What are the types of Inventory counting? How to select the best one
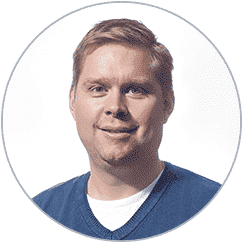
Table of contents
Don’t we all know how important the counting of inventory is in the warehouse and the store! It is the process of validating the quantity you have in your ERP software against the actual quantity on the shelves, and it is crucial to do it meticulously because not all physical movements are updated in the system. As an ERP expert, let me help you with types of Inventory counting and the intricacies involved with each method.
In this article, I will be talking about the difference between various counting mechanisms and to choose the best for your business. We’ll cover:
- What are the reasons for discrepancies in inventory counting? How barcode scanning helps.
- What are the different types of inventory counting? What are their advantages and challenges?
- What are the benefits of using an ERP solution? How to combat challenges in inventory counting methods?
What are the reasons for discrepancies in inventory counting? How barcode scanning helps.
There are various reasons for discrepancies, some of them being: breakage, theft, registering wrong quantity, scanning the wrong item or the wrong location, moving items between shelves without registering that in the system, etc.
Using barcode scanners improves the quality of your inventory data quite a bit, but still, errors can happen.
Of course, preparation in advance is the best way to decrease discrepancies. For instance, you can ensure you have barcode labels on all your items and locations, implement barcode scanning in all your warehouse processes, also take into consideration the quality of your people in the inbound area (they are the most important ones!), etc. To avoid or minimize errors at the inbound make sure you have best team players when the stock enters the warehouse, assuring smooth functioning of warehouse operations.
Once you’ve dealt with these inventory management techniques, there’s still the method of inventory counting you have to master.
What are the different types of inventory counting?
Some of the most-used types of counting are cycle counting, spot counting (sometimes also known as ad-hoc or blind counting), and tag counting.
Let’s see what the existing differences between various types of counting are, and under what situation which counting method is the best.
Cycle counting
As the name implies, cycle counting is about counting in cycles. You do not count your full inventory at once but do it in parts.
A different part of the store or warehouse is counted every month, week, or day. It can be based on product types, product group, warehouse/store zones. And for each differentiator, you may decide on different cycle lengths. For example, small-sized, fast-selling items should be counted more often than the big kitchen appliances.
What are the advantages?
Cycle count could remove the need to execute that frightening annual count – which is typical for most companies. With the cycle counting method, you can distribute the workload throughout the year instead of putting all efforts on that one weekend.
Cycle counts are easier to plan, and in fact, your ERP can create counting orders for you based on your rules and stock changes. This approach will also give you interesting and detailed reports which you will be able to analyze not only against previous years but also to compare different periods of the years.
For example, you may notice more significant discrepancies in the period, when you sell less and order more (hence a problem in the inbound), which could be surprising for you after always blaming the high workload during high season for the inevitable mistakes.
What are the challenges with cycle counting?
When not counting everything, there is always a risk to miss items when creating the counting orders, so planning is critical here. Another downside is that counting becomes part of the daily routine of your employees, and they can easily be distracted (e.g., when a customer comes to them) and forget to count something or count it twice.
As cycle counting could be happening on a daily basis, it may force you to do it in open hours, but in this scenario, there is always the possibility that items included in the counting orders could be sold or shipped before being actually counted. The advice would be to plan the counting at the beginning of the day.
Ad-hoc counting
Ad-hoc counting is initiated by the user and is usually not planned, meaning this counting is quite handy in extraordinary situations.
Say you have counted a zone, but due to somebody or some process, the system went awry a few days later. In this situation, you can just create a new empty order and start adding counted items in it, instead of waiting for the next cycle count to come.
Of course, your system should be capable of matching the counted quantity against what is in the software. Because ad-hoc counting is usually used for small store/warehouse areas or zones and is unscheduled, it is also known as spot or blind counting.
What are the advantages?
Ad-hoc counting gives you more flexibility to tackle emergencies and overcome the drawbacks of bad cycle count planning. The analysis and outcome of ad-hoc counting could help you adjust your cycle count scheduling more precisely. Don’t forget the human factor is always needed in unplanned situations.
What are the challenges with ad hoc counting?
The challenge here is the same as the advantage, which is the human factor. If your employees are not cautious enough, they may not trigger ad-hoc counting even when they identify a need for that.
Tag counting
In preparation for tag counting, the store/warehouse employees should place a physical tag on each item. During counting, the worker must fill in the item ID, counted quantity, and other relevant information on the designated spaces on the tag. Some tags have two sides, so that a second worker may validate the information and, if needed, fill in the correction on the second side. After the counting is processed, these tags are collected and entered the system as journals.
The main difference between tag counting and all other counting methods is that, with it, you do not immediately compare against the system data. It is more like preparing a preliminary draft list of your items and quantities, polishing it (e.g., adjusting with sales which have happened during the counting), and then just creating a counting order and matching it against the tag counting list.
What are the advantages?
Tag counting is very suitable for stores, where usually there are no locations like a proper warehouse, or for bulk warehouse zones.
When there are no locations, and lots of items, it becomes difficult to track the counting process. In this situation, tags solve this issue, giving you visual information about what is counted and what is not.
An even better approach is to use scanners during counting. In this way, you can scan the tag ID together with item and quantity and then just put the physical tag on the item so that it can be recalled later that it has been counted. The journals will be immediately created, and there will be no need to enter them manually.
Furthermore, most ERPs don’t create transactions for tag counting, meaning your items will not be blocked, and you can execute counting in open hours. Just keep track of the inbound and outbound movements during the counting period and then adjust accordingly in the tag counting journals. After polishing the data, post the journals, and just then, the counting transactions will be created.
What are the challenges with tag counting?
Tag counting may not be suitable for all kind of businesses, but if you can implement it in your company, then it really is undoubtedly one of the best ways for inventory counting, giving you transparency, freedom and accuracy.
How does Anywhere mobility studio STAEDEAN solutions help combat challenges in inventory counting
Inventory management is the lifeline of your warehouse operations. Anywhere for Retail and Anywhere for Logistics, powered with Microsoft Dynamics 365FO, are mobile solution for retail stores, and warehouse management, bringing ease and efficiency to your overall in-store and warehouse operations.
The challenges you can overcome with STAEDEAN’s Anywhere for Retail and Anywhere for Logistics are:
- Optimizing various stock counting methods, reducing your efforts, and controlling costs.
- Enabling better control over inventory or stock counting.
- Planning store/warehouse capacity and maintaining inventory level.
- Tracking who, when and where did the stock counting.
There is no denying that inventory management is quite taxing with rising customer expectations and smart competitors around. However, stock or inventory counting is also crucial for the fundamental inventory process without which your business can’t prosper.