on the materials and physical assets in a supply chain. It collects, streamlines, and evaluates data to schedule production, manage inventory, pricing, and logistics. Therefore, it helps manufacturers automate and simplify complex operational processes. This enables cost-efficiency and enhanced business intelligence.
How are PLM and ERP different?
According to a study, leading companies were 40% more likely than average companies to have implemented PLM-ERP integration—indicating improved business performance.
The PLM and ERP systems offer different capabilities crucial for an effective supply chain. Combining and bringing them together on a single platform optimizes your efforts and streamlines all the supply chain processes from ideation, engineering, documentation to procurement, production, inventory, logistics, distribution, and delivery. Ultimately, PLM-ERP integration improves overall business efficiency and helps save cost and time.
What are the benefits of PLM and ERP integration for manufacturers?
1. Higher business efficiency
PLM-ERP integration can enhance process efficiency and productivity, thus helping you increase your company’s bottom line as well. You gain access to real-time data as well as see data transfer in real-time.
The PLM-ERP combination automates the process of updating and transferring data. Thus, your employees will no longer have to waste time on the mundane task of repetitive data input. They can utilize their valuable time in executing more business-critical, skill-relevant tasks, leading to increased productivity.
2. Cost reduction
The ability to save costs is one of the top benefits of PLM and ERP integration. When the data transfers automatically between both systems, the manual intervention is minimalized.
With increased data accuracy, a business can place their purchase orders more confidently, helping you avoid supply shortages and save money on excessive supplies. Furthermore, you can ensure the on-time delivery of orders without having to spend on hiring additional supply chain resources.
3. Higher customer satisfaction
Centralized data ensures higher visibility into your business operations, allowing you to recognize the potential areas for cost reduction.
Undeniably, when you minimize errors, efficiency increases, processes improve, and your customers are happier and satisfied. Despite the PLM and ERP functionalities supporting the internal systems, their combination can help increase customer satisfaction by fulfilling their orders quickly and accurately.
4. Improved collaboration
Seamless and clear communication among multiple departments is crucial for business success, especially in larger organizations.
System integration encourages the exchange of information between multiple departments, which can lead to surprising improvements in your business. Access to the overarching data of their business operations helps all the departments align better, increasing performance and productivity.
5 Key questions to evaluate your need for PLM-ERP integration
So far into the blog, you know how the PLM and ERP systems support separately and how their integration can be a game-changer for your manufacturing business.
Based on the top five challenges that our customers are overcoming with the help of our PLM-ERP integration solution, I’ve put together a few questions you could ask yourself to find out if you need to integrate your PLM and ERP systems. If your answer to one or more of the questions below is a “Yes”, integrating your PLM and ERP systems is the right way forward and can help enhance your business overall.
1. Do you see a lot of errors in data exchanged between your development and manufacturing teams?
Transferring data manually from one system to another can be a heavy workload on your teams.
It can further lead to a costly mistake, such as manufacturing the wrong product.
2. Do your teams complain about incomplete inventory or faulty components?
This can impact the product quality and even delay production.
3. Is it difficult to trace or track changes made to your products? (version management)
With custom parts and products, tracking all the details, including changes made to each version, is essential to ensure servicing and replacement whenever the need arises.
4. Does your procurement team struggle to get the right things in time?
With constant changes to the product and several versions created, procuring the right materials without clear, real-time specifications can be a problem.
5. Is there an evident disconnect among your engineering, manufacturing, and sales departments?
Collaboration between these teams is essential for faster and more reliable data flow to meet the ever-changing customer requirements.