A Manufacturer's Guide to Planning PLM Integration with Dynamics 365
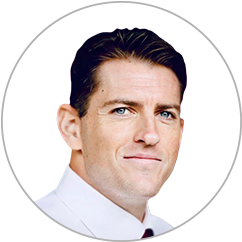
Table of contents
PLM-ERP integration is vital in streamlining communication and managing product data for manufacturers. But how do you integrate PLM and Dynamics 365 ERP? Are there some guidelines you can refer to before you connect the two systems? If you are looking for answers to these questions, you are at the right place.
With an experience spanning almost two decades of offering PLM integrations embedded in Dynamics 365, we have guided several manufacturing companies in preparing, implementing, and succeeding with the integration.
We have also created and shared plenty of information advising manufacturers on the best approach to integrating their PLM system with Dynamics 365 ERP.
This blog will take you through a collection of select topics, each offering unique insights into the end-to-end planning that goes into PLM-ERP integration.
You can read the summarized version for a quick overview or dive deep into each topic by clicking on the link provided at the end of each section.
Before we begin, if you'd like a quick refresher on the commonly used terminology while thinking, planning, and discussing PLM integration with Dynamics 365, click here.
How to plan PLM integration with Dynamics 365 ERP
1. Identify the need for PLM-ERP integration
If you are deliberating whether your business requires PLM integration with Dynamics 365 or how quickly you must integrate your systems, you’ll benefit from going through our checklist. You will find eight clear signs indicating your need to integrate your PLM and ERP systems.
Some of the signs are:
- You cannot keep different departments aligned.
- You incur repeated ad-hoc and unplanned costs.
- You have an inconsistent supply chain.
- You do not have time to innovate, research, and develop.
Know all the signs pointing toward PLM-ERP integration for your business here: Signs a Manufacturing Business Should Integrate PLM and ERP
2. Discuss internally to plan the PLM-ERP integration strategy
Before you begin looking for what kind of PLM-ERP integration solution your manufacturing business requires, you must have discussions with internal teams to sketch out the functional requirements. This need analysis will form the basis of your RFI (request for information).
Some key questions to ask your engineering team are:
- What is the format and type of the PLM data?
- How much legacy data exists in the current PLM system(s)?
- What logistical data is required while working on the product?
Get answers from your manufacturing team on the following:
- How many legal entities are we operating with?
- What data is needed from the PLM system to Dynamics 365?
- What is the data strategy post PLM-ERP integration?
For more insights, check out the blog: Questions to Ask Engineers and Manufacturers Before PLM-ERP Integration
3. Set the criteria to search and select a solution
When exploring solution options to integrate PLM with Dynamics 365, you must look for specific criteria matching your previously planned requirements. These factors will help define the project's strategic scope, and you can shortlist solutions based on this criterion.
Here are some factors to consider when integrating PLM and ERP:
- Functional requirements and features of the integration
- Scope of budget and expected return on investment (ROI)
- Implementation process and timelines
- Experience of the solution provider
Read this blog detailing the topic above: Factors to Consider When Selecting a PLM-ERP Integration Solution
4. Decide between building versus buying the integration
While you are executing the previous step of documenting the factors and features in a PLM-ERP integration, the next question that pops up is, "Do I develop the solution or buy it from an ISV?"
Building a PLM integration with Dynamics 365 ERP from scratch can be challenging with the development, planning, resources, and time that goes into it. On the other end, buying the integration will reduce the hassles of designing, coding, and maintenance.
This blog makes a comparison against factors such as:
- Solution testing and deployment
- Time required to implement
- Maintenance of the solution
- Innovation and futureproofing
See how developing the integration compares to purchasing it: Build or Buy PLM-ERP Integration for My Manufacturing Business
5. Prepare your business before the PLM-ERP integration
Once you have a defined set of considerations against which you will search for the integration solution, you also need to begin some preparation for a smooth transition. Iron out internal processes and shift your lens inward to see how you gear up for the upcoming PLM integration with Dynamics 365.
Some actions you can take include:
- Include cross-team collaboration
- Define the integration project specifications
- Set a repository to store information
- Use a unified channel for communication and updates
Get in-depth information on how to prepare your business here: How to Prepare Your Business Before PLM-ERP Integration
6. Migrate data for PLM-ERP integration
The importance of data migration is a recurring theme during all our customer interactions. Often, manufacturing companies look for integration solutions while not fully migrating to Dynamics 365 F&SCM or try doing both in parallel.
It's best to stay ahead of this to avoid any hassles once the implementation has begun.
The common data migration scenarios for Dynamics 365 F&SCM are:
- Moving from legacy ERP to Dynamics 365 F&SCM
- Moving from Dynamics AX to Dynamics 365 F&SCM
- Updating from Dynamics 365 without Engineering Change Management (ECM) to Dynamics 365 with ECM
Note: Dynamics 365 F&SCM was formerly known as D365 F&O (Dynamics 365 Finance and Operations).
Read this blog on the importance of data migration: Importance of Data Migration for PLM Integration with D365
7. Use benchmark processes for a successful PLM integration with D365
You've selected a solution that fits your needs and initiated procedures to begin the implementation. Follow these industry-based recommendations to ensure a smooth PLM-ERP integration, from research and analysis to going live.
Some of the best practices of PLM integration with Dynamics 365 are:
- Categorize your products to avoid overlap of data sets
- Identify the right internal and external people
- Follow a well-planned implementation methodology
- Facilitate and communicate change management
To know all the best practices, check this: Best Practices for PLM Integration with D365
8. Avoid common PLM-ERP integration mistakes
Once you get the ball rolling, you must beware of the common mistakes before, during, and after PLM integration with Dynamics 365. Stay informed of these errors and how to avoid them, as it costs your business additional money, time, and effort.
Some red flags to watch out for are:
- Unfulfilled prerequisites
- Not sticking to set timelines
- Missing to test the integration
- Repeated customizations
To understand the mistakes in greater detail, view this blog: PLM-ERP Integration Mistakes to Watch Out For
9. Refer to the dos and don'ts of PLM-ERP integration
Lastly, you can find the summarized list of the dos and don'ts of the integration. Keep this quick overview handy, as it will be a helpful guiding document to refer to throughout the integration process.
You can also share it with the relevant stakeholders from different teams, so everyone is educated on what should be done and avoided while connecting the two systems.
Some dos and don'ts to follow are:
- Do analyze your product data thoroughly
- Do train all the end users
- Don't neglect data ownership and maintenance
- Don't overlook data quality and data governance
For the complete list, access the blog here: A List of Dos and Don'ts During PLM-ERP Integration
Want to integrate your PLM/CAD system with Dynamics 365?
If an intuitive PLM-ERP integration solution with a short implementation time interests you, our solution could be the right fit.
Our out-of-the-box integrations for Dynamics 365 include ERP integration for PTC Windchill and ERP integration for Siemens Teamcenter.
If you are using any other PLM, PDM, or CAD systems, a configurable PLM integration framework is available, which can be adapted per your requirements.
You can explore more about our PLM integration for Dynamics 365 in the solution factsheet, which shares the following:
- What the integration solution can do for your business
- Benefits of PLM-ERP integration
- Features of a standard integration solution