Data Best Practices for Virtual Pharmaceutical Companies
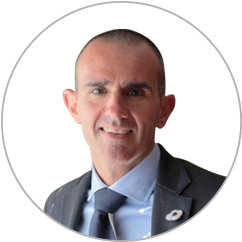
Table of contents
Gain control over your most important outsourcing activities with an easy-to-implement, configurable life sciences ERP solution native to Microsoft Dynamics 365.
Thousands of small companies drive a significant percentage of life sciences innovation. Armed with patented science and small management teams, these companies outsource operational tasks to prove the viability of new therapeutics and accelerate go-to-market timelines at a relatively low cost.
Because a mature outsourcing ecosystem exists to serve pharmaceutical companies, biotech firms, medical device manufacturers, and other life sciences organizations at every stage of development, a business model recognized as the virtual pharmaceutical company (VPC) continues to gain momentum.
VPCs have been around since the 1970s. Most famously, Genentech got its start as a VPC in 1976 and remained one until it set up an in-house wet laboratory two years later. Protodigm, founded in 1996, was the first life sciences company with the intention of remaining a VPC through its lifecycle. Drug Development World reported that “the company employed only nine people and it was estimated that they decreased both development times and costs by approximately 25% compared to fully-integrated pharmaceutical companies.”
Today, VPCs coexist—and often partner—with pharma companies that are fully integrated. Public-private partnerships offer incentives for establishing VPCs in the fight against rare diseases, and access to open-source data makes it easier for smaller entities to join the search for new therapies.
The most successful VPCs are comprised of experienced management teams that are experts at:
-
Finding the right partners (CMOs, CDMOs, etc.)
-
Understanding the regulatory requirements unique to life sciences
-
Orchestrating moving parts while maintaining financial control of the business
The Right ERP System Can Facilitate VPC Logistics
An enterprise resource planning (ERP) solution is essential for managing a complex operational system like a VPC. As a centralized, transparent source of up-to-date business intelligence, an ERP makes it easier for VPC management teams to coordinate activities related to finance, supply chain, manufacturing, quality, and compliance.
Regulations, in particular, are changing all the time. In 2012, for example, the Food and Drug Administration—in Section 501(a)(2)(B) of the Food, Drug and Cosmetic Act—made sponsors responsible for “the implementation of oversight and controls over the manufacture of drugs to ensure quality, including managing the risk of and establishing the safety of raw materials, materials used in the manufacturing of drugs, and finished drug products.” This addition put more of a burden on VPCs, because they typically have no direct role in outsourced processes, such as manufacturing.
So not only do VPCs have to find the best partners, but they also must monitor their partners’ activities and hold them accountable. With a strong ERP solution in place, VPCs are better able to ensure that these requirements are met. Unfortunately, traditional ERP systems generally can’t meet the stringent regulations and unique requirements of drug development companies without heavy customization.
Get Your Data House in Order Fast
Fortunately, VPCs that choose Microsoft Dynamics 365 as their ERP solution have a powerful option for tracking the development, testing, approval, and manufacturing of drugs and devices in a fully compliant way.
STAEDEAN extends the functionality of Microsoft’s revolutionary ERP solution by making it industry-specific, compliant, and fully validated for life sciences organizations.
Via configurable native modules—with no complex customization work needed—the STAEDEAN solution makes it easy for life sciences organizations to bring new components online and integrate with third-party sources for everything from laboratory information management to advanced warehouse management capabilities. The fully vetted solution has been evolving for nearly 18 years, based on the systems and life sciences experience that the STAEDEAN team brings to the table.
Get Up and Running in as Little as 6 Months
While it’s not a VPC, the pharmaceutical company INOVIO turned to STAEDEAN for an ERP upgrade during COVID-19. The fully remote implementation replicated the typical VPC environment, and it was completed and validated in just six months and six days.
STAEDEAN has become INOVIO’s gold standard for data, and executives at the company like that they can quickly turn on individual components as they need them.
The STAEDEAN platform is ready to use out of the box without customizations, and a team of experts continually tests the software against each release from Microsoft, so you don’t have to worry about version updates impacting your business.
For many years, both VPCs and traditional life sciences organizations have had to solve challenges posed by their unique processes and strict industry regulations on their own. With STAEDEAN, leaders at life sciences organizations—including the top five pharma companies—have a fast, flexible, and affordable way to streamline processes and optimize compliance.