3 Examples of How PLM-ERP Integration for Dynamics 365 Improves Business Operations
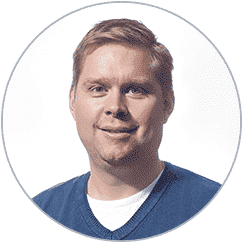
Table of contents
PLM and ERP are two of the most common software systems in the manufacturing world. While it is typical for businesses to conduct various processes in their PLM and ERP individually, having the two systems disconnected could lead to operational delays and unforeseeable errors.
In our experience of almost two decades in the manufacturing industry, we have often been asked how to address the issue of siloed PLM and ERP systems. Connecting the two systems with an integration could enhance the productivity and efficiency of your manufacturing business multifold.
And that’s what we offer at STAEDEAN, a PLM-ERP integration solution embedded in Microsoft Dynamics 365 for Finance and Supply Chain Management.
In this article, you will discover three business examples (inspired by our customers) of how our PLM-ERP integration improves operations and streamlines communications.
3 Business scenarios where PLM-ERP integration addresses challenges and improves operations
Scenario 1: Company A using Agile PLM and D365 F&SCM ERP
Company profile
Company A is a manufacturing company with an international presence. They have a multi-level supply channel set up and deal with numerous suppliers.
Challenge
Company A had an old ERP system, which involved a lot of custom coding and costly licensing. They were stuck on an outdated version of the ERP and faced issues with software maintenance.
The team at Company A was looking for a solution that would offer the latest software, enhance their global supply chain management, and streamline their processes. They were seeking a PLM-ERP integration solution to track and transfer data from their Agile PLM system to the ERP.
Company A's first step was adopting a new ERP system that offers a wide range of standardized functionalities. They adopted Microsoft Dynamics 365 F&SCM (also known as F&O) as the new ERP system, given its technology scale and modernized capabilities.
However, they could not connect their PLM to the D365 F&SCM ERP as it could not support integration with the Agile PLM.
Solution
After conversations with several integration providers and discussions, Company A selected STAEDEAN’s PLM-ERP integration solution. They activated the engineering change management (ECM) functionality within D365 F&SCM, a prerequisite for our integration solution.
Our integration solution could bring all the required data from their PLM system, Agile, into the ERP. They were able to have all the desired functionalities with a quick implementation time.
Company A’s team could go live on time and conduct their manufacturing operations more efficiently.
Transformation
After implementing our PLM-ERP integration solution, Company A transformed its business to achieve the following:
-
Capacity to ascertain the most recent revisions of all their parts
-
Complete visibility into the status of each version across the supply chain
-
More control over supply chain operations
-
Specify whether a particular item can be used in different processes
-
Save time and money by avoiding inaccurate shipping of an item at the wrong lifecycle
-
Make alterations through simple configuration and consistently meet their evolving needs
-
Enhanced collaboration among all supply chain stakeholders
-
Visibility on items, item fields, bill of materials, status, reporting, etc.
Business impact
The PLM-ERP integration enabled a free flow of data between the PLM and ERP systems of Company A. With integrated systems, they gained complete control over various activities.
Today, Company A is running a profitable business and is able to save time and cut down costs due to quicker processes. The scope of errors associated with manufacturing has drastically reduced with better communication, and their overall supply chain efficiency is improved.
Scenario 2: Company B using Siemens Teamcenter PLM and Dynamics AX 2012 ERP
Company profile
Company B is a manufacturer of make-to-order advanced equipment. With national operations, they develop complex equipment for their customers and have a strong presence in the project-based manufacturing industry.
Challenge
Company B had been using one ERP system for a long time. After a few years of usage, their ERP provider was acquired by another company, which meant that the ERP system could no longer be enhanced and supported.
They were using Siemens Teamcenter as their PLM software to handle their engineering processes but were challenged to manage the manufacturing side of their businesses, considering their ERP had reached its end of life.
Company B immediately began searching for a new ERP solution to achieve more effective workflows, and they decided to implement Microsoft Dynamics AX 2012 as it met their requirements.
With the new ERP in place, the company now had to consider software that would be able to integrate their Siemens Teamcenter PLM to Dynamics AX 2012 ERP.
They tried to import some data from their PLM to the ERP by building a connection, but it did not work due to a lack of technical expertise. This made Company B realize the significance of a robust, standardized integration, which is what they sought.
