Can ERP Integration & IEM Technology Keep Manufacturing In The US?
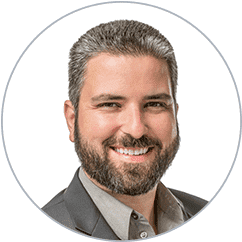
Table of contents
Globalization of manufacturing has generated significant interest and conversation in the Industrial Equipment Manufacturing (IEM) circle. And perhaps no recent article I’ve read on this topic is more impassioned than Can Highly Engineered Machines Be Outsourced, by Mike Collins of Manufacturing Business Technology.
Collins writes:
“In my opinion, it is almost impossible to achieve all of the requirements of a custom machine if it is outsourced to a foreign country. The communication required to engineer and assemble this kind of machine is an almost daily occurrence between the customer and the OEM engineers.”
Collins continues later in the article:
“I don’t see how a highly engineered machine with specifications or custom engineering can be outsourced to a foreign country (or an engineering department) without high risks for the customer and the OEM. With these kinds of machines I would suggest that as the amount of engineering increases the risk of mistakes and errors goes up logarithmically. If the problems are serious enough, the costs of fixing the machine will far exceed any savings from the outsourcing.”
While Collins makes valid points throughout his article, I don’t completely agree with his assertion that complex machinery manufacturing can not or should not be off-shored.
A more important and fundamental issue that should be focused on, in our world where off-shoring has become a reality, is tightening up the components of manufacturing processes that must be off-shored to reduce the risk of costly mistakes. And the answer for this challenge lies in greater integration of IEM technology.
Let’s use key points from Collins article to illustrate where greater integration of IEM technology can help:
-
The manufacturing process usually begins with a Request for Quote (RFQ) from the customer. Depending on the customer’s demand these specifications can include electrical, mechanical, hydraulic, pneumatic, programming, and even painting standards that will require special engineering for compliance.
Ultra-specific RFQs depend on real-time, unbroken chains of communication. The software solutions I represent, Microsoft Dynamics, include Technical Quotes functionality within its project management module – enabling all stakeholders to create, manage and communicate details related to complex bids and quotations in real-time with stakeholders anywhere in the world. The quote’s lifecycle can also be carefully managed and approved through the internal business process workflow engine by either internal or external stakeholders like the customer, the internal director or even the off-shore vendor.
-
In packaging machinery it is not uncommon for a large customer to expect a signed statement that the OEM will guarantee the uptime of the machine on a production line for 98.5 percent of the time on a three shift, seven day per week operation. Our solution offers an Enterprise Asset Management (EAM) / Maintenance Repair Operations (MRO) module that will allow the OEM to service agreements and maintain machines based on warranty or other work. Though I agree that in order to assure such uptime service level agreements there is a need for some local resources, it is not uncommon for local or abroad manufacturers to rely on local third party service providers for this work not requiring the manufacturer to be local.
-
Once the order is received and the drawings are all approved, the customer may have forgotten to add a specific requirement or they may change their minds and want something different. This happens by a “change order” requested by the customer, and they expect the changes to be integrated without changing the delivery schedule.
This is where Enterprise Resource Planning (ERP) / Product Lifecycle Management (PLM) integration comes into play, as well as our fully graphical planning engine.
When implementing our solutions, we help customers with ERP / PLM integration, ensuring their systems are able to exchange all necessary data – as well as mange their product specifications and lifecycle. We also manage all engineering change requests and engineering change orders, ensuring we reduce all waste, as part of the Product Engineering module we offer. This assures concurrent engineering processes spread throughout the world will also be directly connected to your transactional system to assure you minimize any mistakes. Meanwhile, keeping close ties between change orders and planning schedules so manufacturers can assure the projects are delivered on time.
Collins concludes his article:
“For highly engineered machinery, American customers still want the flexibility of ordering machines based on their plant standards and specifications that are very high quality and delivered on “written in stone” delivery dates that cannot be moved because of other contractors. Then once the machinery is installed they want 24 hour parts and service and a guarantee of 98 percent uptime.”
I could not agree more that complex machinery manufacturing requirements are only getting tougher. In some cases, it would be ideal to keep as much of the manufacturing process locally based as possible – and the same IEM technology that represents a global solution can be just as effective at tightening the processes within our borders. I understand this is no walk in the park. Whether you are local or not, the complex supply chain and tougher market demands only makes this process more complex. But that’s where having the right tools to aid you in making the right decisions will help you keep a competitive price without compromising the customer’s requirements.
But elimination of off-shoring is not always going to be the solution. Rather, the solution lies in tightening the chains around a project to the point that the notions of borders and coastlines disappear – and are replaced by the quantifiable concepts of real-time communication and global project visibility. Globalization is here to stay and fortunately, the IEM technology exists to make these very concepts a reality.
What are your thoughts on the globalization of manufacturing, its pros and cons, and how technology plays into the bigger picture? I encourage your feedback.
Stay up to date on the latest IEM industry insight by subscribing to our blog updates, following us on Twitter, liking us on Facebook or connecting with us on LinkedIn.