Extending IoT-connected, cloud-based collaboration around machinery
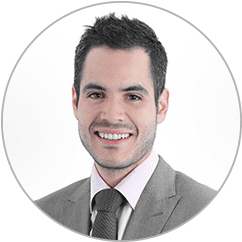
Table of contents
The most innovative machine manufacturers are already finding ways to use the cloud and the internet of things (IoT) to provide machine services that go far above maintenance and gradual enhancements. Effective collaboration among machine makers and their customers can begin as soon as a concept and need for a piece of equipment exists. Cloud-enabled, integrated ERP, PLM, PDM systems and processes play a key role in bringing this about.
In a recent blog post about the IoT, my colleague Luciano Cunha talks about collaborative innovation scenarios that connect machine manufacturers and their customers. Working together, taking advantage of cloud- and IoT-enabled ERP, they make sure that timely maintenance happens so equipment assets perform at their best level. They also use the technology to facilitate the design of incremental innovations for the machinery.
Those collaboration scripts assume that there is equipment installed that requires maintenance or presents opportunities for improvement. But what if the equipment does not yet exist? The process really can start as soon as there is an idea and people in a company brainstorm about the kind of machinery that would be best.
Building a collaborative product lifecycle cloud
Long before you have defined all your needs and landed a suitable vendor, you can use the cloud to gather all of your contributors’ ideas and requirements for a certain machine, and invite trusted advisors whenever you want their participation. Think of it as an early form of what will eventually be the product cloud with IoT sensor data regarding the machine’s performance and utilization, shared between you and the equipment maker.
At the right time, you make your requirements available to potential vendors and machine manufacturers through the same cloud, where they can ask questions, offer input, and share their initial ideas regarding feasibility, cost, and timelines. The process can continue as the machine undergoes design and prototype production, with different business groups involved in the machine manufacturing company. Eventually, when the machine is ready, the deployment team gets involved, helping the customer get the facility ready for it. At that point, or likely earlier, customer contacts can also download a mobile app that lets them access the product cloud and engage with the manufacturer’s engineers, sales reps, and production managers, from their favorite devices.
As an equipment vendor, you can engage in a similar collaboration with the suppliers and trading partners from whom you source your components and materials. You can also make your dynamic product catalog available in the cloud. Documentation and training materials you create for the equipment are also stored and maintained in the product cloud. As the machine is installed and runs at the customer site, this content can be updated with actual performance data and insight from the customer experience, like a proprietary, machine-specific wiki. Employees can access it whenever they need to, and refer to it when they need to use or service the equipment.
Changes in the way organizations and systems work together
As you see, to make this lifecycle approach to cloud-enabled machine management work, manufacturers and their customers will, at least to a degree, perforate organizational boundaries and infrastructures, and agree on the right security protocols and IP protection for their collaboration. Throughout the life of the equipment, from conception, to production, to deployment and continued innovation, they need to define the roles and accountabilities involved on both sides—including the shared ownership of shared IP to do with product features and innovations, as well as the product cloud itself and the resources it provides. Business process management (BPM) with a solution like STAEDEAN RapidValue can help them design roles and processes, and align cloud-based, mobile, and on-premise systems, to accomplish this.
Success in collaborative product innovation, design, and continuous improvement also requires that product lifecycle management (PLM), product data management (PDM), and ERP systems become integrated and cloud-enabled. STAEDEAN is deeply involved in readying its technologies to help companies make this transition smooth, secure, and economical.
Some companies, like RapidValue customer Komatsu in its Australian operations, are far ahead in creating and deploying cloud technology to provide machine services. KOMTRAX, created by Komatsu Australia, is a monitoring system for high-cost, large machinery, often used in mining. KOMTRAX involves satellites to facilitate communications. Using a mobile app or web services, customers can review the locations, performance, utilization, security, and activity of the IoT-connected Komatsu equipment they use, on their screens. Komatsu also recently entered into an agreement with telecom provider Telstra to further advance the cloud and machine-to-machine (M2M) technologies that Komatsu will use to make its machine services ever more powerful and competitive.
Clearly, Komatsu reached a point where the cloud and IoT investments on behalf of its customers made good sense. Many companies today are charting their own way toward the collaborative machine cloud, and not all of them are manufacturers. Leading construction companies, professional services organizations, fishing fleets, and many others are moving in this direction. I hope we can share some of their exciting stories with you as they happen. If you want to share ideas and feedback, please contact us.
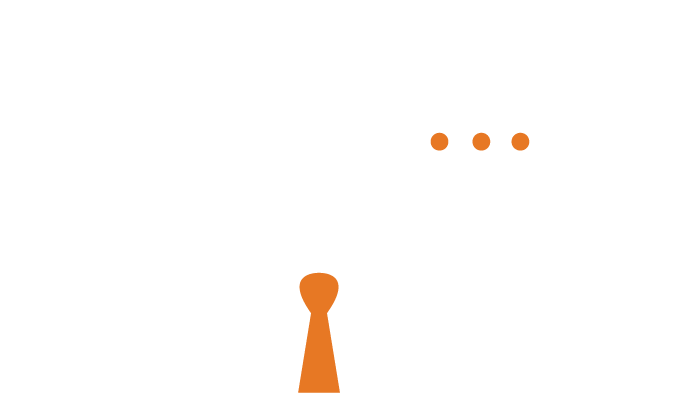