Solution
After implementing Dynamics AX 2012 with one of our partners, Company B discovered our PLM-ERP integration solution. Despite speaking with other ISVs, they selected our solution, as we built ‘Product Engineering’ within Dynamics AX 2012 to manage product versions and changes.
They trusted us as the best bet for taking care of their business needs and offering them the most innovative technology.
They activated Product Engineering within their ERP system and implemented our out-of-the-box PLM-ERP integration solution for Siemens Teamcenter.
With our standardized integration solution, they achieved their goal of going live quickly and streamlining communications.
Transformation
After implementing our out-of-the-box PLM-ERP integration solution, Company B was able to achieve the following:
-
Time savings in transitioning from design to production
-
Timely customer delivery
-
Meet their strategic short and long-term goals
-
Easy maintenance of the solution
-
Save costs from multiple process improvements
-
Increase customer satisfaction and improve customer relationships
-
Enhance revenue generation and increase profitability
-
Stronger competitive positioning in new markets
-
Complete visibility into the status of each version across the supply chain
Business impact
With a standardized PLM-ERP integration solution available out of the box, Company B’s integration solution was operational in no time. They continue to reap the benefits of streamlined manufacturing processes.
Our integration and product engineering solution helped them improve their workflows between design, engineering, and production teams.
![]() |
To discover our out-of-the-box PLM-ERP integration for Siemens Teamcenter and D365 F&SCM.
|
Scenario 3: Company C using 3DX Dassault and other PLM systems and D365 F&SCM ERP
Company profile
Company C is a global leader in designing and manufacturing aerospace equipment. With a presence in multiple continents, they are a worldwide premier supplier of automated equipment to the aircraft industry.
Challenge
With a strong philosophy of enhancing performance, Company C gained considerable growth in the past two decades, leading to production and financial process strain. Previously, they used an ERP system, which met their primary business needs but could not analyze revenue, forecast costs, or run financials.
The team at Company C decided to invest in another ERP that could handle their growing business and multiple international processes. After their due diligence, they invested in Microsoft Dynamics 365 for Finance and Supply Chain Management as it offered a wide range of standardized processes, including invoicing and accounts payable processes.
With a newly implemented ERP, they could meet most of their business requirements. However, specific processes were still not streamlined, such as communication between the ERP and PLM, which made them realize the need for an integration tool as it wasn’t available out-of-the-box in standard D365.
Solution
One of our partners had implemented D365 F&SCM for Company C, and the partner collaborated with us to address Company C’s remaining business requirements.
The capabilities and features of our PLM-ERP integration solution impressed Company C as it ensured data quality, and they felt it was a robust solution for their business.
They were able to build a seamless connection between multiple PLM systems, including 3DX Dassault PLM, to the D365 F&SCM ERP.
Transformation
Post the implementation of our PLM-ERP integration solution; Company C enhanced its business in multiple ways, some of which are:
-
Visibility into each customer’s project, from cost to materials supply chain
-
Better overall project management
-
Easy maintenance of software in line with Microsoft’s upgrade policies
-
Controlled costs with process automation
-
Enhanced user experience with a unified, standardized, and embedded solution
-
Successful digital transformation of their business
-
Improvement in profitability and supply chain agility
-
Scalability with a future-proof solution
Business impact
Our software enabled a smooth and sophisticated connection of their PLM systems to D365.
They were also able to create configurations between various systems, saving them time, the effort of expensive customizations, and additional implementation costs. They continue to utilize our integration framework to transfer data into and out of D365 in a reliable and repeatable manner.
Are you considering integrating your PLM and ERP?
Above, we have shared three success stories of how our PLM-ERP integration solution drastically improved operational efficiency for manufacturing businesses in varying industries.
If your business is facing similar challenges with disconnected PLM and ERP systems, a standardized PLM-ERP integration solution is the way to go.
This table shares a quick overview of the cost, time, and effort you’ll save buying a standard integration like ours over developing it.
Our solution can support integrations for all PLM systems with the ERP Dynamics 365 F&SCM (which requires ECM) or Dynamics AX 2012 (which involves product engineering).
We offer out-of-the-box PLM integrations for Siemens Teamcenter and PTC Windchill. We also have experience in PLM integrations with 3DX Dassault and other PLM, PDM, and CAD systems with a configurable PLM integration framework.