Discover How Activity-Based Costing Can Impact Your Manufacturing Business!
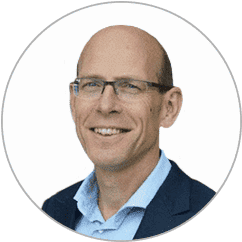
Table of contents
Activity-Based Costing is a term that many of us may not be familiar with and find scary and unachievable. However, that is not the case at all, and it is easy enough to achieve if you have clear understanding of how a manufacturing solution works within ERP.
Let us make this simple by defining what Activity-Based Cost means: It is the systematic allocation of overhead cost appropriately to each item that is manufactured and sold. As those of us who are familiar with the discrete manufacturing sector know, overhead costs are critical to proper costing of products, the total cost of production, and, thereby profitability. Overhead costs like electricity, consumables (gloves, lubricating oils, etc.), salaries, wages, sales and promotional expenses, research and development, etc. can form a substantial amount of money that has to be considered and apportioned appropriately.
While you cannot pinpoint what portion of these expenses specifically belong to the manufacture of a particular project, you can use your discrete manufacturing solution to record these. And the good news is that solutions like Industrial Equipment Manufacturing on the Dynamics 365 Business Central platform are capable of tracking accurate activity-based costing. The first and logical step would be to assign rates for resources like the work centers, engineers, the workers, etc. The next step would be to break this further into the Job Cost types so that you can get a summary of the costs at the job level.
To ensure that you are indeed considering all costs for the job, you can also have a budget to check the way your costs are panning out. As you add resources to a plan for a job, the costs of the resource get added to create a job budget. This way, when the job is carried out, the costs can be accurately calculated based on the time each human resource spent on the job. The same applies to consumables and other overhead variables.
The whole process of adding costs to the job plan forms the foundation of activity-based costing. Your manufacturing unit can benefit from inculcating these steps into your costing and manufacturing setup using an optimum Industrial Equipment Manufacturing solution. Project managers can then focus on their core job while the cost details are tracked in the system.
While the concept of overhead costs and the role they play in profitability is not new, it is a good practice to identify a solution that can help you track activity-based costing. What is more, when the solution also syncs with your ERP seamlessly, tracking of budgets, allocation of costs, and other related activities become more effortless.
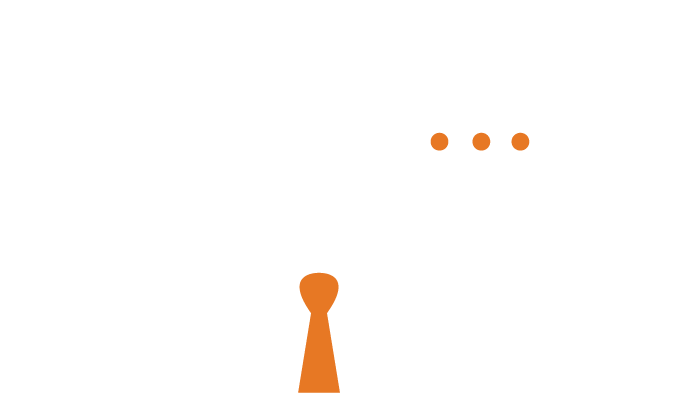