Custom Order Management: Understanding QRM vs Lean Manufacturing
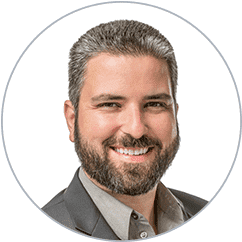
Table of contents
Building customized products for customers can be big business, but many manufacturers increase lead-time and decrease productivity when they create one-off products.
This isn’t a new problem, but one that needs a clearer path to higher productivity and more effective use of order management, as well as man-hours. Applying a lean manufacturing philosophy to custom production orders is hardly the answer: The concept often relies heavily on standardizing tasks to efficiently create items in quantity, while custom orders are by definition not a target of mass production. Quick response manufacturing (QRM), on the other hand, probably is the solution.
I’m not alone in this thinking. On Mbtmag.com, Mike Collins wrote why he thinks manufacturers should look at QRM and not lean manufacturing as the answer to produce custom products.
Collins writes:
“This does not mean that QRM is an alternative methodology that replaces Lean. Every manufacturer needs a good continuous improvement program regardless of the type of manufacturing. QRM simply complements Lean, Six Sigma and other popular methodologies. I just think that the QRM system is a better approach for custom product manufacturers who need to reduce lead times and labor hours.”
Building out custom products for your customers does require some rethinking beyond lean strategies. To this end, Collins goes on some key points about the differences between lean manufacturing vs. QRM:
-
Origin: Lean came from the Toyota Production System, for high-volume repetitive production. QRM was built from the ground up for custom products with low-volume.
-
Driver: The driver for lean manufacturing is the elimination of waste. The driver of QRM is the reduction of lead times, in part through better order management.
-
Organization Structure: This type of structure isn’t an objective of lean manufacturing, but it’s key to QRM. This helps the organization reduce lead times, as a different type of organizational structure can substantially reduce them.
To move on the path to success with QRM, Collins points out a few factors QRM could use for improved custom product development, manufacturing and order management:
-
Generalist vs. Specialist Employees – As Collins writes, in functional organizations, most employees specialize. What QRM needs is cross training for more employees to work on any machine or department.
-
Purchasing – Some customers may want specific materials for every process. This means new vendors and possible lead-time problems. Collins states how one company moved a buyer from one area to the division, there by purchasing could happen during the engineering process.
A main objective with custom development and production of specialized products is lead-time. To do this, efficiently, focus on a process that works with your current system – this is what QRM represents. When this is put into place, you not only experience shorter lead times, but increased profits and satisfied customers.
Stay up to date on how QRM contributes to order management, shorter lead times and helps organization run more efficiently: Subscribe to our blog updates, follow us on Twitter, like us on Facebook or connect with us on LinkedIn.