Engineering Change Management (ECM) Solution: What are the top benefits?
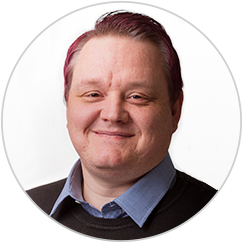
Table of contents
One of the biggest challenges in product engineering is keeping track of all the changes during the lifecycle of a product. Every time a new version is introduced this has impact on products, BOMs, routings, but also on existing supply chain transactions. Organizations must manage the change progress across the supply chain and that is where the biggest challenge lies. A good ECM solution supports product owners in arranging and aligning the communication needed to effectively make a change. This is done using an engineering change process.
So, how do you streamline change processes, track history of changes, lessen time to market and reduce costs at the same time? The answer lies in Engineering Change Management.
Here’s are top reasons why your company needs an advanced ECM Solution.
Version Management
When a product is created, it represents an idea becoming a reality. Often, this product will need adjustments based on feedback and experiences. Thus, it enters the product life cycle, and a need for tracking these improvements in the supply chain arises.
For a manufacturing company, it becomes crucial to manage that ever-growing size of immense data of various version of their products. When a customer faces problem with the older version of a product, the solution to it lies in the data. STAEDEAN’s Engineering Change Management now integrated within Microsoft Dynamics 365 for Supply Chain Management comes with version management, also called revision management – making history of changes traceable.
Improved Product Quality
Improving product quality starts with gathering innovative ideas from people throughout the internal supply chain. This process is supported using Engineering Change Requests (ECRs) and Engineering Change Orders (ECOs) in ECM.
Ideas can be captured in ECRs from Purchasing, Sales, manufacturing, after sales services and more, to document why a change is needed. ECOs can then be used to put changes in effect and document what changes were made.
Minimize Manufacturing Costs and Errors
Any process is said to be well-optimized and properly functioning when it assures less to no errors, taking less time to deliver, assuring no delay in the product launch. An ECM solution is doing that task for you. The time from engineering the product to production can be tedious as time-consuming, however with ECM there is reduced manual work related to entering product data in ERP systems, and hence low scope for errors.
Any company’s primary objective is to minimize manufacturing costs. Thus, the focus should be on aligning the process used in general engineering systems (can be PLM, PDM, CAD etc) with the process used in Dynamics avoiding data discrepancies and other production related issues.
Enhance Traceability with PLM
One of the top benefits of ECM is how well it integrates with general engineering external system (CAD/PDM/PLM). Using Product Lifecycle Management (PLM) software to manage engineering change brings efficiency in engineering change management (ECM). With PLM comes a centralized location for all the information on data and design, enabling traceability across all the domains and deliverables.
Improved ROI
Experience an improved ROI. With engineering change management capabilities, manufacturers can reduce manual errors through version control and product data management. With ECM, there is also transparency in managing documentation and traceability of all changes.
How to maximize ROI from Engineering Change Management implementation is also a question that customers would like to know. The answer lies here (link to factsheet)
Conclusion
An ECM solution is a bridging factor between engineering, operations and manufacturing processes. Every stakeholder gets notify about the task assignment and when it is due to review or needs update or approval for any change. When stakeholders are aware of the changes, they can also understand the consequences and take timely action.
That’s how a structured ECM effectively manages the impact of product changes and variances on bills-of-material, routings, and inventory in the system. Engineering change management thus helps in streamlining product lifecycle or end-to-end business process flow -- empowering the manufacturing cycle.